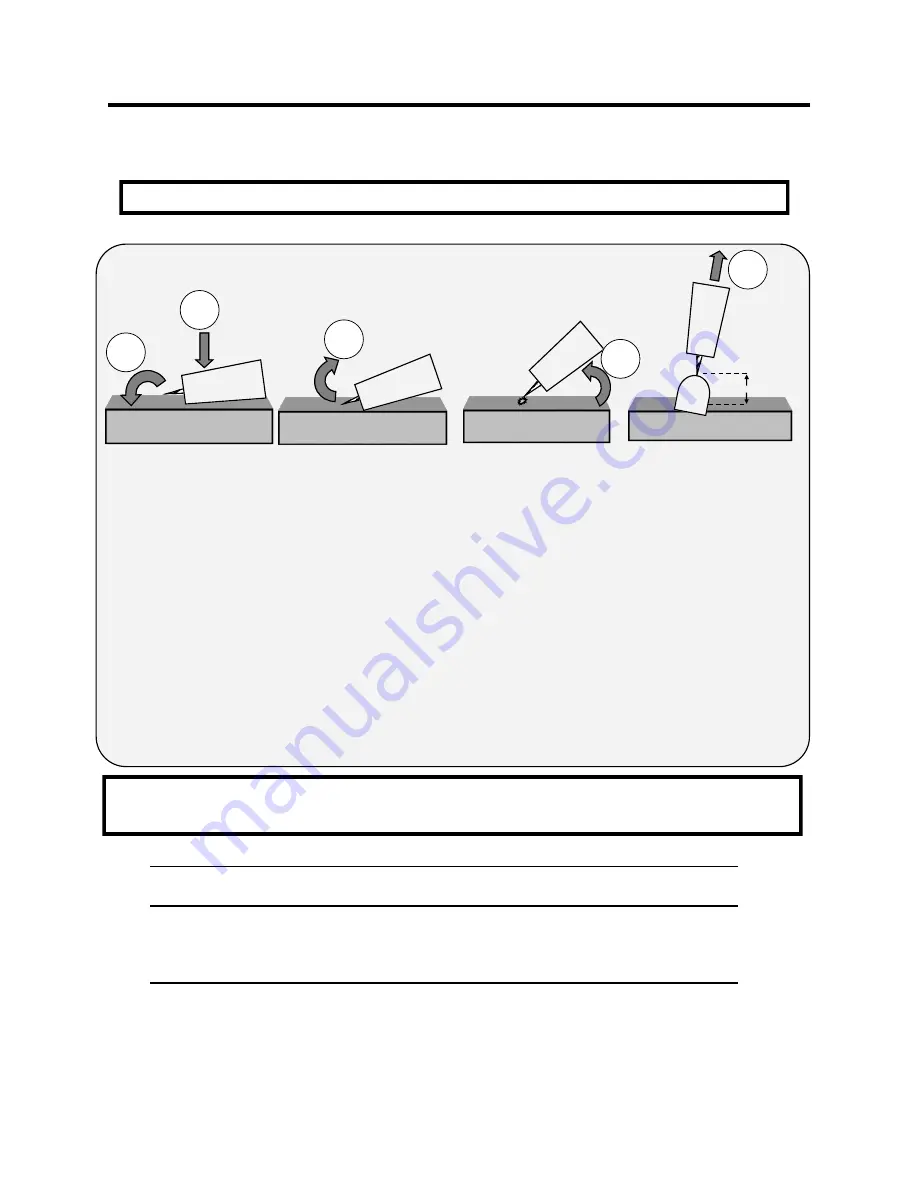
19
GENERAL SETUP AND OPERATION
Section 2
Note: This method takes some practice to master to initiate the arc on the first try. However, an arc can usually be struck fairly easily by the beginner, though
it may take 2 or 3 times to get one to initiate properly. After it is mastered, arc striking can be done with a light, seamless motion on the first try. Be sure to
protect the cup from damage when not in use. The Alumina TIG cups are fragile and can easily crack if dropped or tapped on the surface.
5. Leave
1/8”
or less gap between the tungsten tip and the metal.
1
. Position the edge of the ceramic cup on the metal. Do not touch the tungsten to the metal until ready. The tip is always live.
2. Quickly rotate the cup so that the tungsten comes in brief contact (< .2 seconds) with the metal.
3. After contact with the metal, quickly rock the torch back so that the tungsten breaks contact with the metal.
<1/8”
Note:
A Lift start should be done with a nearly seamless motion. Use a light touch and a quick motion for best results.
1
2
3
4
5
LIFT START TIG OPERATION
4. An arc should form. As the arc grows, raise the cup up off the metal and slowly rotate the torch into welding position.
6. Poor starts and welding of the tungsten to the surface can be a result of a rapid
“
double tap
”
or quick bounce off the surface
of the metal and back down. This inadvertently signals the inverter to put out full power until the continuity or arc is broken.
If this occurs, fully break the arc by releasing the switch or pedal. Re
-
sharpen the point if necessary, then allow the point to
stop glowing before attempting the start again. Do not scratch start in Lift TIG mode, or the tungsten may stick fast. Per-
forming a scratch start instead of a lift start can also trigger this as the tungsten
“
skips
”
along the surface.
METAL THICKNESS
(STEEL)
WELDING AMPS
(A)
TUNGSTEN DIA.
Ar FLOW RATE
1
-
3 mm/.040
”
-
3/32”
30
-
80
1.5
-
2 mm/
1/16”
-
3/32”
8
-
15 CFH /4
-
7 lpm
3
-
4 mm/
3/32”
-
1/8”
50
-
120
2
-
3 mm/
3/32”
-
1/8”
15
-
25 CFH/ 7
-
14 lpm
>4mm/
>1/8”
120
-
200+
1/8”
15
-
25 CFH/7
-
14 lpm
Note: These ranges are approximate, and not absolute. There is a range of overlapping capability with each tungsten size, metal
thickness and amp settings. Experience will eventually dictate the best range and choice of Tungsten size, filler size etc. As a
general rule, select a filler metal that is no more than
1/32”
larger or smaller than the Tungsten diameter. Do not use
“
pure
”
(green) Tungsten in an inverter. Use only Lanthanated, Thoriated, or Ceriated Tungsten.