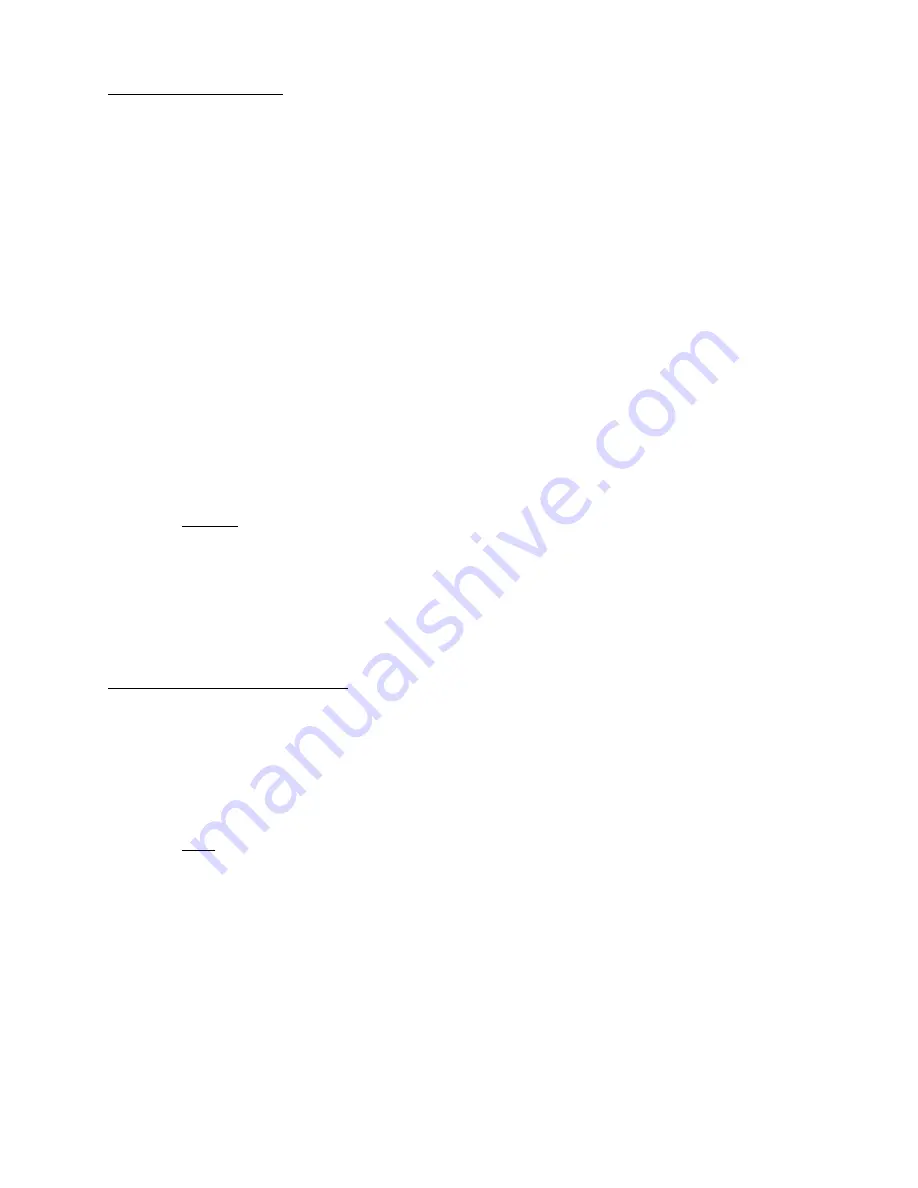
5
Torch Parameter Presets
Each torch can have the following parameters or variables preset:
Schedule number preset
Wire burnback preset
Shielding gas type
Spot weld time
The software will automatically switch to the torch being used when the torch trigger is depressed. Each torch
may have two welding schedules assigned at a time when using the Trigger Selection mode (described
above). The right side torch (viewed from the front of the feeder) is the default torch setting. This means that
when the feeder is first powered up this torch and its parameters will be displayed. If a red light between the
IPM and VOLTS display windows is illuminated, the left side torch parameters are being displayed.
Choose the schedule number (1- 8) for each torch by depressing the Schedule Selection key and setting the
desired schedule number in IPM window for the left torch and the VOLTS window for the right torch.
Preset the desired bumback by depressing the torch trigger switch to be preset. This action displays the
current welding parameters for that torch. Hold Burnback/Spot key in the up position and set a burnback
number in VOLTS window. Repeat this procedure for the other torch.
Attach the desired gas mixture to the appropriate torch for the type of welding to be completed.
Caution
- Some shielding gases will not pulse arc and short arc equally well. Therefore, the
optimization of both pulse arc and short/spray arc parameters will be dependent on the shielding
gas and its ability to support both processes.
If spot welding is desired, depress the torch trigger switch to be preset. This action displays the current
welding parameters for that torch. Hold the Burnback/Spot key in the up position and set a spot time in
seconds in the IPM window. Repeat this procedure for the other torch if desired. Entering a spot weld time
automatically disables the Trigger Selection mode and dual schedule operation is not possible.
Weld Schedule Parameter Presets
Pulse Arc Welding
Schedules 1 through 4 are dedicated pulse arc welding schedules for stainless steel using .045" (1.2 mm)
diameter wire. The synergic relationship is the same on each torch and for each schedule. When entering a
schedule number 1 to 4, the feeder control and power source is automatically set for pulse welding with .045"
stainless steel wire.
Note
- The SVI-450i power source slope switch should be set to the STEEP slope position. The
INUCTANCE & VOLTAGE knob on the SVI-450i is deactivated.
The !PM window will display the wire feed speed in inches per minute and the VOLTS window will show a
number between 0 and 200 with 100 being the default value. These numbers relate to the synergic relation-
ship programmed into the software and correspond to a pulse frequency. The number 100 is the nominal
pulse frequency required for the wire feed speed selected in the IPM window. This number will also affect the
arc length. If the welding arc length is too long the number can be decreased which shortens the arc length.
If the welding arc is too short, increase the number in the VOLTS window. Each count in the window changes
the pulse frequency by one pulse per second.
Summary of Contents for BOMBARDIER SVI-450i
Page 1: ...F 15 565 February 1999 ...
Page 8: ...F 15 565 2 99 ...