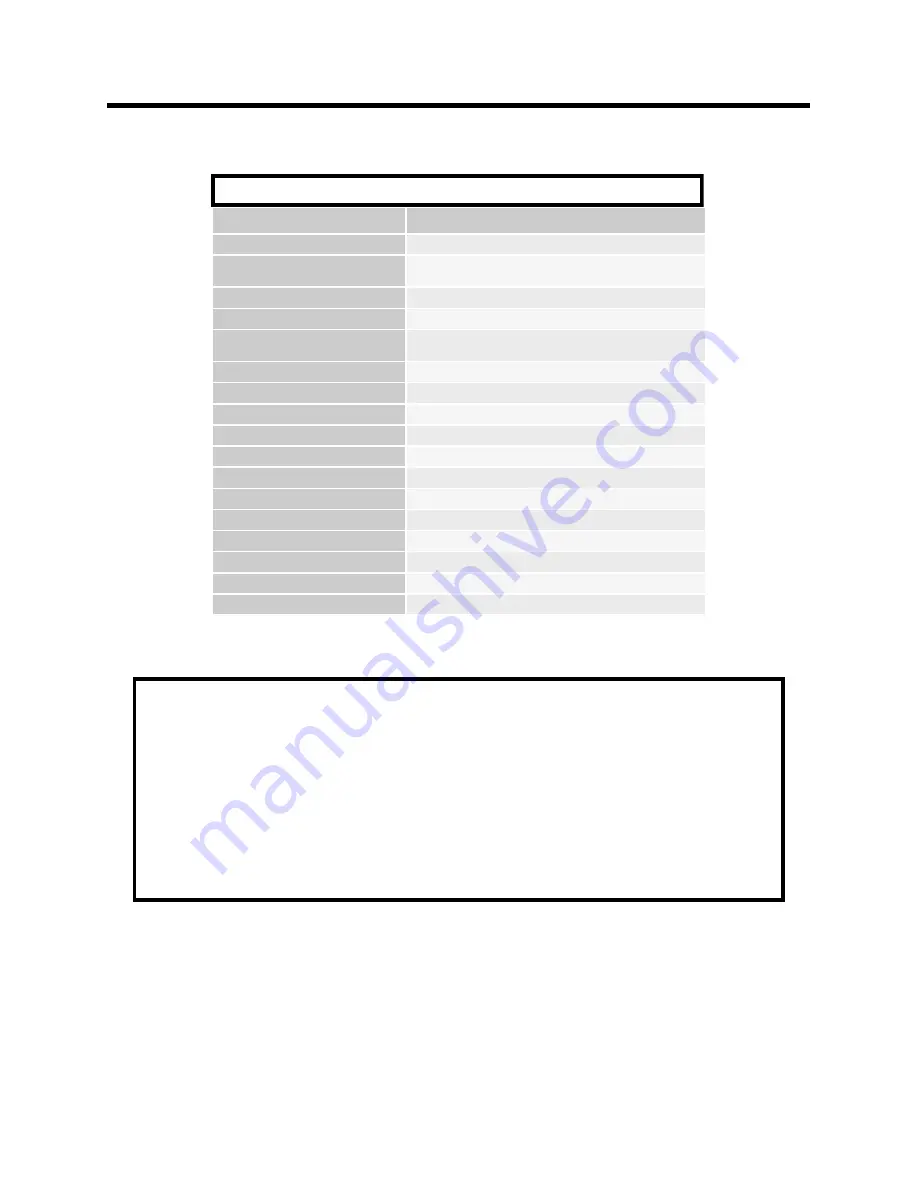
9
Specification:
PowerARC 300ST Stick/TIG welder
INVERTER TYPE
ANALOG CONTROLLED IGBT
INPUT VOLTAGE ±10%;PHASE/FREQUENCY
220V; 1 Phase and 3 Phase /50
-
60Hz
MAXIMUM INPUT AMPS (I₁max)
60A 220V 1 phase/ 45A 220V 3 phase
MAXIMUM INPUT RUNNING AMPS (I₁eff)
46.8A @ 220V 1 phase / 31A 220V 3 phase
DUTY CYCLE % @ AMPS
60% @ 300A/32V
100% @ 240A/ 29.2V
OUTPUT
20
-
300A, 20.8
-
32V
OPEN CIRCUIT VOLTAGE
70 V
TIG PACKAGE
OPTIONAL (Gas valve torch and regulator for scratch start DC use only)
CONSTANT CURRENT (CC) OUTPUT TYPE
DC (±)
CELLULOSE ROD CAPABLE 6010,6011
YES
INCLUDES
WELDER, WORK CLAMP WITH CABLE (10 FT),STICK TORCH WITH CABLE (10FT)
DINSE CONNECTOR TYPE
35/70mm² (DINSE 50 STYLE)
HOT START (SURGE CURRENT)
Adjustable
ARC FORCE CONTROL
Adjustable
MAXIMUM SUGGESTED ROD DIAMETER
1/4”
(6
-
7mm)
PROTECTION CLASS
IP21S
INSULATION GRADE
F
PERFORMANCE AND FEATURE COMPARISON
specifications
Section 1
IMPORTANT: The PowerARC 300 is DC output only and is not designed to weld aluminum or magnesium.
Need longer welding cables or an extension cord?
The welding cables are held into the DINSE style
connectors by set screws located under the connector cover and can be accessed by aggressively
twisting the rubber cover back and forth while pulling at the same time. A little effort may be required
the first time the connector cover is removed. If necessary, very lightly clamp the end of the connector
pin in a vise or with a pair of pliers while working the cover back until the cover pops off. The torch has
a small set screw that holds the cover in place. It acts as a wedge to hold the cover in place. It should be
loosened (not removed) and the cover slid back to access the set screw holding the cable in place.
When adding welding cable or using an extension cord make sure that the respective voltage/current
carrying capacity is sufficiently rated for carrying the maximum current of the welder over the dis-
tance of the cable.
Also, whether running long or short lengths, make sure the welder is strapped
down so any
“
whipping
”
movement of the cable will not overturn the welder or jerk it out of place.