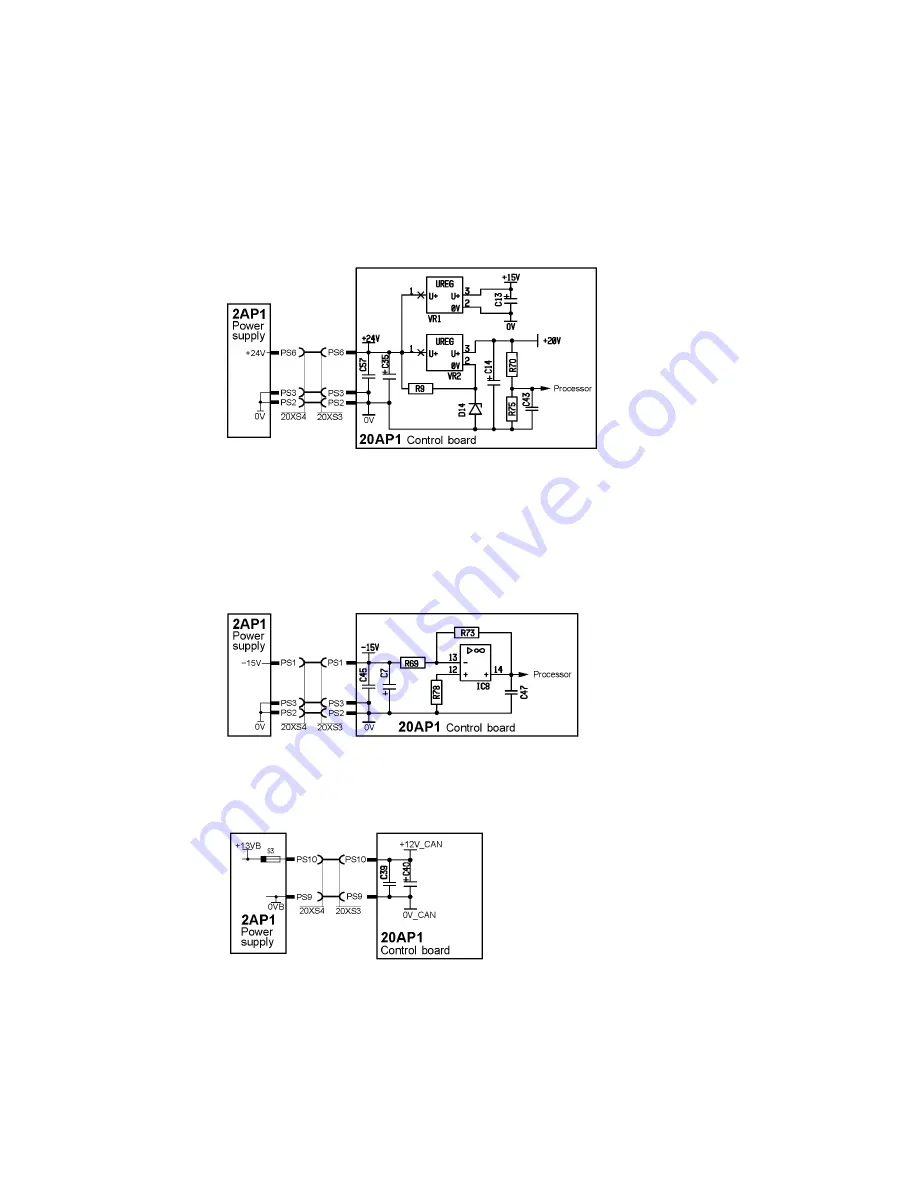
S0740 800 186/E080826/P50
-- 25 --
ct34_20
The voltage on terminal PS4 is normally about 24 V, when this drops below
20 V, pin 14 of IC6 goes low, providing the processor with a low power supply
voltage signal. The processor then stores current data and generates fault
code E4. When the 5 and 2.
5
V voltages are passing below their treshold
values, the processor receives a reset signal from IC16.
Fault code E4 is not displayed at normal power off
+15 V and +20 V
Voltage regulator VR2 produces an output voltage of +20
±
1.0 V, which
supplies the pulse width modulator output stage.
Voltage divider R70/R75 supplies 2.6 V to the processor. This provides a signal
that the power supply is available.
Voltage regulator VR1 produces an output voltage of +15 V, and this, together
with the --15 V supply, powers the analogue circuits.
--15 V
The --15 V power supply is monitored by the processor.
+12 V_CAN
The +13 VB from 2AP1 is used to supply the CAN circuits of the equipment.
This supply is referred to as + 12 V_CAN, its neutral point, 0 V_CAN, is
separated from the electronic neutral (0 V).
The tolerance of the voltage is 11.5 to 14.5 V.
Summary of Contents for Cadd Tig 1500i TA34
Page 8: ...S0740 800 186 E080826 P50 8 ct34_00 Tig 1500i with control panel TA34...
Page 9: ...S0740 800 186 E080826 P50 9 ct34_00...
Page 10: ...S0740 800 186 E080826 P50 10 ct34_00 Tig 2200i with control panels TA33 and TA34...
Page 11: ...S0740 800 186 E080826 P50 11 ct34_00...