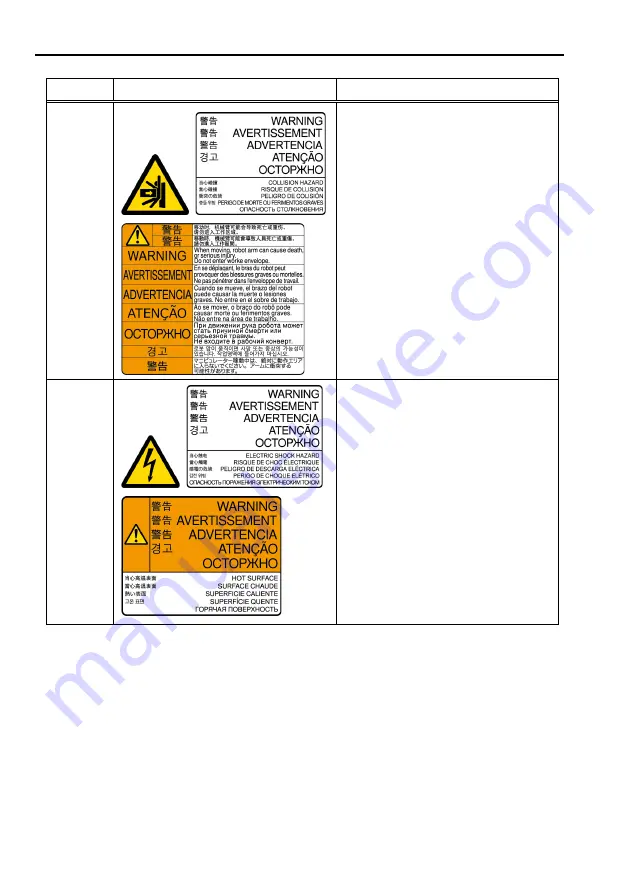
Safety Precautions
24
Safety Manual Rev.4
Location
Warning label
Note
B
Do not enter the operation area
while the Manipulator is moving.
The robot arm may collide against
the operator. This is extremely
hazardous and may result in
serious safety problems.
C
Hazardous voltage exists while
the Manipulator is ON.
Summary of Contents for RT3B-401SS
Page 2: ...Robot System Safety Manual Read this manual first Rev 4 ...
Page 12: ...x Safety Manual Rev 4 ...
Page 44: ...Safety Precautions 30 Safety Manual Rev 4 Location of Labels G1 E 1 B UL B A C C A UL F ...
Page 49: ...Safety Precautions Safety Manual Rev 4 35 Location of Labels LS10 B B A 1 D D C C C ...
Page 50: ...Safety Precautions 36 Safety Manual Rev 4 Location of Labels LS20 B B A 1 D D C F C E ...
Page 51: ...Safety Precautions Safety Manual Rev 4 37 Location of Labels T3 B A C 1 D C C C C D C C H ...
Page 52: ...Safety Precautions 38 Safety Manual Rev 4 Location of Labels T6 B A C 1 D C C D C C H ...
Page 53: ...Safety Precautions Safety Manual Rev 4 39 Location of Labels RS3 B A C 1 D C E C C C C B UL F ...
Page 65: ...Safety Precautions Safety Manual Rev 4 51 Location of Labels T6 B 1 B C 1 H C D C C A C 2 ...