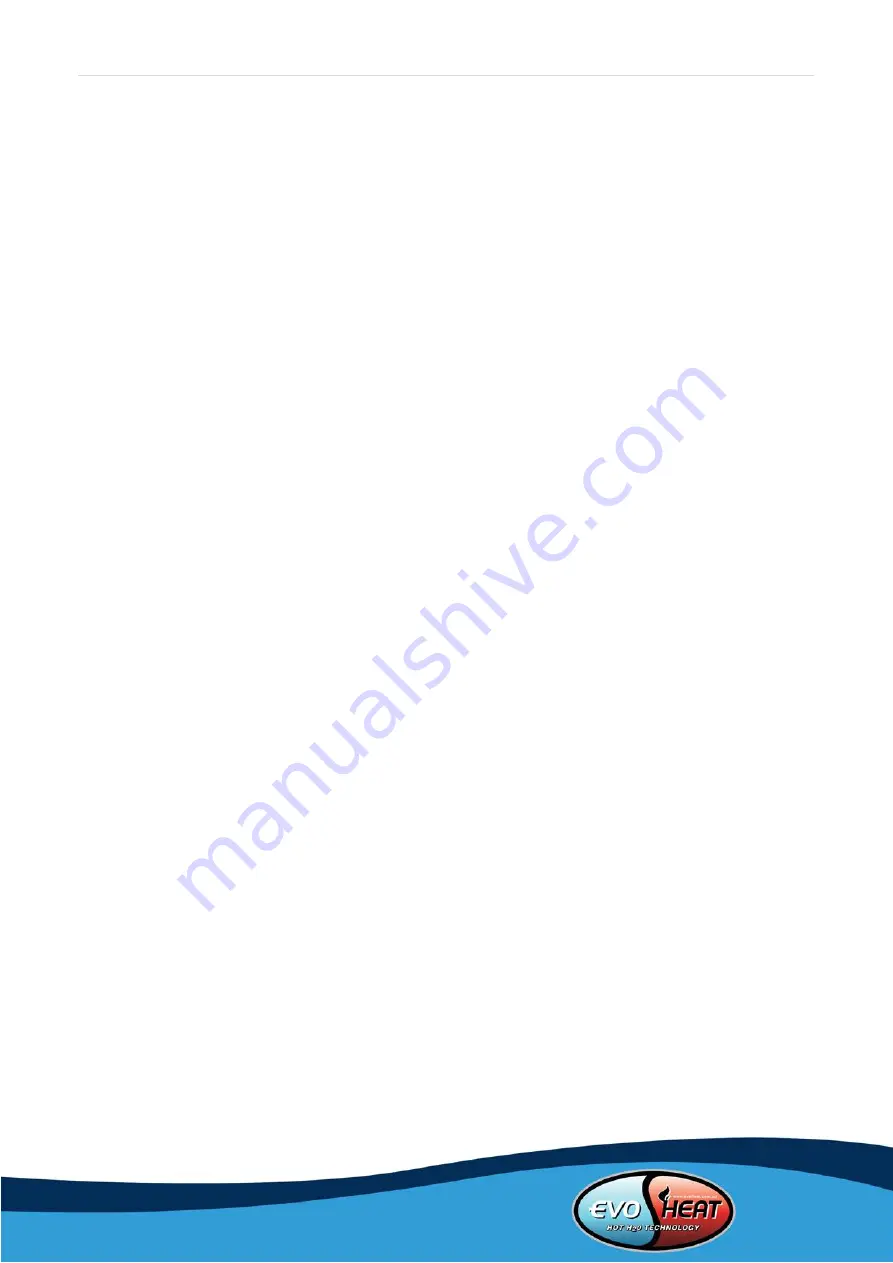
P
a g
e
| 33
7. Warranty
Please refer to the EvoHeat website for warranty details
•
Australia: www.evoheat.com.au
•
South East Asia: www.evoheat.com.sg
2.
Warranty terms are from date of purchase.
3.
This warranty excludes any defect or injury caused by or resulting from misuse, abuse, neglect,
accidental damage, improper voltage, vermin infestation, incompetent installation, any fault not
attributable to faulty manufacture or parts, any modifications which affect the reliability or performance
of the unit.
4.
This warranty does not cover the following:
a.
Natural Disasters (hail, lightening, flood, fire etc.)
b.
Rust or damage to paintwork caused by a corrosive atmosphere
c.
When serviced by an unauthorized person without the permission of Evo Industries
d.
When a unit is installed by an unqualified person
e.
Where a unit is incorrectly installed
f.
When failure occurs due to improper or faulty installation
g.
Failure due to improper maintenance (refer Operating Instructions)
h.
‘No Fault Found’ service calls where the perceived problem is explained within the
i.
Costs associated with delivery, handling, freighting, or damage to the product in transit.
5.
If warranty service is required you should:
a.
contact Evo Industries Australia on 1300 859 933 or via our Contact page on our web site
b.
provide a copy of your receipt as proof of purchase
c.
have completed the online warranty registration or provide a completed warranty card.
6.
Onsite technical service is available within the normal operating area of your Evo Industries
authorized Service Centre. Service outside this area will incur a traveling fee.
7.
Unless otherwise specified to the purchaser, the benefits conferred by this express warranty and
additional to all other conditions, warranties, rights and remedies expressed or implied by the Trade
Practices Act 1974 and similar consumer protection provisions contained in legislation of the States and
Territories and all other obligations and liabilities on the part of the manufacturer or supplier and
nothing contained herein shall restrict or modify such rights, remedies, obligations or liabilities.
Summary of Contents for Force i12
Page 1: ...P a g e 1 ...
Page 6: ...P a g e 6 2 Unit Dimensions Force i9 Force i12 unit mm Force i17 unit mm 40 40 40 40 ...
Page 11: ...P a g e 11 4 Usage and Operation Instructions 4 1 Controller Introduction ...
Page 13: ...P a g e 13 4 2 3 Clock Setting 4 2 3 1 Time Setting ...
Page 14: ...P a g e 14 4 2 3 2 Timing Setting ...
Page 15: ...P a g e 15 4 2 4 Silent Silent Timing Setting 4 2 4 1 The Silent Button ...
Page 16: ...P a g e 16 4 2 4 2 Timing Silent Function Setting ...
Page 22: ...P a g e 22 4 4 Interface Drawing 1 Main Board Force i9 ...
Page 23: ...P a g e 23 2 Main board Force i12 Force i17 ...
Page 34: ...P a g e 34 ...