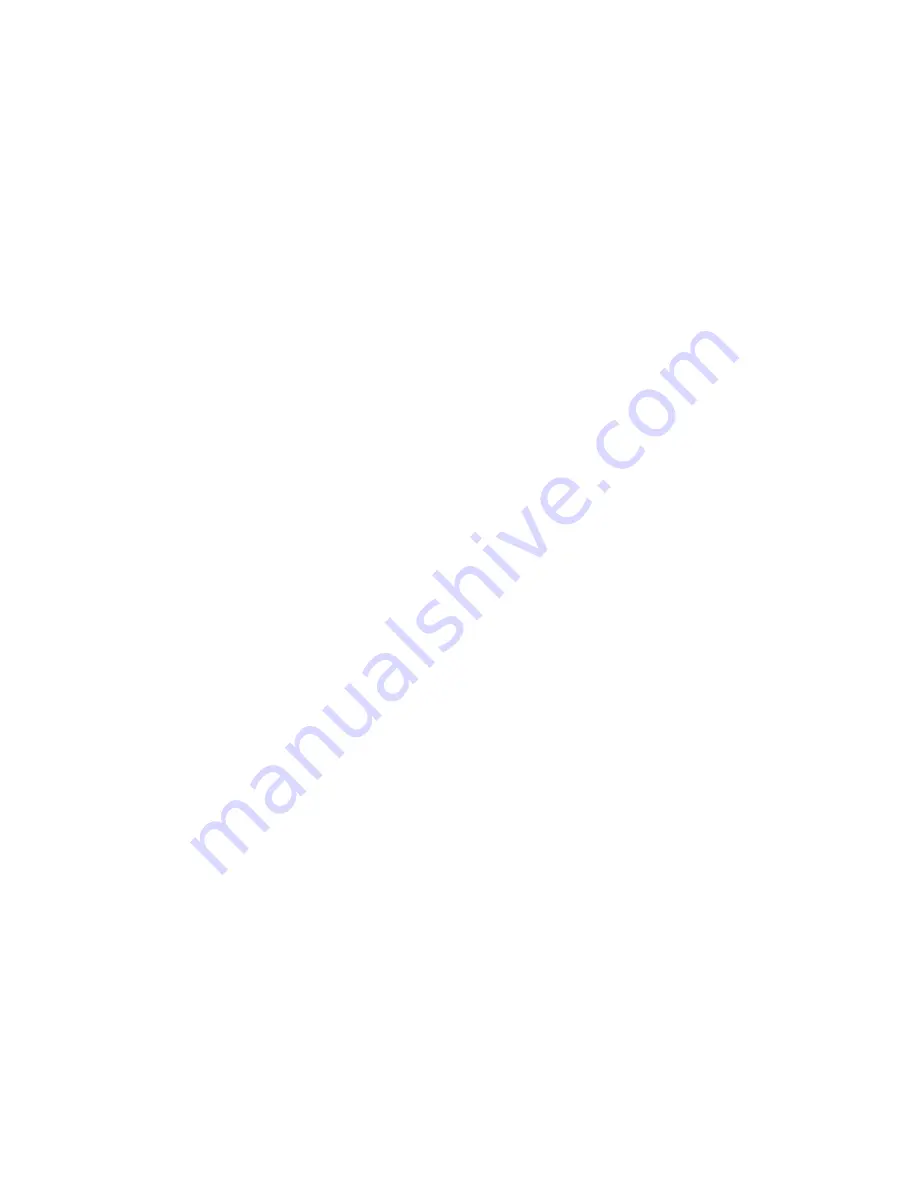
5
Unit Reassembly
1)
Start with base
(1)
. Turn base upside down and position on
press table. Base should be pointing upward with outer bear-
ing cup
(20)
exposed. Apply a layer of lithium bearing grease
to bearing cup surface.
2)
Invert output shaft
(4, retaining ring groove end down)
and
carefully lower into base
(1)
until the shaft’s outer bearing
cone
(18)
is seated against outer bearing cup
(20)
.
3)
Press shaft seal
(34)
into base until it is flush with bottom of
pilot diameter. Use a press fixture, if possible, to avoid distort-
ing seal. If press fixture is not available, a hammer and flat-
ended drift may be used by tapping outer edge of seal lightly
and alternating sides.
4)
Stand base assembly upright on output shaft.
CAUTION: The only thing holding output shaft and base
together at this point is the tightness in fit of the shaft seal.
Securely and cautiously turn unit upright, not allowing base
and shaft to separate.
5)
While holding output shaft
(4)
with one hand, rotate base
(1)
to be certain it turns freely and smoothly. The slight resistance
felt, if any, is due to shaft seal load (drag) on output shaft.
6)
Apply a layer of lithium bearing grease to inner bearing cup
(21)
surface.
7)
Install inner bearing cone
(19, small end down)
over internal
end of output shaft. Press bearing on slowly until it is just
seated against bearing cup
(21)
. With a slight press load still
applied, rotate base
(1)
by hand to ensure roller bearings are
rotating evenly and smoothly. Inner bearing cone
(18)
may
require additional press load to reach proper bearing preload.
If roller bearings are seated properly, continue on to set and
check bearing preload.
SHAFT BEARING PRELOAD: Proper shaft bearing preload is
achieved when torque required to rotate base is 50 to 80 in-
lbs. This rolling torque is equal to a force of approximately 11
to 18 lbs if pulling on base flange to rotate base (1). This may
be determined by feel or by using a fish scale or similar mea-
suring device to check rolling torque.
8) Install
shims
(10)
over internal end of output shaft
(4)
. Shims
should slide all the way down to outer bearing cone
(18)
,
where they will rest. The same number (quantity) of shims
removed from unit during disassembly should be returned.
Follow shims with bearing spacer
(23)
. Spacer will sit directly
on top of bearing shims.
NOTE: Quantity of shims (10) may vary from unit to unit.
Bearing preload, set at the factory, determines quantity of
shims.
9)
Install a new retaining ring
(22)
onto output shaft.
10) Lightly grease a new o-ring
(33)
and install it into o-ring
groove in base
(1)
. Assemble ring gear
(2)
to base
(1)
. Refer
back to scribe marks made across external joints of gear
drive prior to Disassembly Procedure. Line up scribe marks
between ring gear and base to give
correct hole alignment.
NOTE: Be certain that o-ring (33) stays seated in groove
during Step 10.
11) Install secondary carrier assembly into unit. Carrier assembly
should be installed with hub side down
(24 tooth spline)
.
Rotate carrier assembly back and forth to mesh secondary
planet gear teeth
(7)
with ring gear
(2)
teeth. Once teeth
mesh, let secondary carrier slide down until it contacts with
output shaft spline. The carrier splined hub
(5)
should spline
onto output shaft
(4)
. Carrier hub will rest on top of retaining
ring
(22)
when splines are fully engaged. Check to be certain
carrier cup washer
(15)
is installed.
*12) Turn primary carrier assembly upside down so that splined
end of carrier
(6)
is up. Insert splined end of secondary sun
gear
(11)
into carrier spline until fully engaged. Install carrier
assembly into unit, sun gear down. Sun gear teeth will mesh
with secondary planet gears, and primary planet gear teeth
(8)
will mesh with ring gear
(2)
.
13) Put input thrust washer
(26)
over step of input gear
(12)
.
Insert input gear into unit so that teeth mesh with planet
gears.
14) Grease a new o-ring
(33)
and install it into bottom of cover/
bail assembly
(3)
. Refer back to scribe marks made across
external joints prior to Disassembly Procedure. Line up scribe
marks between cover/bail assembly and ring gear
(2)
so that
orientation of motor mount holes and oil plug are back to their
original positions.
NOTE: Be certain o-ring (33) stays seated in cover/bail
assembly during Step 15.
15) Install all twelve of the 7/16 lockwashers
(31)
and the 7/16
hex capscrews
(27)
and torque to 70 ft-lbs.
16) Fill unit with 2.5 pints of a GL-5 grade EP 80/90 gear oil.
Proper oil level will measure to middle of primary planet gears
(8)
.
17) Lift bail assembly
(42)
onto planetary unit. Align access hole
with motor ports. Secure with six hex head capscrews
(38)
,
lockwashers
(36)
and nuts
(37)
; torque to 55 ft-lbs.
18) Install
motor
(41)
with gasket
(35)
, using hex head cap
screws
(39)
and lockwashers
(36)
; torque bolts to 55 ft-lbs.
THE AUGER DRIVE IS NOW READY FOR USE.