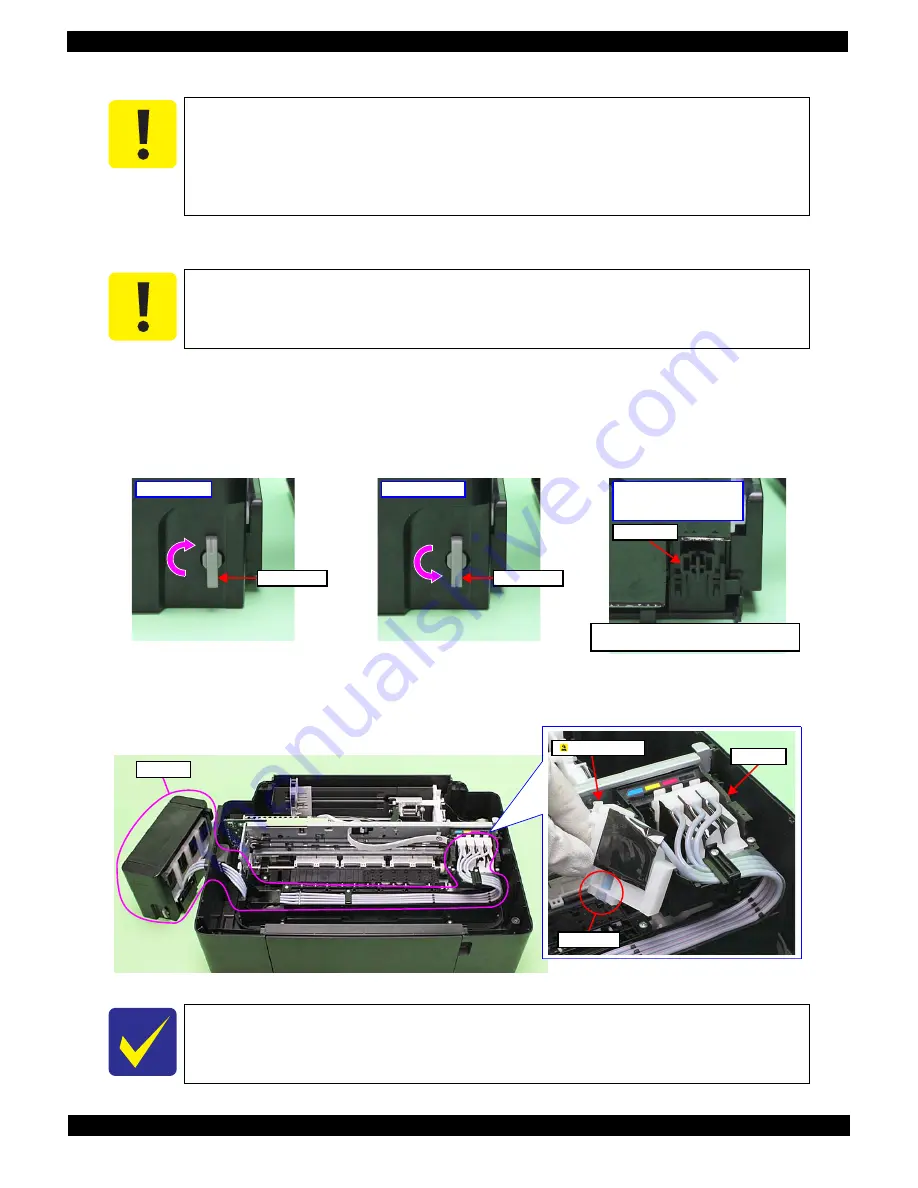
Confidential
Disassembly/Reassembly
Overview
11
L200/L201/L100/L101
Revision A
Means do to minimize the ink spill
Before disassembling, confirm that the printer is in the following condition.
Choke Valve is closed
•
Before disassembling:
Turn the Valve Lever and be sure to close the Choke Valve.
•
After reassembling is complete:
Open the Choke Valve to perform the print inspection.
•
Before returning the printer to the user after repairing:
Make sure to turn the Valve Lever up to the choke position to close the Choke Valve before packing the printer.
Figure 1-2. Opening/closing the Choke Valve
Adapter Assy is removed
Before disconnecting the joint parts of the ink path, make sure that the Adapter Assy is removed from the Carriage.
Figure 1-3. Adapter Assy
Even observing the points described in this section, ink may spill in the following situations.
Therefore, be careful not to contaminate the inside of the printer or its surroundings by
preparing the container to receive the leaked ink, or the like.
When removing the Valve Assy, some ink will spill from both ends of the ink tube even
the Valve Lever is closed.
When removing the Tube Assy, all the ink in the ink tube will spill.
Do not turn the Valve Lever too much when closing the Choke Valve, otherwise, the Valve
Lever and/or Valve Assy may get damaged.
The Adapter Assy has an ink valve which cuts off the ink path when removing the Adapter
Assy from the carriage.
Valve Lever
Valve Lever
Open position
Choke position
Choke Valve shaft is secured more tightly
in Choke position than in Open position.
Choke position
(When checking with the
Valve Lever removed.)
Valve shaft
Ink path
Carriage
Ink valve
Adapter Assy
Summary of Contents for L200
Page 1: ...SERVICE MANUAL CONFIDENTIAL Color Inkjet Printer L200 L201 L100 L101 SEMF10 001 ...
Page 8: ...Confidential CHAPTER 1 DISASSEMBLY REASSEMBLY ...
Page 33: ...Confidential CHAPTER 2 ADJUSTMENT ...
Page 37: ...Confidential CHAPTER 3 MAINTENANCE ...