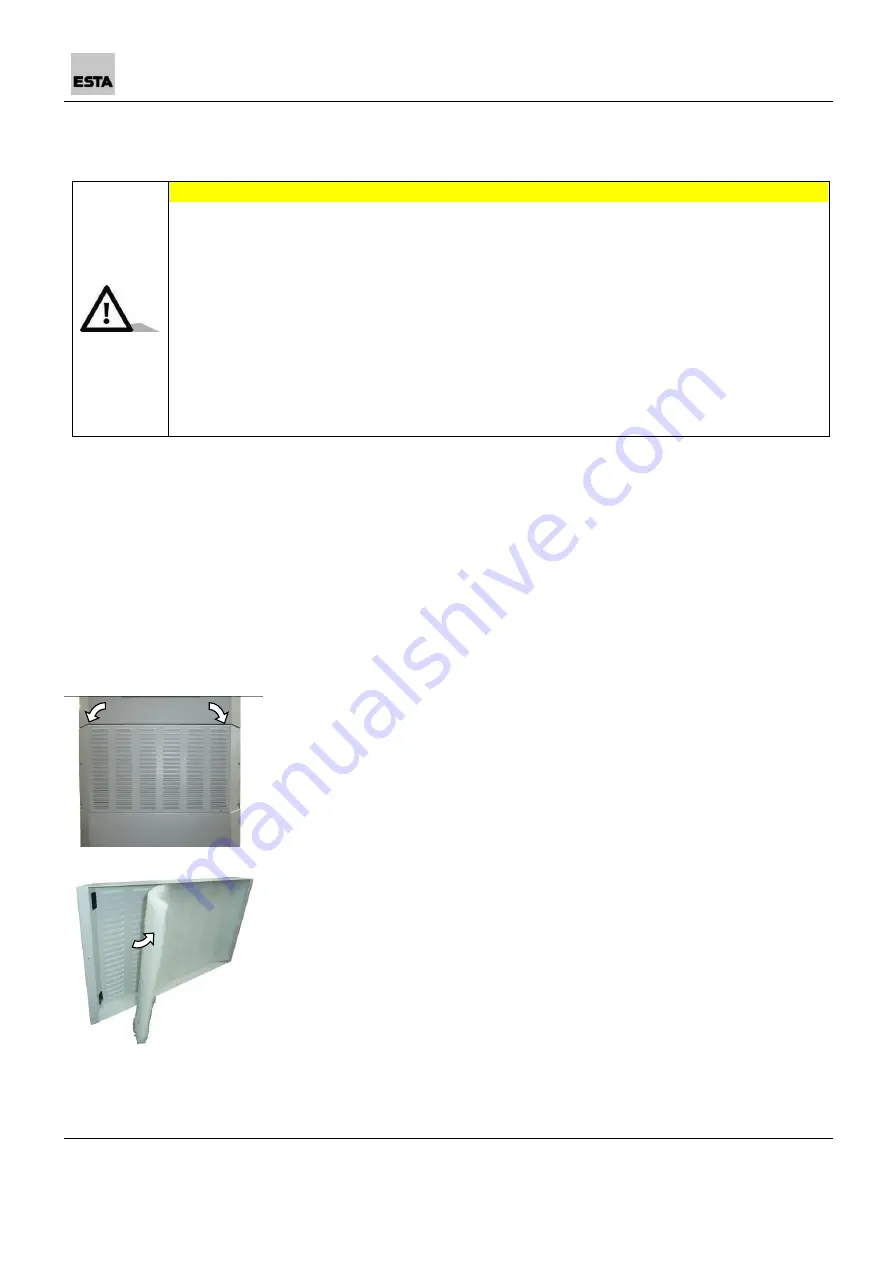
Maintenance &
troubleshooting
0973008-52-03
DDE 2000 // DDE 3000
27
7.3 Detach filter mat outlet element
CAUTION
Damage due to dust release
Maintenance, cleaning, repair and emptying work must be done only by
expert personnel.
Wear personal protective gear.
-
Respirator mask (particle filter class P3)
-
Protective clothing
-
Protective gloves
Set up locally filtered forced-air ventilation where the device is being
maintained, inspected or cleaned.
Regularly check whether the filter mats have clogged.
Operate the device only with the complete filtration system.
A filter mat is installed on the outlet openings in the product cover. This must be
checked regularly and replaced where necessary. Perform a visual inspection
when you take off the product cover off the product during cleaning, repair or
maintenance work. To do this:
1. Switch off the suction on the control panel and wait for the
post-cleaning.
2. Disconnect the compressed air supply.
3. Empty the compressed air tank
–
through manual cleaning, if
necessary
–
on the control panel.
4. Switch off the device on the main switch and pull the power
plug.
5. Take off the end caps via the fastening screws of the outlet
element.
6. Release and remove the fastening screws.
7. If available
→
Detach the potential equalisation from the
cover.
8. Take the outlet element cover off.
9. Remove the old filter mat without leaving residue.
10. Attach the new filter mat into the cover.
11. Place the cover onto the device with the outlet openings
pointing upwards.
12. If available
→
Attach potential equalisation to the cover.
13. Insert the fastening screws of the cover and tighten them.
14. Re-attach the compressed air supply.
15. Re-insert the power plug.
The device is now ready to operate again.