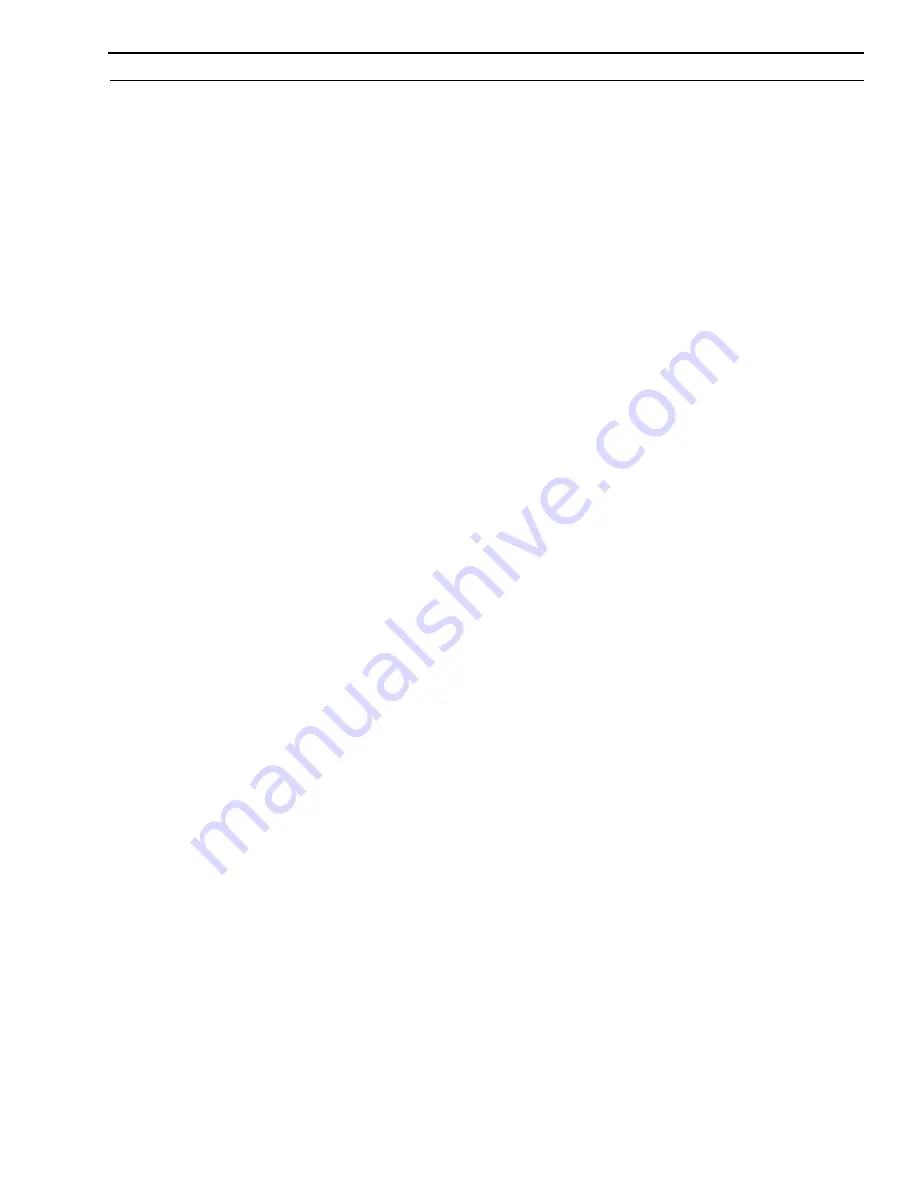
3
MAINTENANCE
WARNING
MAINTENANCE INVOLVING THE REMOVAL OF THE OUTER COVER MUST ONLY BE UNDERTAKEN BY QUALI-
FIED OR SUITABLY TRAINED PERSONNEL.
Switch off and disconnect the unit from the main supply before under-taking any maintenance tasks.
Daily (Operator task)
I.
Check all welding and electrical cables for signs of cracking or general deterioration.
2. Check that all electrical (and gas) connections are in good physical condition.
3. Check the torch or electrode holder for damage. Replace any suspect part(s).
ALWAYS CHECK THE WELDING AREA DAILY FOR POSSIBLE SAFETY HAZARDS. IF IN DOUBT CONSULT YOUR SAFETY
OFFICER.
Monthly (Maintenance Department Task)
l. Switch off the unit and disconnect from the main electrical supply.
2. Remove the cover (retain the fixing screws)
3. Using a soft brush, remove any dust or dirt from the interior of the unit. If compressed air is used to the unit the pres-
sure must not exceed 30 psig, and the air must be dry.
SUITABLE EYE AND MOUTH PROTECTION SHOULD BE WORN.
. Replace the cover.
. Reconnect the unit to the main supply.
SECTION 4
MAINTENANCE
Summary of Contents for Miniarc 150
Page 1: ...Miniarc 150 F15 725 02 2006 Instruction Manual...
Page 4: ...TABLE OF CONTENTS...
Page 12: ...12 SECTION 1 DESCRIPTION...
Page 34: ...34 SECTION 3 OPERATION...
Page 36: ...36 SECTION 4 MAINTENANCE...
Page 38: ...38...
Page 44: ...Notes...
Page 45: ...Notes...
Page 46: ...Notes...