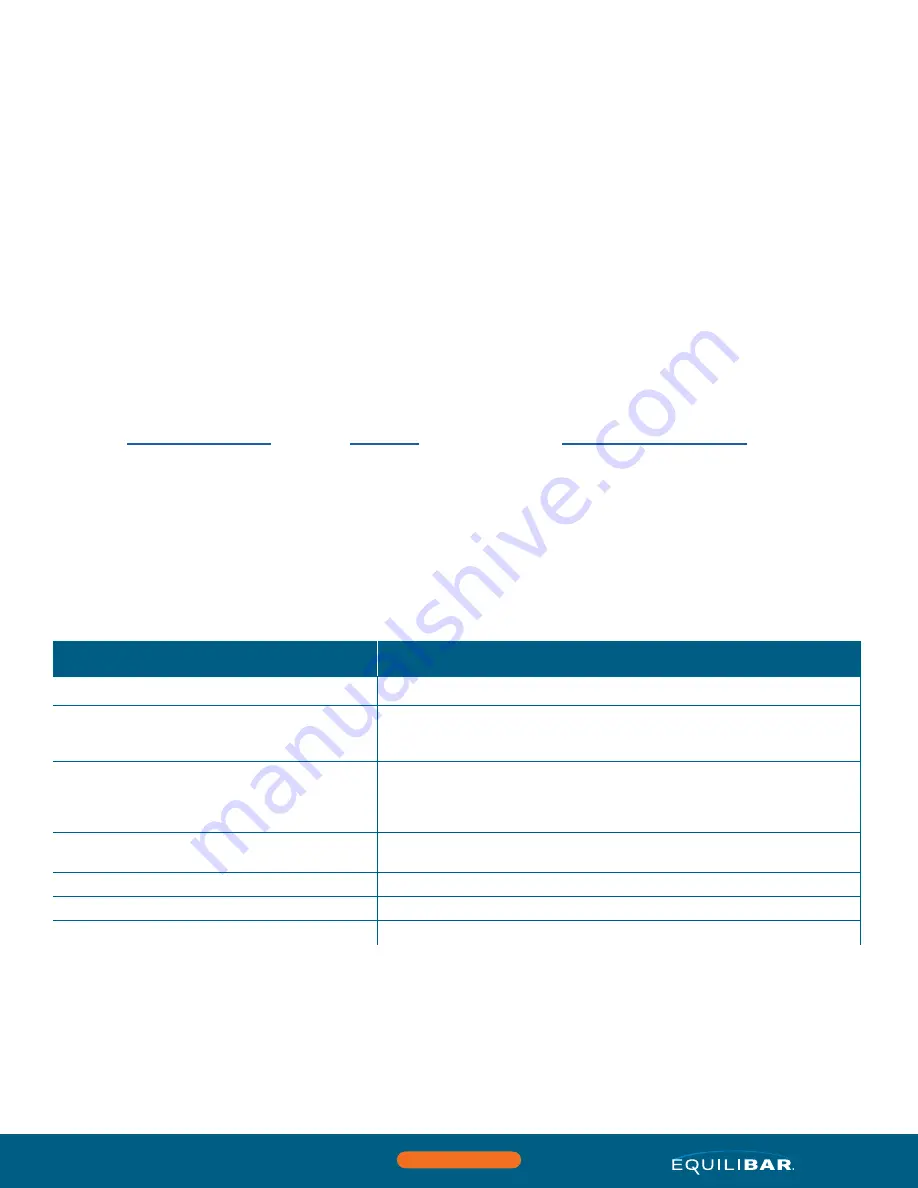
Page 3 of 6
www.equilibar.com
828.650.6590
©2010-2020 Equilibar, LLC
25/08/20 R6
Research Series Precision Back Pressure Regulator
PROBLEM
GUIDANCE
Maximum flow is reduced
Clean out internal orifices
Will not maintain back pressure at low flow rates
1. Inspect the regulator for debris or diaphragm damage which prevents the
diaphragm from sealing against the orifice in the regulator body
2. Contact Equilibar application engineer to review low flow specifications
External leak around diaphragm
1. Check for loose bolts
2. Check for misaligned flanges, O-rings or diaphragm
3. Check for scratched sealing surface
4. Check for O-ring Damage
Chatter on the downstream tubing
1. Increase exhaust piping size
2. Contact factory for additional assistance
Air in process exhaust
Check for ruptured diaphragm
Fluid out of the reference port
Check for ruptured diaphragm
Leaking (not from process ports)
Lubricate and/or stretch O-rings to get better O-ring seal
TROUBLESHOOTING
RATED PRESSURE NOTE
Equilibar regulator bodies have a
Shell pressure rating
based on the body and bolt strength using principles of the ASME B31.3 and
confirmed using hydrostatic testing. These
Shell pressure ratings
are the maximum rating for each design as listed in the technical
brochures. For example, H3P in SS316L (H3PxS) is listed with a maximum pressure rating of 3000 psig.
Equilibar configures individual regulators to the specific customer application which may involve fitting the valve with a thinner diaphragm
to meet precision or low-flow requirements. The diaphragm selection, operating temperature, chemical composition or other factors
cause pressure derating. Therefore, the MAWP printed on an Equilibar BPR label reflects that of the selected diaphragm and application
conditions but will not exceed the Shell pressure rating of the body design.
The maximum pressure rating for the shell is always based on the body and bolt strength and is
not
printed on the product label. Customers
may contact Equilibar engineers if they desire to increase unit MAWP by upgrading diaphragm thickness.
7. Equilibar recommends that reference pressure always be applied
when running the process fluid through the Equilibar, such as in
the case of pressure testing a system that has an Equilibar BPR
installed. This helps prevent the diaphragm from lifting and
deforming into the cap which can have a negative impact on
performance.
8. The BPR is designed to have maximum pilot pressure applied
even when there is no pressurized media at the inlet (I) port. No
damage will result.
9. Start the flow of process fluid after the pilot pressure has been
applied and the diaphragm has been set.
10. Exercise caution when reducing the pilot pressure. The BPR will
attempt to reduce the inlet pressure at the same rate that the
pilot pressure is being reduced. This can result in extremely rapid
release of media through the outlet (O) port of the regulator.
Reduce the pilot pressure as slowly as practical.
11. When preparing for maintenance or shutting the system down,
turn the process fluid off before removing pilot pressure supply
to the pilot port.
INSTALLING (CONTINUED)
MAINTENANCE NOTES
•
Maintain strainer or filter upstream of device to avoid debris getting trapped in the orifices
•
Annual inspection of diaphragm integrity is recommended, especially for applications where there is strong or regular pulsing (i.e.
reciprocating pump, etc.).
•
It is expected that O-rings and diaphragms will need to be replaced on a regular basis, the timing of which is dependent on the
application.
•
It is recommended to order spare parts prior to performing maintenance. The following replacement part kits are available for order:
•
RBK – Rebuild Kits – replacement parts for O-rings AND diaphragms
•
DI – Diaphragm Kit – replacement parts for diaphragms only
•
OR – O-ring Kit – replacement parts for the O-rings only
•
for videos or
for more information at
PREPARING FOR MAINTENANCE OR TROUBLESHOOTING
•
When shutting the system down for maintenance or troubleshooting, turn the process fluid off before removing pilot pressure supply
to the pilot port. This step will prevent a sudden release of system media pressure through the BPR.
•
Release the pilot pressure and remove the pilot port piping to clear the BPR for maintenance. Equilibar BPR’s can be serviced ‘inline’
and do not need to be removed from the system piping.
•
Loosen the bolts in the cap of the BPR and disassemble wearing proper protective equipment. See exploded views on page 4-5.
•
Inspect diaphragm and O-rings for integrity to determine if they need to be replaced. Check for scratched O-ring sealing surfaces.
•
Clean all wetted surfaces to remove any residual process fluid and particulates.
•
Reassemble the clean parts with new diaphragm and O-rings following the instructions on pages 4-5.