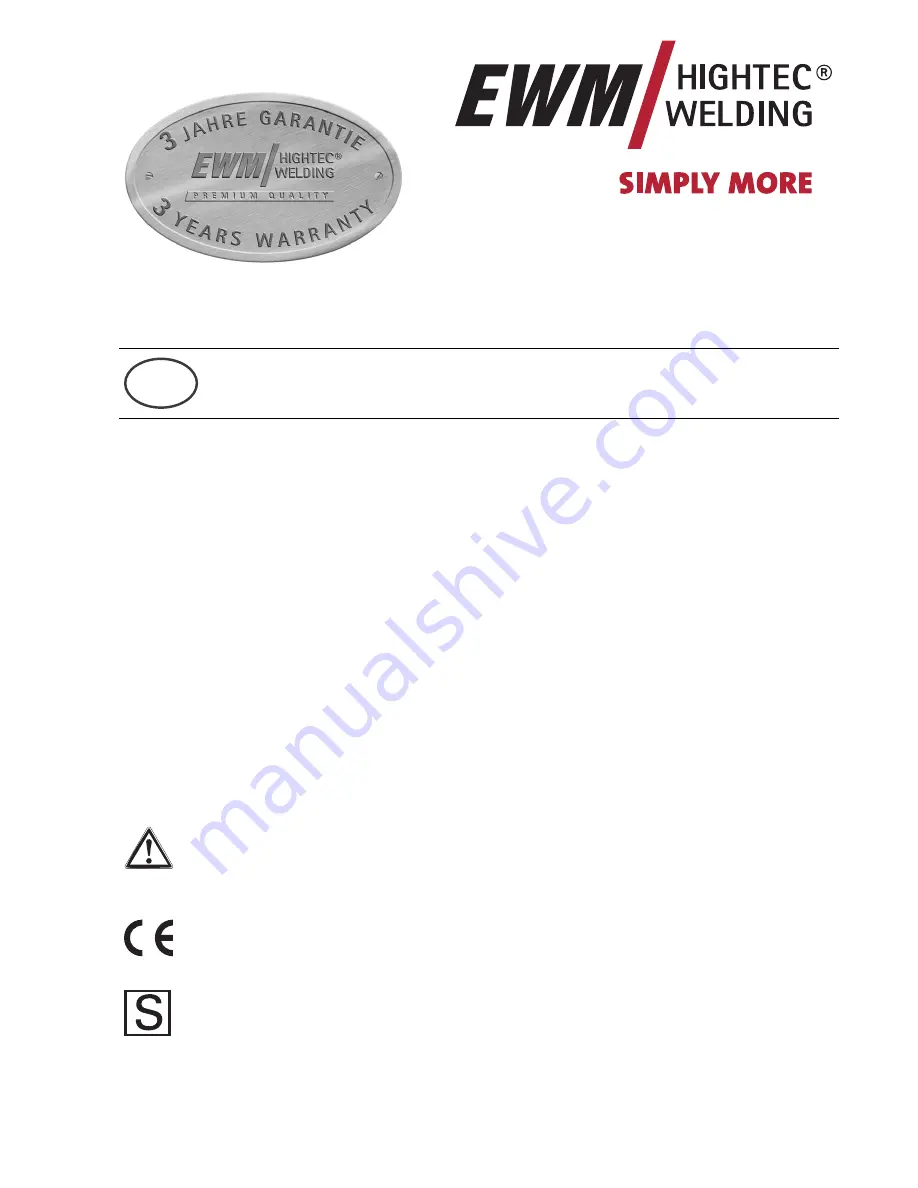
EWM
HIGHTEC WELDING GmbH
Dr. Günter - Henle - Straße 8 • D-56271 Mündersbach
Phone: +49 2680 181 0 • Fax: +49 2680 181 244
www.ewm.de
•
GB
Operating instructions
Compact welding machine for MIG brazing and
MIG/MAG welding
PHOENIX 301 CAR EXPERT PULS
N. B. These operating instructions must be read before commissioning.
Failure to do so may be dangerous.
Machines may only be operated by personnel who are familiar with the appropriate safety
regulations.
The machines bear the conformity mark and thus comply with the
• EC Low Voltage Directive (73/23/EEC)
• EC EMC Directive (89/336/EEC)
In compliance with IEC 60974, EN 60974, VDE 0544 the machines can be used in environments
with an increased electrical hazard.
© 2006 Subject to alteration.
Item No.: 099-004998-EWM01
Revised: 25.09.06