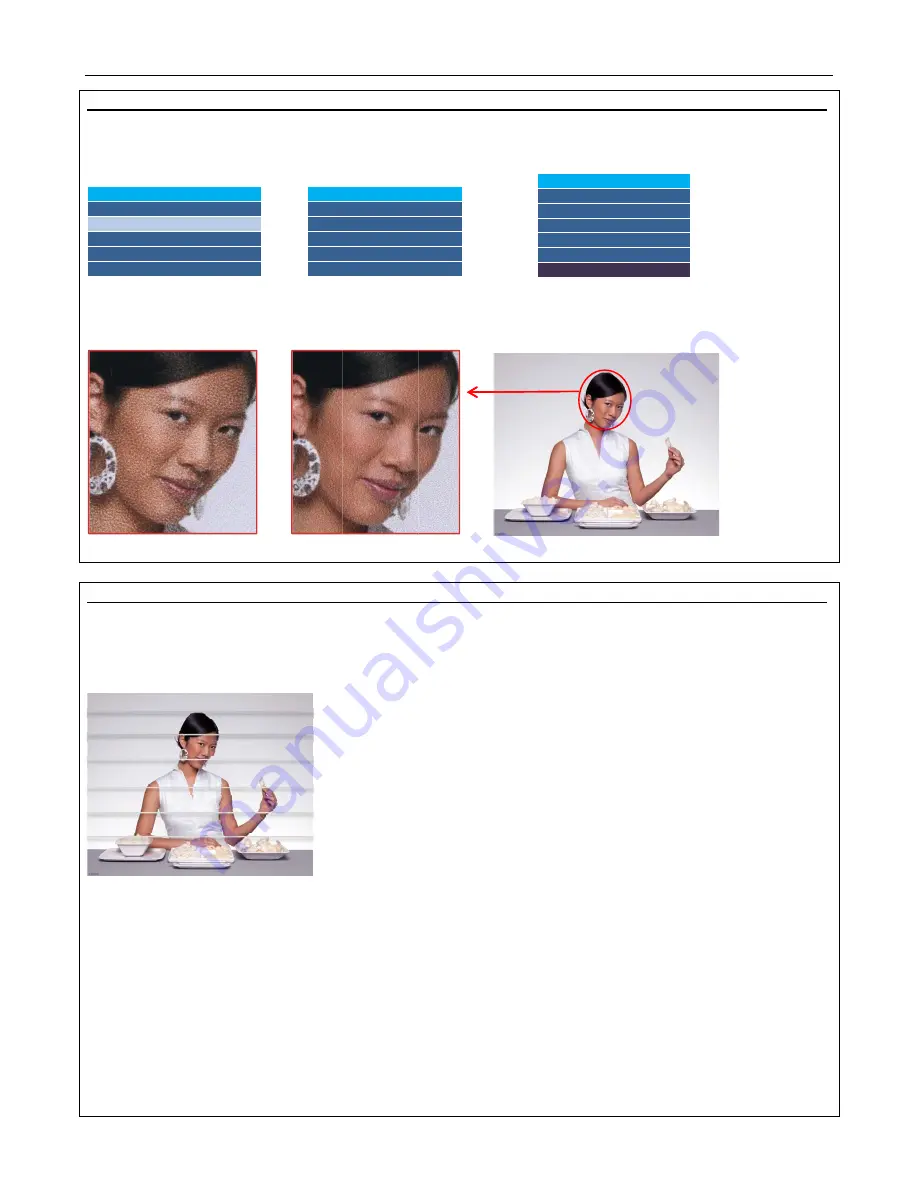
Epso
4
.
T
A.
H
Most
The
Fo
Befo
B.
Q
Depe
and
wors
Coun
1)
1
s
2)
m
3)
Us
4)
us
5)
Us
6)
re
7)
He
Note
RIP
Se
●
Plat
●
Hea
●
Rol
●
Ten
●
Me
n
Engineering
TROUBLE
SH
Head
Alignm
t
of
grainine
head
Alignm
or
head
Align
ore
head
align
Quality
Band
ending
on
th
causing
head
se
:
CR
block
ntermeasure
t
of
all,
check
ake
sure
the
se
the
best
m
se
the
correc
se
correct
he
educe
the
ink
ead
moveme
e
:
for
quality
ettings
:
ten
Gap
(1,5,
2,
ad
Alignment
l
Type
(Side
In,
S
nsion
Measurem
dia
Tension
g
Europe
HOOT
QUIC
ment
ss
quality
ph
ment
can
be
d
nment
detai
nment
ding
he
heater
tem
d
gap
reduct
ed
with
med
e
to
reduce
q
k
missing
no
e
head
alignm
media
profile
ct
resol
eater
temp
s
k
duty
too
ent
data
wid
y
banding
sp
2,5)
Side
Out)
ent
CK
GUIDE
henomenon
done
for
2
m
Media
t
l,
please
refe
after
hea
mperature
an
tion
with
the
dia
Jam
quality
bandi
zzles
perf
ment
and
pa
e
and
Ink
Lim
ution
capabi
ettings
:
too
o
much
ink
w
th
or
Full
wid
ecification,
p
Head
A
input
T
Range:
SC
‐
S306
is
coming
fro
media
selectio
hickness
is
asked
er
to
section
ad
alignment
nd
media
rea
e
media
H
ng
:
form
light,
m
per
feed
has
mit
according
ility
regardin
high
tempe
will
increase
m
dth
?
depend
please
refer
Alignment
0.2
mm
Thickness.
0.1
‐
1.0
mm
600/610
Tech
om
wrong
he
on:
[
RIP
Sett
d
in
RIP
Settings
n
STEP
B
Cus
t
action
with
e
ead
strikes.
medium
or
he
s
been
perfo
g
media
capa
ng
your
signa
rature
decre
media
buckli
ding
on
signa
to
section
[
1
nical
Guide
ead
alignmen
ings
]
or
(
Me
use
aut
tomize
Setti
environment
Head
strikes
eavy
cleaning
rmed
with
th
bilities
age
applicatio
eases
quality
ing
age
applicati
1.
What
SC
‐
S
Head
A
●
Auto
●
Auto
●
Man
●
Man
[OK]
P
nt.
dia
xx
]
o
or
manual
ings
>
B2.
He
t,
some
medi
can
cause
in
g
(maintenan
he
media
loa
on
(Banners,
ion,
choose
t
S30600/610
C
Alignment
o
(Uni
‐
D)
o
(Bi
‐
D)
ual
(Uni
‐
D)
ual
(Bi
‐
D)
roceed
[
↖
]
Back
ead
Alignme
ia
can
buckle
nk
scratch
on
nce
menu)
aded
,
billboard,
e
the
correct
s
CAN
DO
]
k
P a g
ent
e
more
or
les
n
the
media
etc)
setting
e
|
16
ss
or