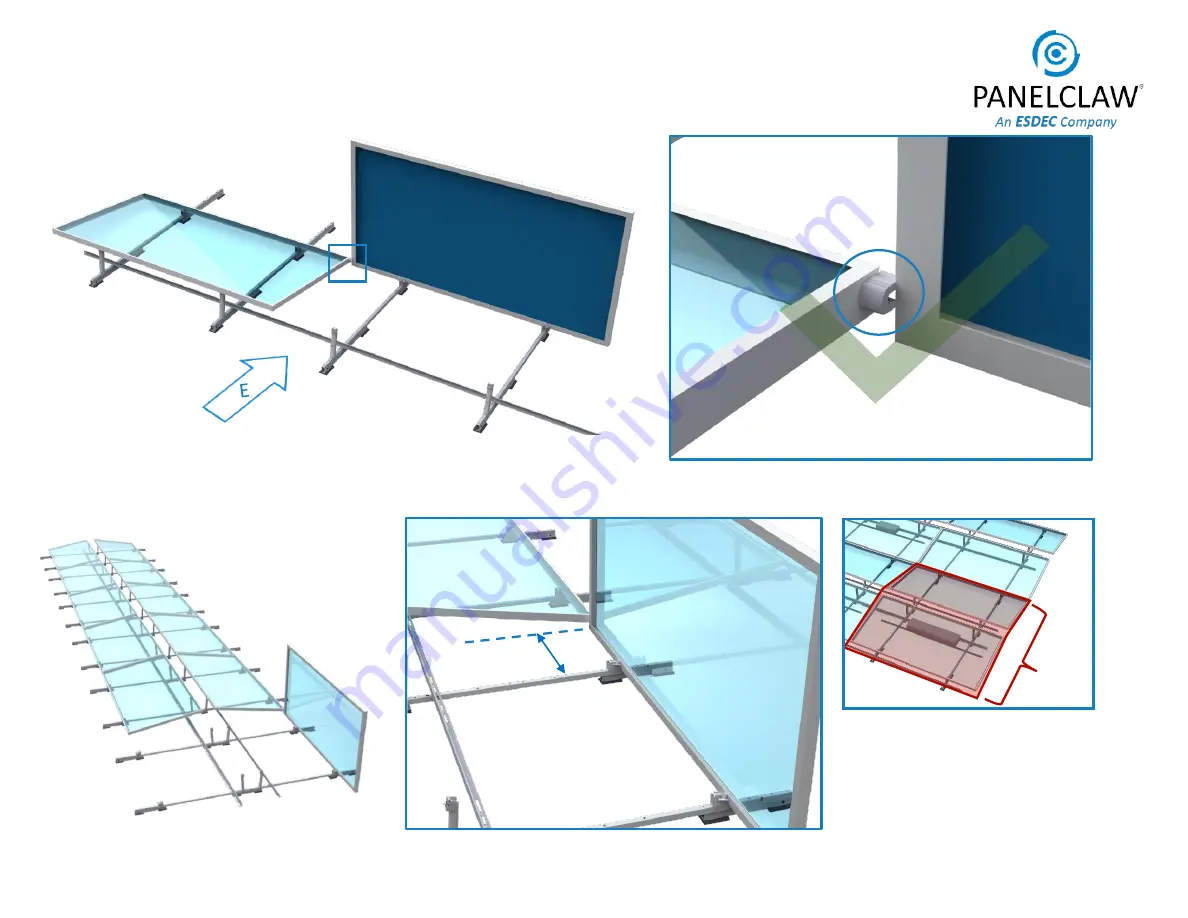
9910046 RevG April 2021
PAGE
16
7. Continue Installing Modules
ALERT:
When forecasted wind gusts
exceed 25% of the wind speed listed
in the Site Criteria Table of the
Racking
Construction
Set,
all
mounted modules must be complete
pairs (Domes) to avoid system
damage.
DOME
Use Cam Claw as spacer to set spacing between modules.
ALERT:
Check the R
dimension every 5
th
module and adjust
spacing between
modules as needed.
R
Tip:
R dimension is found in the Racking Construction Set.
See Sheet Title: Typical Array Dimensions.
ALERT:
If Cam Flanges are located on
Module mounting holes refer to
page 14 of the manual to verify
appropriate spacing.