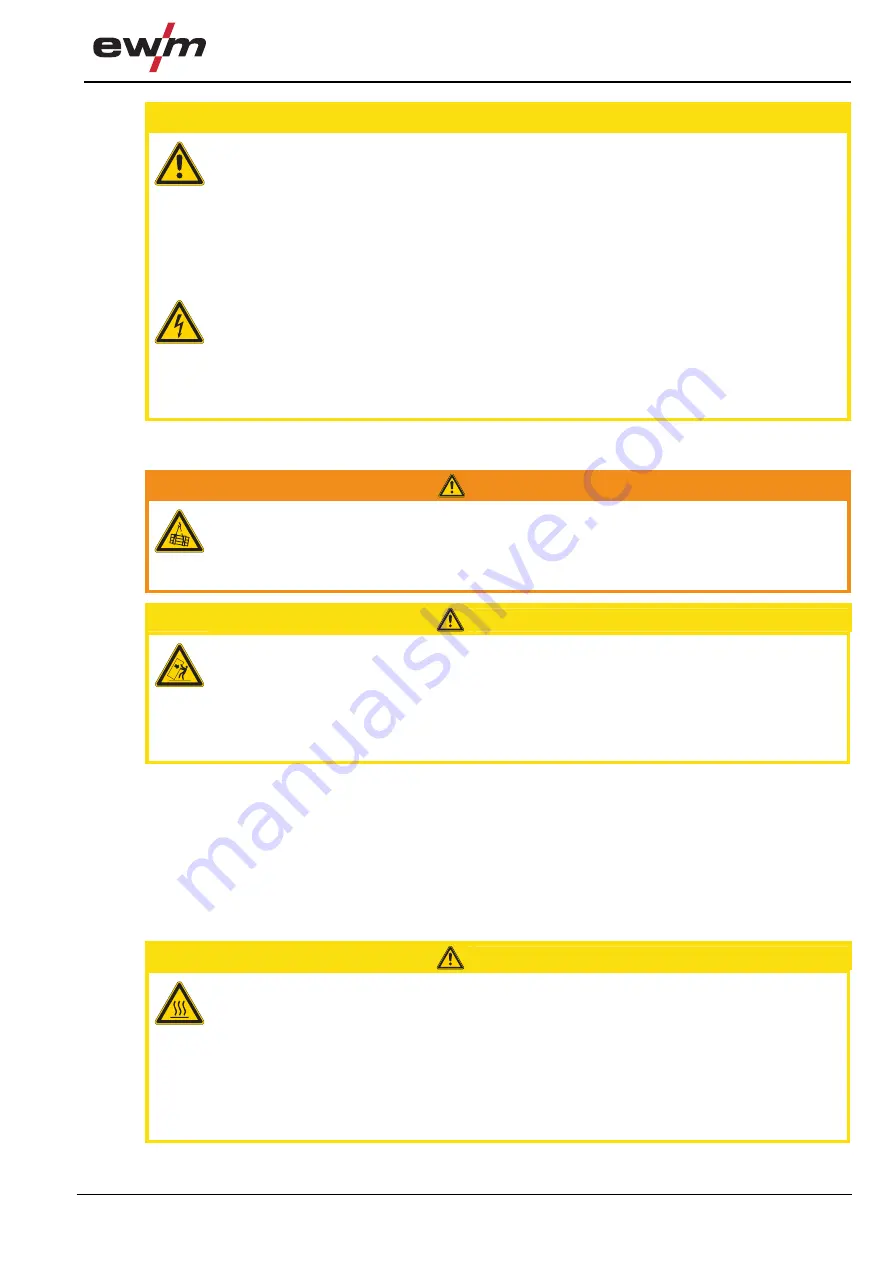
Design and function
Installation
099-005084-EW501
22.09.2011
23
CAUTION
Damage due to incorrect connection!
Accessory components and the power source itself can be damaged by incorrect
connection!
• Only insert and lock accessory components into the relevant connection socket when the
machine is switched off.
• Comprehensive descriptions can be found in the operating instructions for the relevant
accessory components.
• Accessory components are detected automatically after the power source is switched on.
Using protective dust caps!
Protective dust caps protect the connection sockets and therefore the machine against
dirt and damage.
• The protective dust cap must be fitted if there is no accessory component being operated
on that connection.
• The cap must be replaced if faulty or if lost!
5.2
Installation
WARNING
Risk of accident due to improper transport of machines that may not be lifted!
Do not lift or suspend the machine! The machine can fall down and cause injuries! The
handles and brackets are suitable for transport by hand only!
• The machine may not be lifted by crane or suspended!
CAUTION
Installation site!
The machine must not be operated in the open air and must only be set up and
operated on a suitable, stable and level base!
• The operator must ensure that the ground is non-slip and level, and provide sufficient
lighting for the place of work.
• Safe operation of the machine must be guaranteed at all times.
5.3
Machine cooling
To obtain an optimal duty cycle from the power components, the following precautions should be
observed:
•
Ensure that the working area is adequately ventilated.
•
Do not obstruct the air inlets and outlets of the machine.
•
Do not allow metal parts, dust or other objects to get into the machine.
5.4
Workpiece lead, general
CAUTION
Risk of burns due to incorrect connection of the workpiece lead!
Paint, rust and dirt on the connection restrict the power flow and may lead to stray
welding currents.
Stray welding currents may cause fires and injuries!
• Clean the connections!
• Fix the workpiece lead securely!
• Do not use structural parts of the workpiece as a return lead for the welding current!
• Take care to ensure faultless power connections!