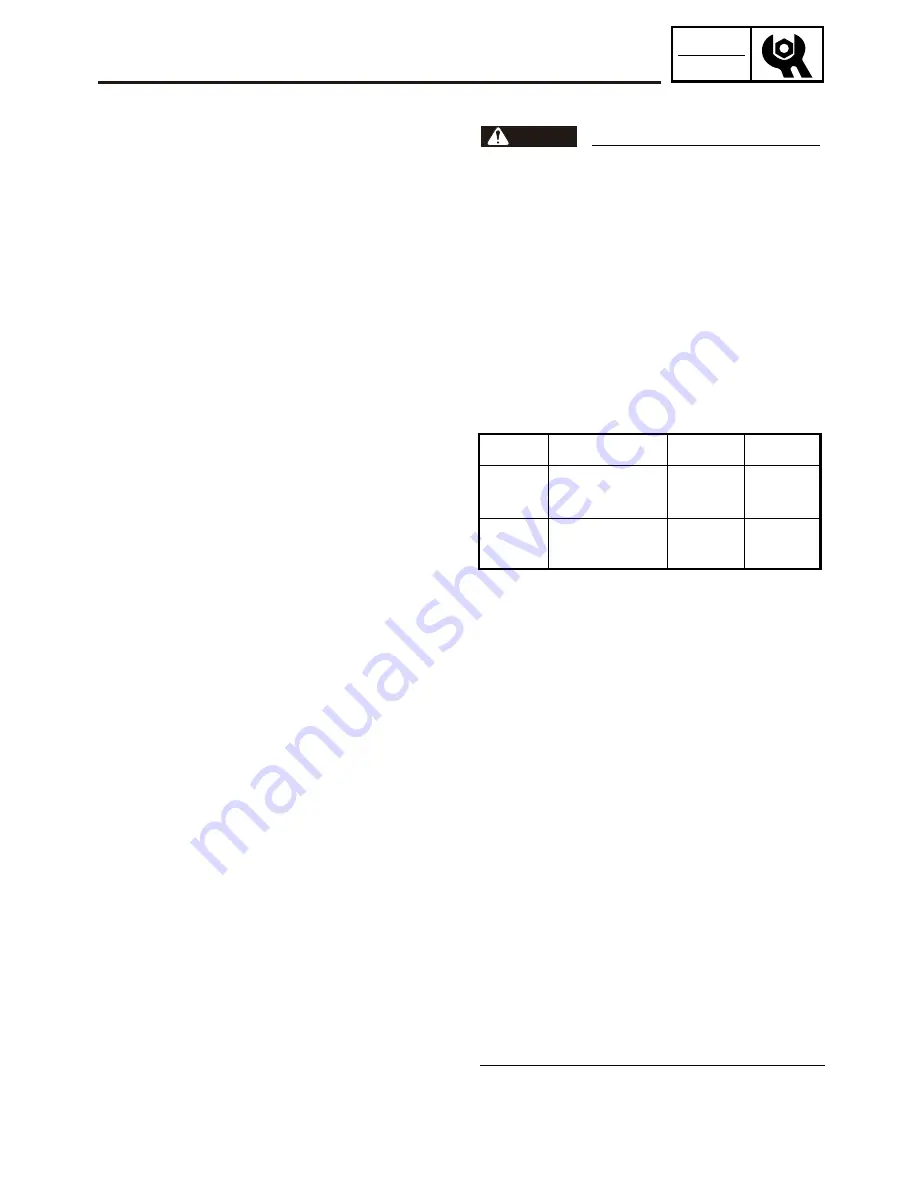
CHECKING THE TIRES
This model is equipped with low pressure
tires. It is important that they be inflated
correctly and maintained at the proper
pressures.
• TIRE CHARACTERISTICS
1) Tire characteristics influence the han-
dling of ATVs. The tires listed below
have been approved by E-TON POWER TECH
Co., Ltd. for this model. If other tire com-
binations are used, they can adversely
affect your machine’s handling charac-
teristics and are therefore not recom-
mended.
• TIRE PRESSURE
1) Recommended tire pressure
Front 25 kPa (0.25 kgf/cm
2
, 3.6 psi)
Rear 25 kPa (0.25 kgf/cm
2
, 3.6 psi)
2) Tire pressure below the minimum speci-
fication could cause the tire to dislodge
from the rim under severe riding condi-
tions.
The following are minimums:
Front 22 kPa (0.22 kgf/cm
2
, 3.2 psi)
Rear 22 kPa (0.22 kgf/cm
2
, 3.2 psi)
3) Use no more than
Front 250 kPa (2.5 kgf/cm
2
, 36 psi)
Rear 250 kPa (2.5 kgf/cm
2
, 36 psi)
when seating the tire beads. Higher
pressures may cause the tire to burst.
Inflate the tires slowly and carefully.
Fast inflation could cause the tire to
burst.
• MAXIMUM LOADING LIMIT
Vehicle load limits: 70.0 kg (154 lb)
*Total weight of the cargo, trailer hitch
vertical load, rider, and accessories.
Manufacturer
Size
Type
Front
MAXXIS
AT18
7-8
M939
Rear
MAXXIS
AT18
x
9-8
M940
x
3 - 33
CHECKING THE TIRES
CHK
ADJ
WARNING
www.Get2itParts.com
www.Get2itParts.com
www.Get2itParts.com