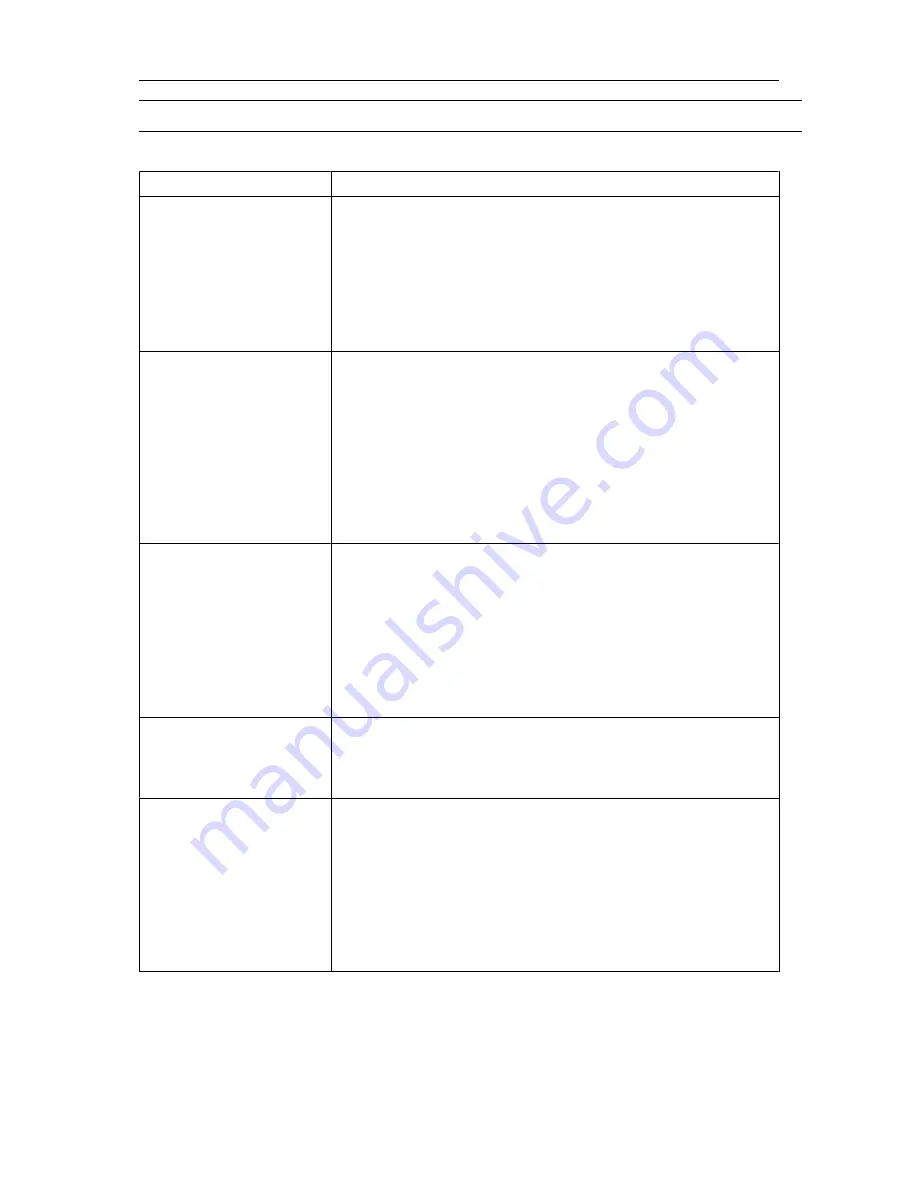
8 TROUBLESHOOTING
0463 408 001
- 32 -
© ESAB AB 2017
8
TROUBLESHOOTING
Try these checks and inspections before sending for an authorized service technician.
Type of fault
Corrective action
Porosity within the weld
metal
• Check gas bottle is not empty.
• Check gas regulator is not closed.
• Check gas inlet hose for leaks or blockage.
• Check that the correct gas is connected and the correct
gas flow is used.
• Keep the distance between the MIG torch nozzle and the
work piece to a minimum.
• Make sure the work piece is clean before welding.
Wire feeding problems
See appendix WEAR
PARTS for correct sizes
and types.
• Make sure the wire spool brake is adjusted correctly.
• Make sure the feed roller is correct size and not worn.
• Make sure the correct pressure on the feed rollers is set.
• Make sure proper direction of motion based on wire type
(into the weld pool for aluminium away from the weld pool
for steel).
• Make sure the correct contact tip is used and it is not worn.
• Make sure liner is the right size and type for wire.
• Make sure the liner is not bent so that friction is caused
between the liner and the wire.
MIG (GMAW/FCAW)
welding problems
• Make sure the MIG torch is connected to correct polarity.
Refer to the electrode wire manufacturer for the correct
polarity.
• Replace contact tip if it has arc marks in the bore causing
excessive drag on the wire.
• Make sure the correct shielding gas, gas flow, voltage,
welding current, travel speed and MIG torch angle is used.
• Make sure the work lead has proper contact with the work
piece.
MMA (SMAW) basic
welding problems
• Make sure you are using correct polarity. The electrode
holder is usually connected to the positive polarity and the
work lead to the negative polarity. If in doubt consult the
electrode data sheet.
TIG (GTAW) welding
problems
• Make sure the TIG torch lead is connected to negative
welding terminal
• Make sure the correct shielding gas, gas flow, voltage,
welding current, travel speed, filler rod placement,
electrode diameter and welding mode on power source is
used.
• Make sure the work clamp has proper contact with the
work piece.
• Make sure the gas valve on the TIG torch is on.