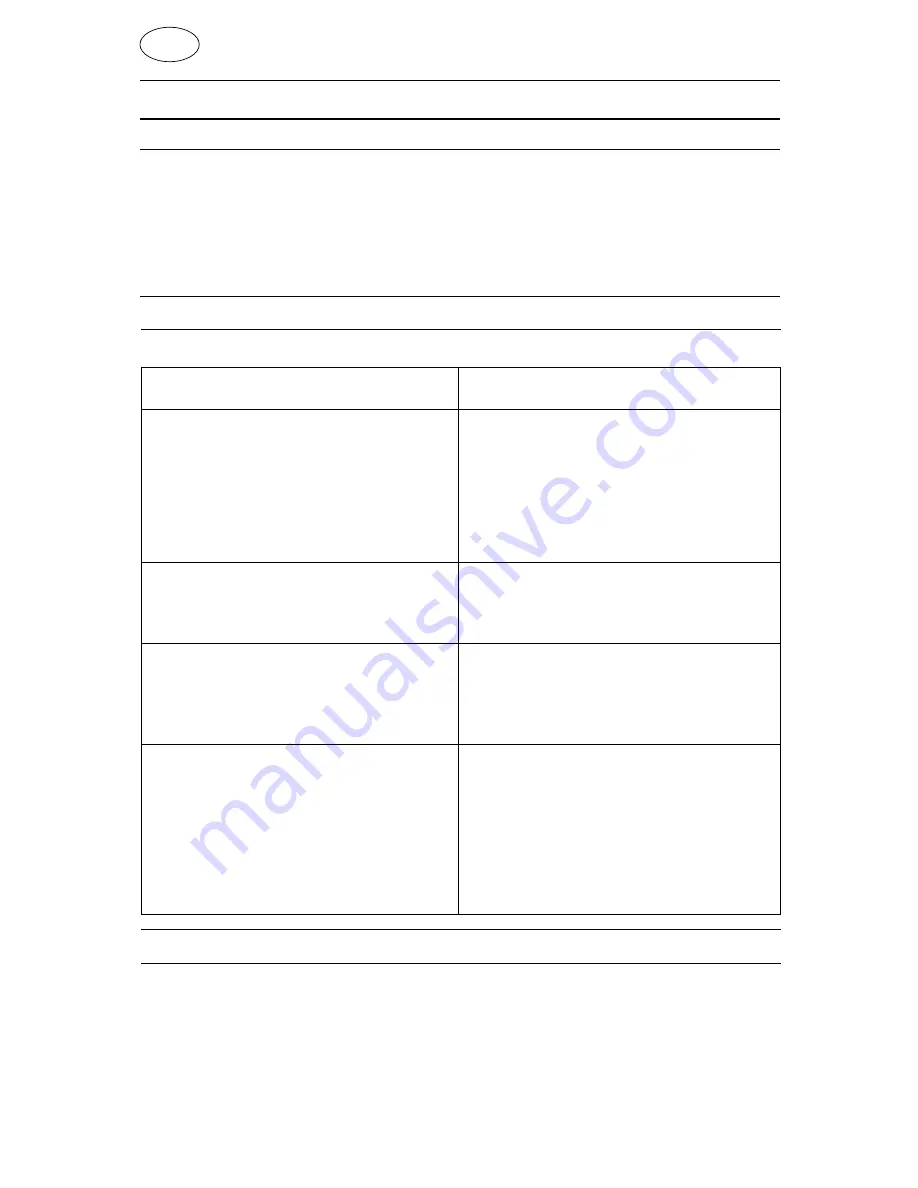
7
7..1
1
P
Po
os
ss
siib
blle
e
ffa
au
ulltts
s
a
an
nd
d
m
me
ea
as
su
urre
es
s
tto
o
tta
ak
ke
e
When ordering a spare part, please state the type and serial number of the machine as
well as number of the spare part, according to the spare parts list.
This will simplify dispatch and ensure you get the right part.
T
Ty
yp
pe
e
o
off
ffa
au
ulltt
No arc is generated by the welding
power source.
The welding current is interrupted in the
course of welding.
The thermal cut-out trips frequently.
Poor welding result.
M
Me
ea
as
su
urre
e
•
Make sure the mains switch is on.
•
Check that the welding and return
cables are properly connected.
•
Make sure the welding current set is
correct.
•
Verify that the welding process is cor-
rectly selected
•
Check if the thermal cut-out has trip-
ped (the yellow indicating led on the
front panel is on).
•
Check the mains fuse.
•
Check that the filter is not packed with
dust.
•
Check that the ratings of the welding
power source have not been exceeded
(overload of the power source).
•
Check that the welding and return
cables are properly connected.
•
Make sure the welding current set is
correct.
•
Check that there is nothing wrong with
the electrodes.
•
Verify that the welding process is cor-
rectly selected
8
ORDERING OF SPARE PARTS
7
FAULT TRACING
6
6..1
1
C
Clle
ea
an
niin
ng
g
Normally it is sufficient to blow the welding power source clean regularly using dry com-
pressed air (reduced pressure), and to clean the filter in the front regularly.
In dusty and dirty environment the welding power source should be cleaned at shorter
intervals.
GB
51
6
MAINTENANCE