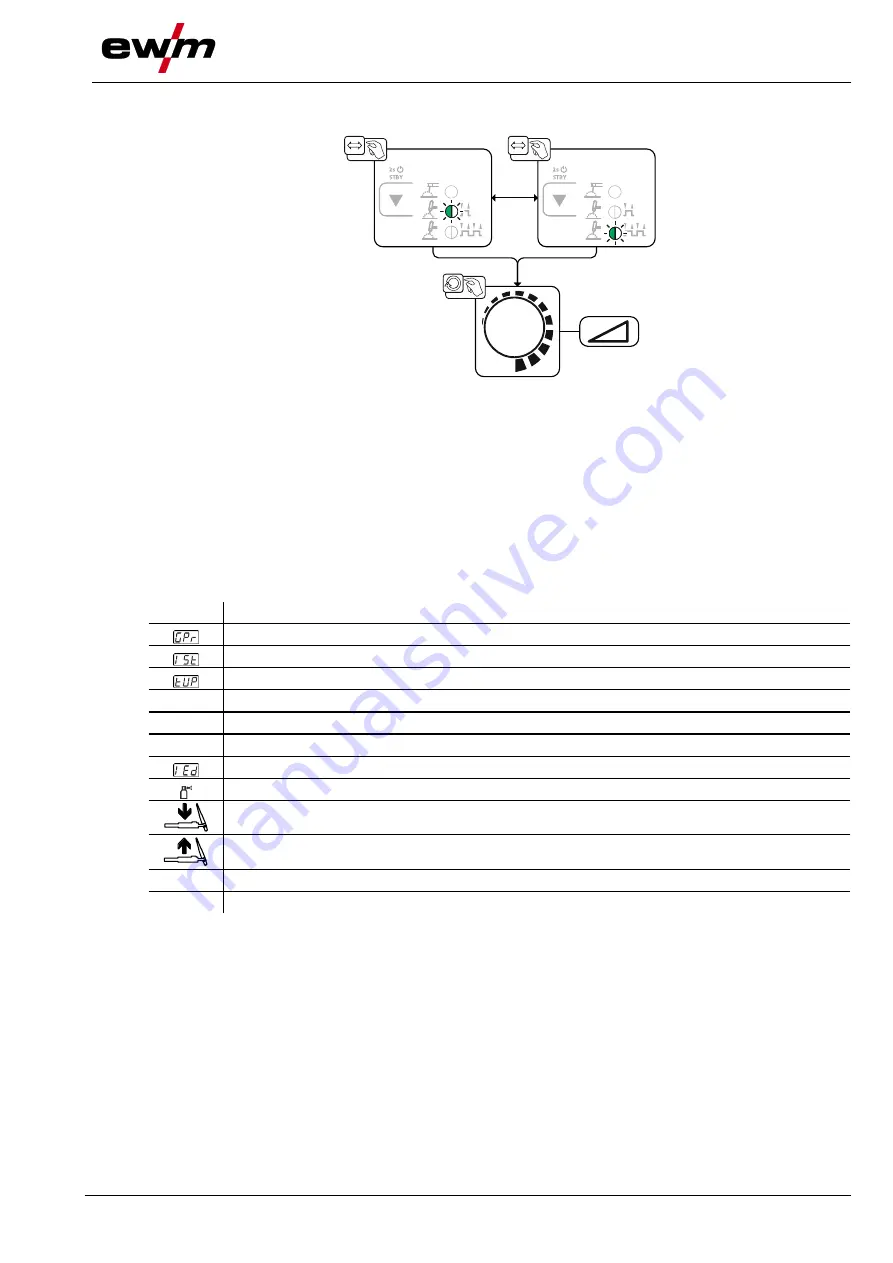
Design and function
TIG welding
099-002058-EW501
26.11.2020
27
5.2.4 Welding task selection
Figure 5-12
This completes the basic settings and you can now start welding.
Further welding parameters, such as gas pre-flow time, are predefined for the most common applications
but can be adjusted when necessary
> see 5.2.8 chapter
.
5.2.5 Operating modes (functional sequences)
Using the welding parameter push-button and welding parameter setting rotary knob the sequence para-
meters are set.
By pressing the "select welding parameter" push-button for approx. 2 s you can access the advanced set-
tings and optimise further parameters for your welding task
> see 5.2.8 chapter
.
5.2.5.1 Legend
Symbol Meaning
Gas pre-flow
Ignition current
Up-slope time
AMP
Main current
AMP%
Secondary current
t
Down
Down-slope time
End-crater current
Gas post-flow time
Press torch trigger 1
Release torch trigger 1
I
Welding current
t
Time