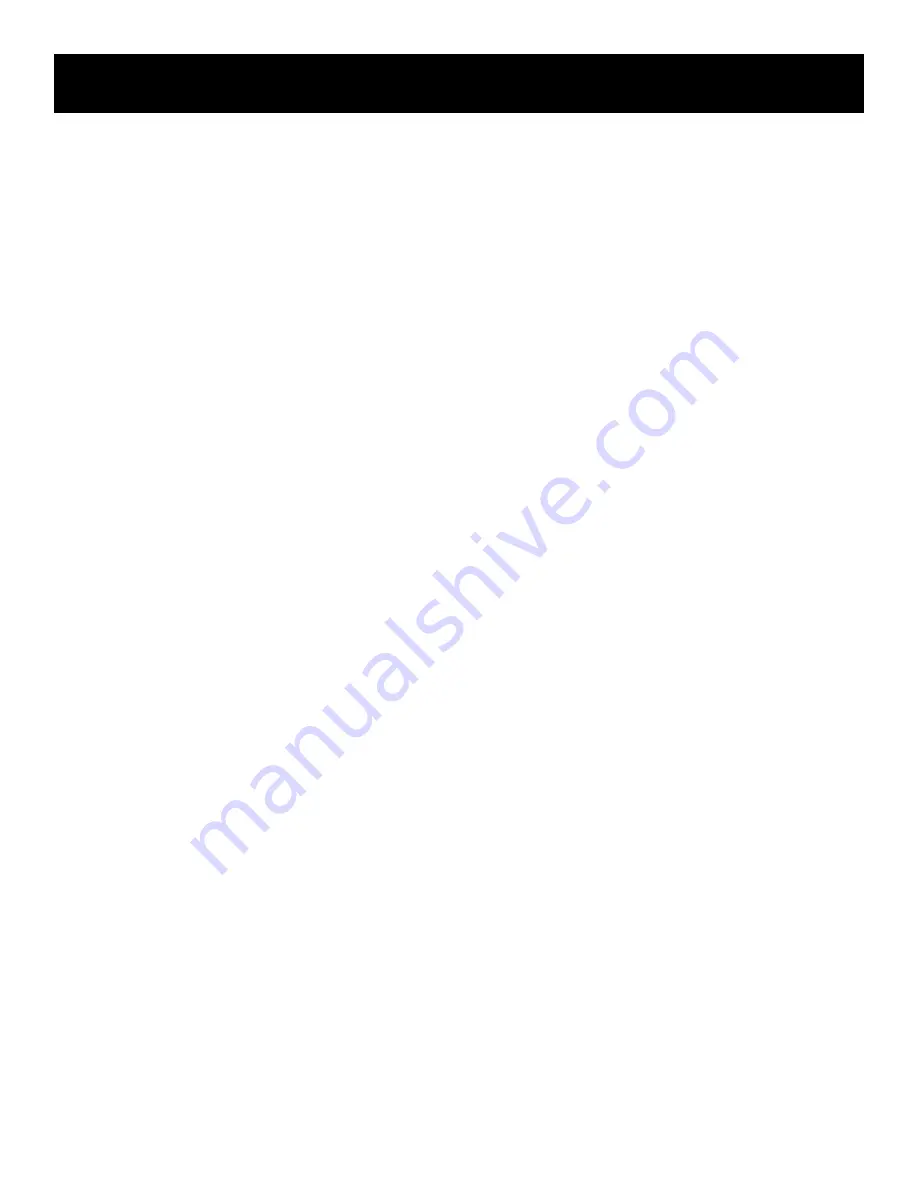
27
Component Identification and Explanation
Setting the Unit Up For Welding Manually
(IPM) and in Meters Per Minute) m/Min. This is the default
setting for the right side After 5 seconds of no input, When the
Wire Feed Speed is selected for adjustment the display will
brighten in color. This is the setting. After 5 seconds of no
input or adjustment of other parameters or functions, the select-
ed setting will default back to the Voltage setting.
7.
Up
-
Slope and Down Slope. These two functions are linked in
function. Up Slope provides a time duration for wire speed to
accelerate from the Start Wire Feed Speed (Start WFS). This
can be used to further improve arc starting when used with run
in and should exaggerate the hot start feel. The Down Slope
provides a time duration for the wire speed to ramp down to the
preset End Wire Feed Speed ( End WFS). This provides time for
the welder to fill the crater instead of the arc abruptly terminating
and leaving a crater at the end of the weld. In 2T, the arc will
start slow and accelerate up to the welding wire feed speed au-
tomatically. In 4T, the trigger should be depressed and released
quickly, as soon as the arc starts, to allow the Up Slope to func-
tion and accelerate the wire speed. If the trigger is held the Up
-
Slope will be delayed until the trigger is released. Note that
Down Slope will keep the wire feeding briefly after the trigger is
let go in 2T if a time value is set more than 0.0 seconds. In 4T
the trigger is depressed and held to control the actual arc termi-
nation, or is depressed and let go quickly to automatically allow
the wire to decelerate to the End WFS. If one or both of these
functions are not desired, select 0.0S. In PowerSet mode these
functions are managed automatically and will be non
-
adjustable.
If manually rapid tacking or spot welding select 0.0S for both.
8.
Start and End Wire Feed Speed (WFS). The Start and End Wire
Feed functions (Start WFS, End WFS) allow the user to set a pre
-
determined wire feed settings at the start and end of the weld.
At the Start of the weld, if being used, a lower setting creates a
smoother start with less popping and spattering typical of cold
starts. The reduction of the sputtering (also known as
“
machine
gunning
”)
will be noticeable at lower settings than used to weld.
End wire feed speed is designed to be used to fill the crater at a
lower Amperage/WFS to help prevent stress in the weld. If in
doubt about the best setting for either, always start at the mini-
mum Start and End WFS setting for the smoothest starts. Or, for
general purpose welding set both to 60% to 75% of welding
wire feed speed and fine tune it as desired.
9.
Pre
-
Flow. The unit has an adjustable pre
-
gas flow setting. This
automatically times the flow of gas before the weld, improving
overall weld quality at the critical start of the weld. However, the
user may opt to turn down this setting if desired Use the left Up
and Down navigation keys to navigate and highlight (turn green)
this setting. Use the left adjustment knob to turn the setting on
or off. In Flux
-
Cored mode, this feature will be unavailable and
be listed as N/A.
10.
Post Flow. The unit has an adjustable post
-
gas flow setting.
This is complimentary to the Preflow setting and also serves to
improve the weld quality and prevent oxidation after the weld is
terminated and also serves to provide gun cooling. However,
the user may opt to turn down this setting if desired Use the left
Up and Down navigation keys to navigate and highlight (turn
green) this setting. Use the left adjustment knob to turn the
setting on or off. In Flux
-
Cored mode, this feature will be una-
vailable and be listed as N/A.
11.
Inductance. This improves the wet in of the weld. A low setting
will result in a very poor arc, with a high pitch. The result will be
a raised ridge in the middle and poor wet
-
in. Excess spatter may
be observed. The result of too high of a setting will result in a
very fluid, flat puddle. The pitch will be raspy and not smooth.
Starts will not be as smooth Generally a setting of 65 to 75% is
a good starting point on Steel with C25. With Steel and C100,
70 to 80% is a good starting point. Generally pure CO2 is not
very smooth on many welders, but with inductance control, high
quality welds can be achieved. Stainless requires the highest
inductance with 90% or greater. Aluminum can range depend-
ing upon the wire from 60 to 80% or so. Flux
-
Core behaves a
little differently with a 40 to 50% starting point. Of course, dif-
ferent weld positions, joint designs and thicknesses of metal can
affect the inductance requirement slightly. Use the left Up and
Down arrow keys to navigate and highlight (turn green) the Burn
Back control. Use the left side control knob to change the value.
12.
Burn Back. This is the amount of time the arc stays on after the
wire stops feeding. It is used to help prevent the wire from stick-
ing in the weld and to reduce the need for constant trimming of
the wire before restarting. Use a setting of .1 to .3 seconds to
begin with for most applications. Smaller diameter wires need
less burn back time. Use the left Up and Down navigation keys
to select and highlight (turn green) the Burn Back feature. Use
the left adjustment knob to adjust the duration of the Burn Back.
13.
Spot Timer. This is a timer that can be set to automatically shut
off the weld when the trigger is held down. This allows you to
make repeatable and perfectly sized tack welds or short seams.
Use the Right side Up and Down navigation keys to navigate and
highlight (turn green) the Spot Timer. Use the right side adjust-
ment knob to turn the Spot Timer on and set the duration of the
spot timer. NOTE: Keep in mind that If the spot timer is turned
on accidently, the wire feed will stop suddenly soon after the
trigger is pressed. In fact it may barely feed and just seem to
quit if the time is set low. This is normal, but often a source of
tech support calls. If your wire feeder stops feeding unexpect-
edly after the trigger is pressed, check this function first.