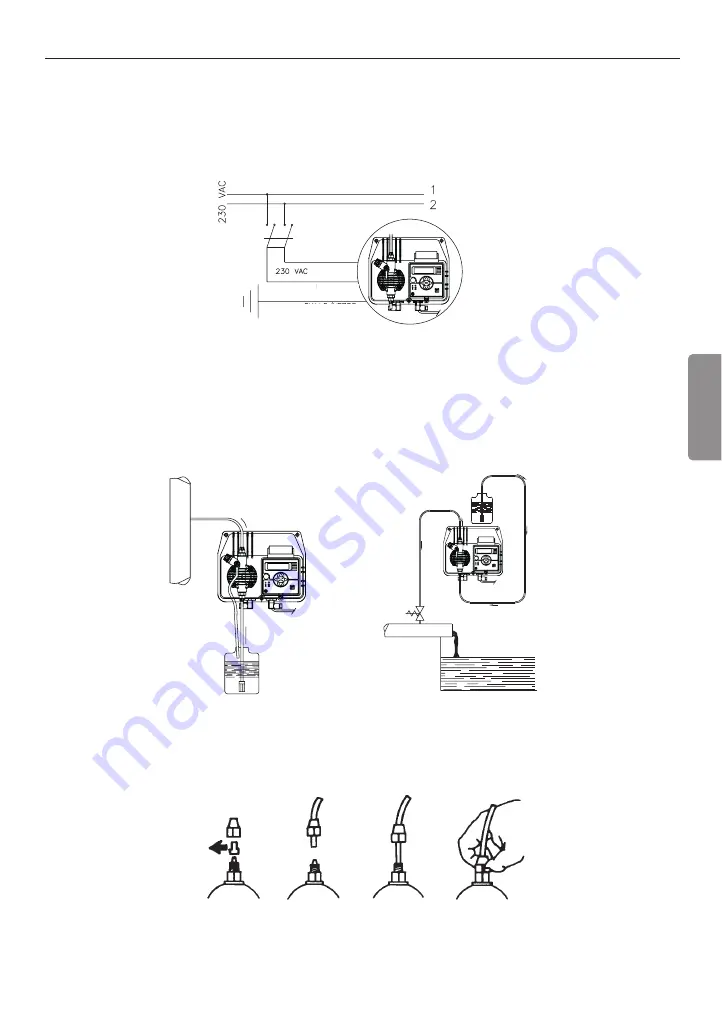
3.0 - INSTALLATION
a. - Install the pump in a dry place and well away from sources of heat and, in any case, at environmental tem-
peratures not exceeding 40°C. The minimum operating temperature depends on the liquid to be pumped,
bearing in mind that it must always remain in a liquid state.
b. - Carefully observe the regulations in force in the various countries as regards electrical installations (Fig.4).
When the supply cable is devoid of a plug, the equipment should be connected to the supply mains by
means of a two-poles switch having a minimum distance of 3 mm between the contacts. Before access-
ing any of the electrical parts, make sure that all the supply circuits are open.
Fig. 4
c.- Locate the pump as shown in fig. 5 bearing in mind that it may be installed either below or above the level
of the liquid to be dosed, though the level difference should not exceed 2 meters. When the process plant in
which the pump is installed is operating at atmospheric pressure (no back pressure) and the chemical tank
is situated above the plant (Fig. 6), the condition of the injection valve should be checked at regular inter-
vals, because excessive wear and tear could cause additive to drip into the plant even when the pump is shut
down. If the problem persist, install a properly calibrate counter-pressure valve (C) between injection point
and the valve. In the case of liquids that generate aggressive vapours, do not install the pump above the
storage tank unless the latter is hermetically sealed.
Fig. 6
d. - The discharge nipple will always remain in the upper part of the pump. The suction nipple, which serves to
attach the hose (with filter) leading into the chemical tank, will therefore always be situated in the lower part
of the pump.
Fig. 7
e. - Remove the protection caps from the two nipples, slide the hoses over the connectors, pushing them right
home, and then fix them with appropriate tube nuts. (Fig. 7).
Fig. 5
C
•
23
•
ENGLISH
BLUE
BROWN
YELLOW/GREEN