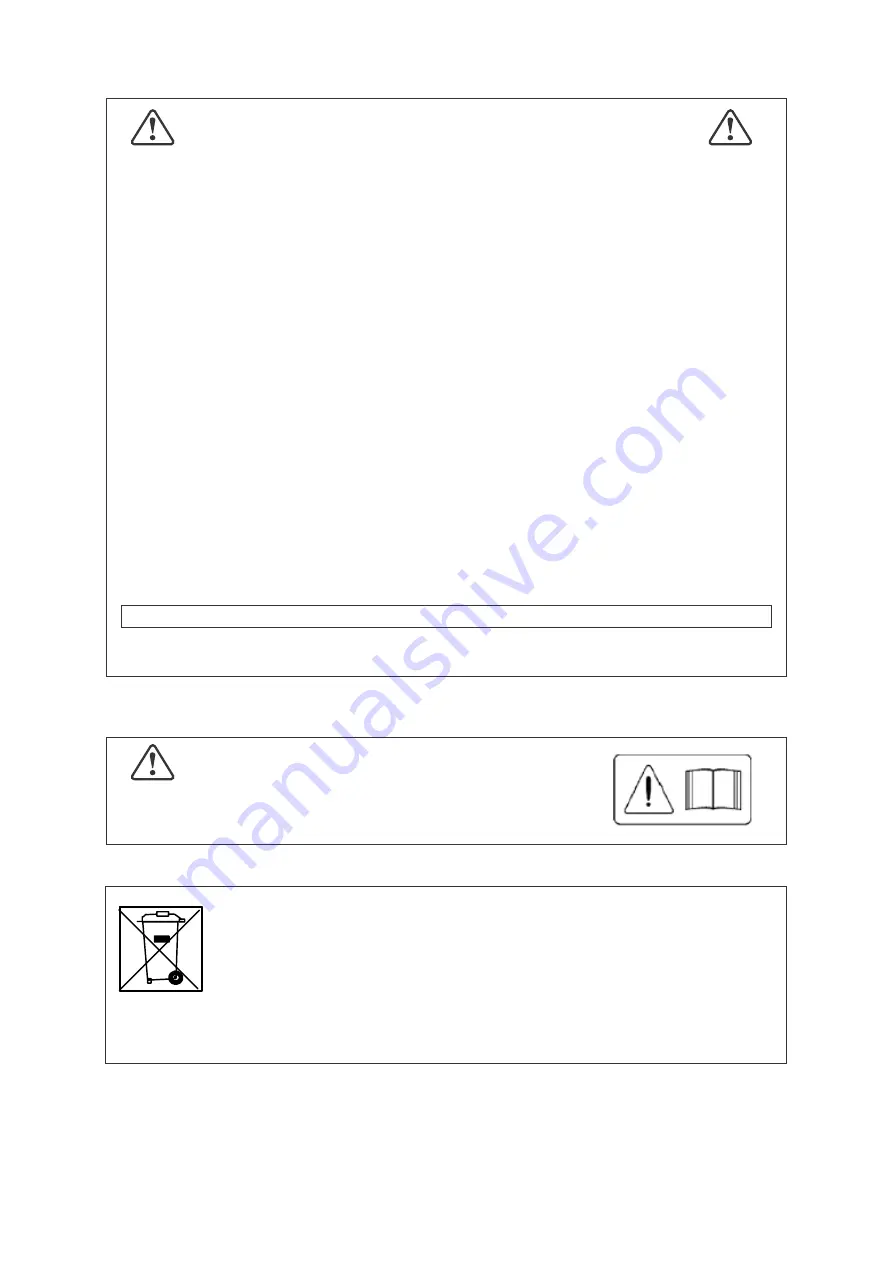
WARNING
ARC WELDING AND CUTTING CAN BE INJURIOUS TO YOURSELF AND OTHERS. TAKE
PRECAUTIONS WHEN WELDIN. ASK FOR YOUR EMPLOYER’S SAFETY PRACTICES WHICH
SHOULD BE BASED ON MANUFACTURERS’ HAZARD DATA.
ELECTRIC SHOCK – Can kill
l
Install and earth the welding unitin accordance with applicable standards.
l
Do not touch live electrical parts or electrodes with bare skin, wet gloves or wet clothing.
l
Insulate yourself from earth and the workpiece.
l
Ensure your working stance is safe.
FUMES and GASES - Can be dangerous to health
l
Keep your head out of the fumes.
l
Use ventilation, extraction at the arc, or both, to take fumes and gases away from your breathing
zone and the general area.
ARC RAYS - Can injure eyes and burn skin
l
Protect your eyes and body. Use the correct welding screen and filter lens and wear protective
clothing.
l
Protect bystanders with suitable screens or curtains.
FIRE HAZARD
l
Sparks (spatter) can cause fire. Make sure therefore that there are no inflammable materials
nearby.
NOISE - Excessive noise can damage hearing
l
Protect yours ears. Use earmuffs or other hearing protection.
l
Warn bystanders of the risk.
MALFUNCTIONS - Call for expert assistance in the event of malfunction
READ AND UNDERSTAND THE INSTRUCTION MANUAL BEFORE INSTALLING OR OPERATION.
PROTECT YOURSELF AND OTHERS!
ESAB can provide you with all necessary welding protection and accessories.
WARNING!
Read and understand the instruction manual before installing or operating.
Do not dispose of electrical equipment together with normal waste!
In observance of European Directive 2002/96/EC on Waste Electrical and Electronic
Equipment and its implementation in accordance with national law, electrical equipment
that has the end of its life must be collected separately and returned to an
environmentally compatible recycling facility. As the owner of the equipment, you should
get information on approved collection systems from our local representative. By
applying this European Directive you will improve the environment and human health !
- 20 -
- 21 -
2 INTRODUCCION
™
The Origo Feed 302N P0 wire feeders are designed for semi-automatic MIG/MAG welding with solid wires,
cored and aluminium in services of average and heavy production.
They have a wire feed mechanism of 2 feed rollers engaged and an electronic control system. They can be
installed on the power source or on a wheel kit to move it around the workplace (optional).
4.1) Front panel
1- Knob for setting wire feed speed.
2- Interruptor of manual wire release - Allows the wire to be fed without voltage in the welding gun.
3- Euro-conector for connect welding gun.
4.2) Side console
4- Wire feed mechanism.
4.3) Rear panel
5- Connection for welding current from power source.
6- Connection for control cable from power source.
7- Connection for shielding gas.
8- Brake hub.
9- Inlet nozzle.
3
TECHNICAL DATA
4
CONTROLS AND CONNECTORS
42 - 50/60
1,5 - 22,0
0,6 - 1,6
1,2 - 1,6
1,0 - 1,6
Euro-conector
Yes
Optional
230 x 570 x 380 (without bobbin cover)
230 x 570 x 455 (with bobbin cover)
10,8
Power supply (V - Hz)
Wire feed speed (m/mm)
Wire diameter (mm)
Solid steel
Cored wire
Aluminium
Welding gun connection
Manual feeding of the wire
Bobbin cover
Dimensions (W x L x H) (mm)
Weight (kg)
Summary of Contents for 0402503
Page 6: ...6 1 2 3 8 9 4 6 7 5...
Page 15: ...15 p gina em branco...
Page 16: ...16 p gina em branco...
Page 22: ...22 1 2 3 8 9 4 6 7 5...
Page 31: ...31 white page...
Page 32: ...32 white page...
Page 38: ...38 1 2 3 8 9 4 6 7 5...
Page 53: ...53 P gina en blanco...
Page 54: ...54 P gina en blanco...
Page 55: ...55 P gina en blanco...