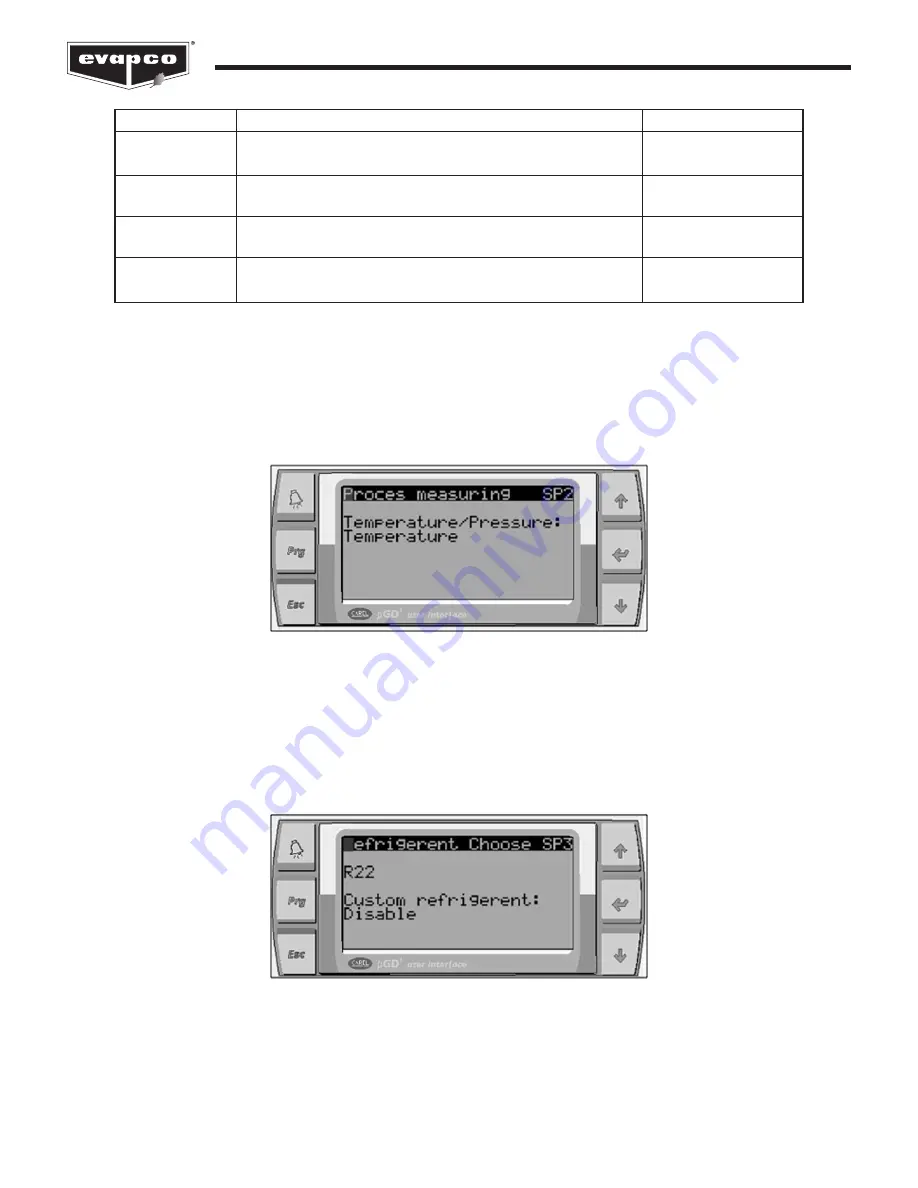
24
Controller User Manual
The probe type connected to universal input U1.
The process value of the lower reading used to establish a
scale. This is not required for all sensor types.
The process value of the upper reading used to establish a
scale. This is not required for all sensor types.
The amount of time that is allowed to elapse after the
connection to the sensor is lost before an alarm is generated.
NTC if Dry Cooler
4-20 mA if Condenser
Various
Various
60 seconds
Parameter
Description
Default
Table 8
The parameters associated with the process sensor.
Probe Type
Minimum Value
Maximum Value
Alarm Delay
Figure 42
The process measuring is set as temperature in this example.
The screen shown in Figure 42 allows the user to determine if the process sensor is measuring a temperature value or a
pressure value. Note that this setting will be set at the factory and should not require modification. For fluid coolers, the default
setting will be
Temperature
and for condensers the default setting will be
Pressure
.
Figure 43
The refrigerant is chosen as R22 in this example.
If the eco-Air unit is a condenser, and the process measuring is set as
Pressure
in Figure 42, the screen shown in Figure 43 will
be shown. When the EVAPCO Controller ships from the factory, the proper refrigerant for the application is already
programmed. Refer to Table 9 for a list of the available refrigerants. If the desired refrigerant is not listed in Table 9, a custom
refrigerant may be selected by selecting
Enable
.