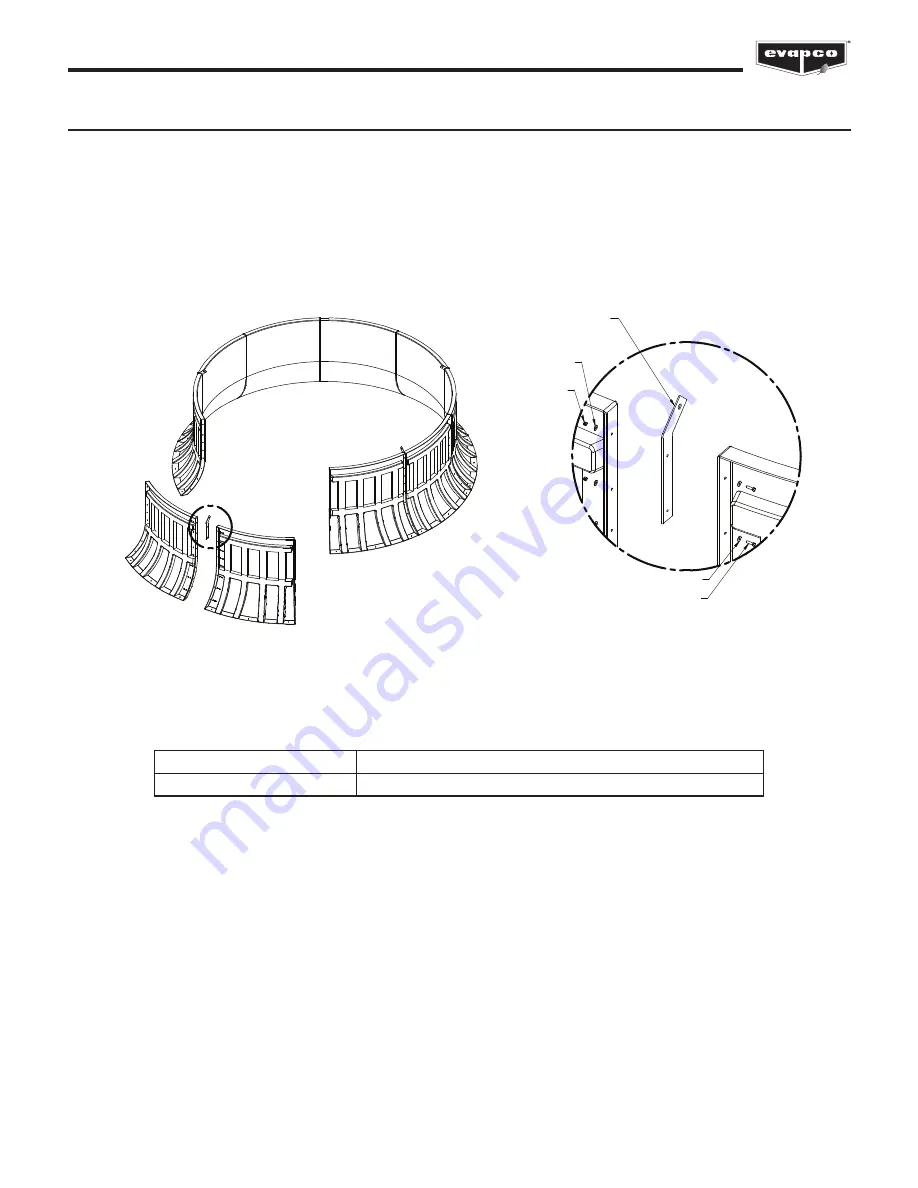
AT ATLAS Induced Draft Counterflow Cooling Towers
19
Figure 18 - Fan Cylinder Assembly
Fan Cylinder Assembly
The fan cylinder will ship in 10 sections for assembly and installation in the field. Each section will be joined with a flange as shown
in Figure 18. Fan cylinder assembly should be performed on the ground with one person holding the sections up until the assembly
is able to stand alone. See Table 9 below for hardware required to assemble the fan cylinder.
Lifting devices to be installed in between cylinder sections during assembly. Remove lifting device after installing fan cylinder if the
tower has a Super Low Sound Fan.
Flanges should be cleaned prior to assembly. Each cylinder should have 5 lifting devices total, installed in every other cylinder
panel seam.
ASSEMBLE CYLINDER PANELS USING
PROVIDED 3/8" HARDWARE
(SEE DETAIL A)
A
DETAIL A
(TYPICAL)
*ASSEMBLE CYLINDER PANELS
WITH LIFTING DEVICE SANDWICHED
BETWEEN EVERY OTHER PANEL
3/8" NYLOCK NUT
3/8" FENDER WASHER
3/8" FENDER WASHER
3/8" DIA X 1 3/4" BOLT
*REMOVE LIFTER AFTER INSTALLING CYLINDER
Units
Hardware Sizes
All ATLAS Units
3/8” (10mm) Nuts, Bolts & Washers
Table 9 - Hardware Sizes