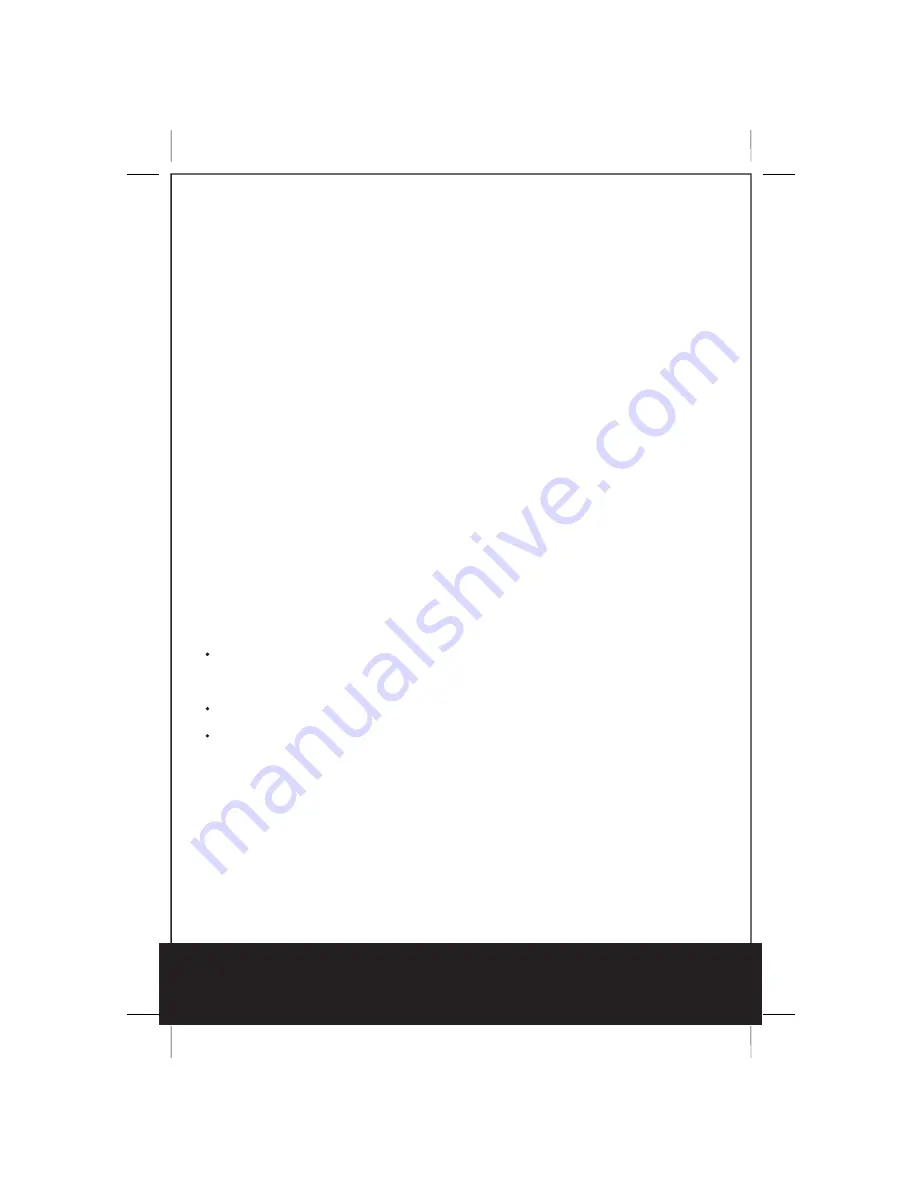
10
400W AUTOMATIC STAINLESS STEEL SUBMERSIBLE CLEAN WATER PUMP
Assembly / Putting The Pump Into Operation
The pump is supplied complete with a H05 RN-F electrical cable with a RCCB and 11/4 fitting for
32mm hose. Attach the necessary discharge pipe and reinforce the seal with a pipe clip. Water
flow, among other things, also depends on the diameter of the discharge pipe. A large diameter
means a greater flow rate, while a smaller diameter has a lower flow rate as a consequence.
Immerse the pump in the fluid to be pumped out (Check the maximum discharge head.)
Please Note! Prevent the Pump from Dry Running.
The pump is put into operation when the RCCB is plugged in and switched on. Note if using any
external 3 pin plug socket ensure that when the RCCB is fitted the socket is still weather proof. In
the event that the pump is lifted or handled, this must be done by the attached handle, not by the
connecting cable. In the event that the pump is submerged, if necessary, a rope or something
similar, which is tied to the handle, must be used.
On silty, sandy or pebbly ground, the pump run must be hung by a rope or chain or situated on a
suitably wide base plate in order to allow it to work submerged. Sand and other abrasive
substances reduce the service life of the components as well as the pump gaskets and should
therefore be avoided. In freezing temperatures, the pumped liquid should be removed from the
pump.
Exposure of the pump to the risk of freezing must be avoided in all cases. The pump must be
drained and be taken to a place protected against freezing temperatures. In order to make the
draining of the pump easier, it is recommended to let the air escape by submerging the pump
with the outlet connections directed upwards.
Note: Please put the pump into the water at an angle so that the air at the bottom of
the pump can escape.
Setting of the On / Off Switching Points:
The on or off switching point of the float switch can be set by means of a change of the float
switch in the float switch fixing / pivot point. Please, check the following before putting it into
operation:
The float switch must be attached in such a way that the ON and OFF switching point levels
can be reached with little expenditure of energy. Check this by putting the pump in a tank
filled with water and carefully lifting the float switch by hand and then letting it sink. In this
way, you can see whether the pump switches itself on and off.
Make sure that the space between the float switch head and float switch fixing / pivot point is
not too small. In the event of too small a space, faultless functioning is not ensured.
When setting the float switch, make sure that the float switch does not touch the bottom
before the pump is switched off. Please note! Risk of dry running.
Overloading Protection / Thermal Motor Switch
The submersible pump is equipped with a thermal motor switch. In the event that the motor
becomes overheated, the motor switch automatically switches the pump off. The cooling period
amounts to 25 minutes and subsequently, the pump switches on again automatically. In the event
that the motor switch operates, it is absolutely essential to find and eliminate the cause (Also see;
Troubleshooting Guide). The information given here may not be considered as instructions for
“home-made” repairs because repairs require specific technical expertise.
In the event of potential malfunctions, one must always contact authorised agent.
Summary of Contents for ERB400SWP
Page 1: ...ERB400SWP 400W AUTOMATIC STAINLESS STEEL SUBMERSIBLE CLEAN WATER PUMP...
Page 2: ...400W AUTOMATIC STAINLESS STEEL SUBMERSIBLE CLEAN WATER PUMP 2...
Page 13: ...13 400W AUTOMATIC STAINLESS STEEL SUBMERSIBLE CLEAN WATER PUMP...
Page 14: ...14 400W AUTOMATIC STAINLESS STEEL SUBMERSIBLE CLEAN WATER PUMP...
Page 16: ......