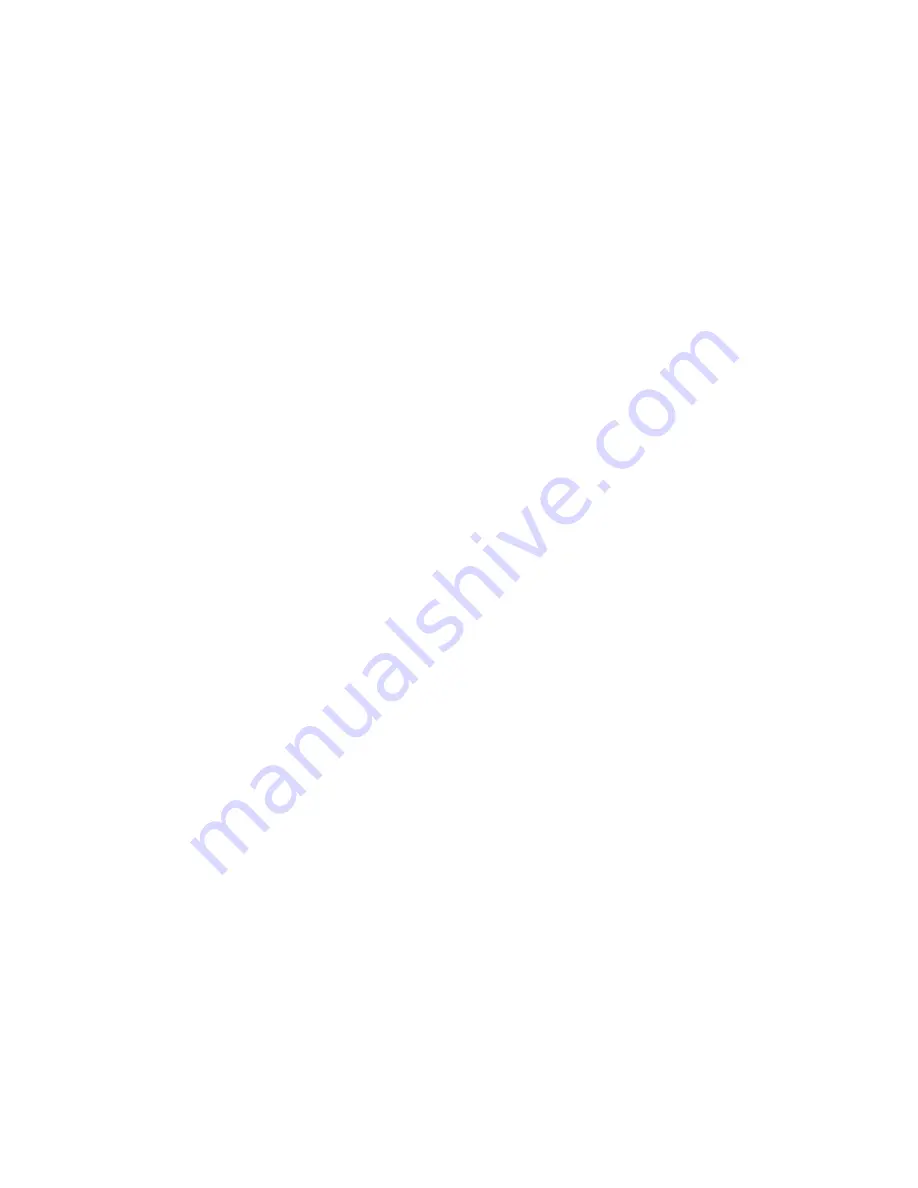
7
SL-7 Floor Edger
Repair/Maintenance
Instructions
1. Disc Pad Removal
2. Brush Replacement
3. Bearing Replacement
4. Adding Grease
5. Tap out Jackshaft for Bolt & Washer
6. Clean Armature Commutator
Before attempting any repairs on your Silver-Line SL-7 edger disconnect it from power.
The tools referred to in these instructions are available from Essex Silver-Line Corporation,
call us @ 800 451-5560 and ask for each tool separately or as a kit part # C7-92.
1)
Disc pad Removal:
The disc pad is threaded onto the jackshaft in a clockwise motion!
a) Remove dust tube exposing the vacuum fan on the armature. (4 screws)
(Fig. A)
b) Turn edger upside down, resting on the flat top of the SL-7.
c) Block the fan with the handle of a hammer or screwdriver to stop the armature from
moving.
d) Line up the bolts of the disc pad remover with the holes on the disc pad, and insert them
into the disc pad.
e) Using a hammer, tap the disc pad remover counte rclockwise to remove the old disc pad.
f) The disc pad should thread off the jackshaft.
Note: The jackshaft has interior and exterior threads. The interior accepts the bolt and washer
while the exterior threads are for the disc pad!
(Fig. B)
2) Carbon Brush Replacement:
a) Remove brush caps using flathead screwdriver. Be careful not to damage the slots on the
caps.
b) Remove the old brushes and blow out edger with compressed air. The brush holders should
be blown out periodically as a part of maintenance.
c) Install the new brushes and reinstall the brush caps.
d) Run the unit to break in the new brushes.
3) Replacement of Bearings:
a) C7-40 (6201)
Top bearing
i) Remove cover (C7-4) and load spring (C7-12a) (4 screws). Be careful to see how the load
spring comes out of the machine so you can put it back in the proper position.
ii) Mark the top of the Bearing plate (C7-12) with a magic marker to show which side is top.
Remove the bearing plate with a set of pullers.
iii) Remove the bearing with pullers.
iv) Tap a new bearing onto the armature (6201).
v) Reinstall the bearing plate, load spring, cover and screws.
Summary of Contents for Silver-Line SL-7
Page 5: ...5...