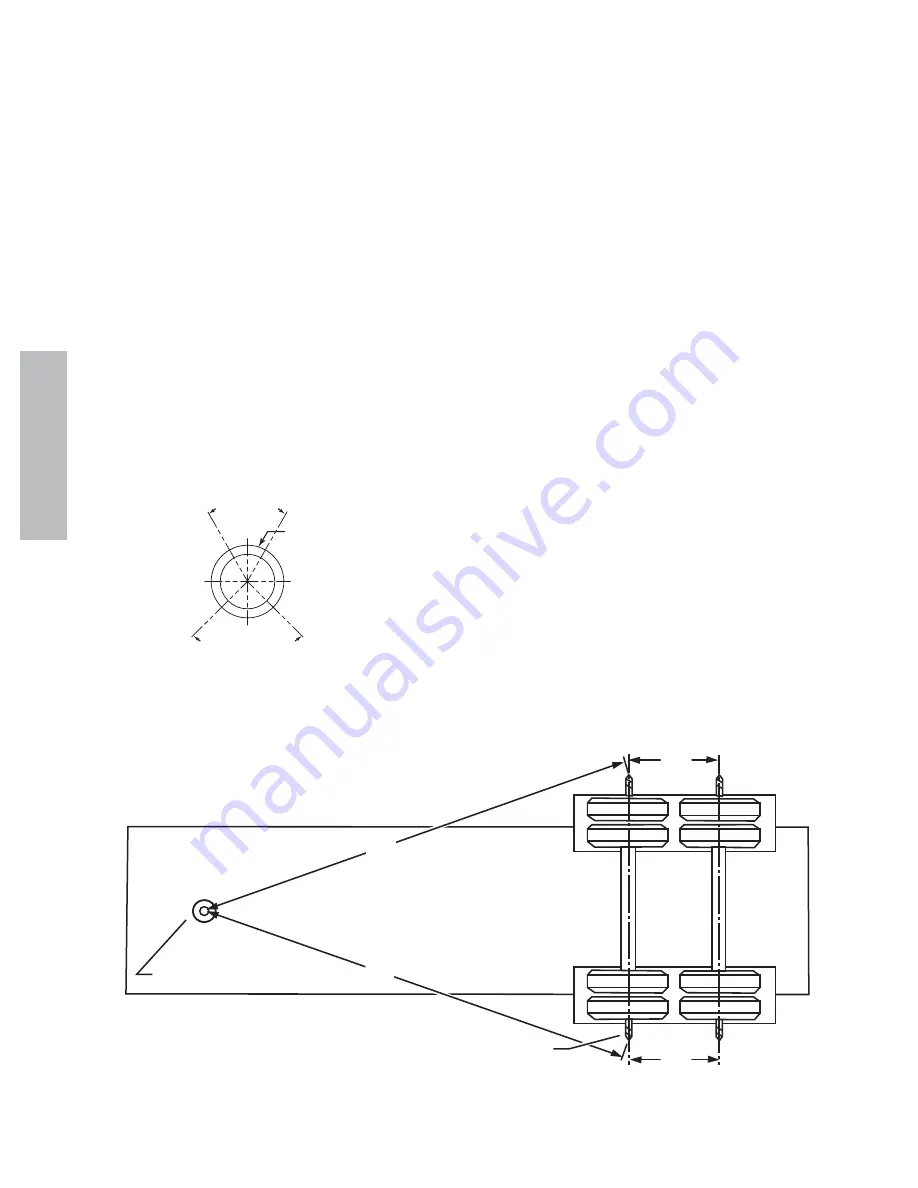
24
MAINTENANCE
3" NO WELD
ZONE
4" NO WELD
ZONE
TOP OF
AXLE
D) Multiple pass welding may be used on the beam/
axle connection using the following guidelines. Total
fillet weld size should be 1/2" (12.7mm).
Multiple pass (recommended method, SMAW,
GMAW, FCAW) weld initiation and termination should
be performed as outlined and shown in (Figure 17).
NOTE: All slag must be removed between passes.
Backstep fill all craters. Each pass must be accom-
plished in two segments. Recommended electrode is
E7018 if SMAW (stick) is used.
IMPORTANT: It may be necessary to C-clamp
axle to axle beam seat prior to welding. This will
insure that complete contact occurs between the axle
housing and beam seat.
Repair Welding
If the beam/axle weld is cracked or broken, the weld
Figure 18. No Weld Zones
can only be repaired if the crack or break does not
extend into the axle tube. To repair the weld, grid or
back gouge the weld/crack down to the base metal. If
the crack extends into the axle tube, or if any other area
of the axle is cracked, the axle must be replaced. Apply
the repair weld according to the information in Sec-
tions 1-3 of the guideline.
Welding Precautions
A) All welds must be kept away from the top and
bottom of the axle where maximum stresses occur. The
"no weld" zones are illustrated in (Figure 18).
B) Do not test weld the arc on any part of the
axle tube. This can cause a material change which can
lead to a small crack that may eventually grow and af-
fect the fatigue lift of the axle.
Figure 19. Alignment of Axle
1 6450076 BAZOOKA
2 6450077 AXLE EXTENSION SET
AXLE EXTENSION SET SHOWN IN PLACE
SR
SL
LL
LR
SL = SR =
±
1/16
LL = LR =
±
1/16