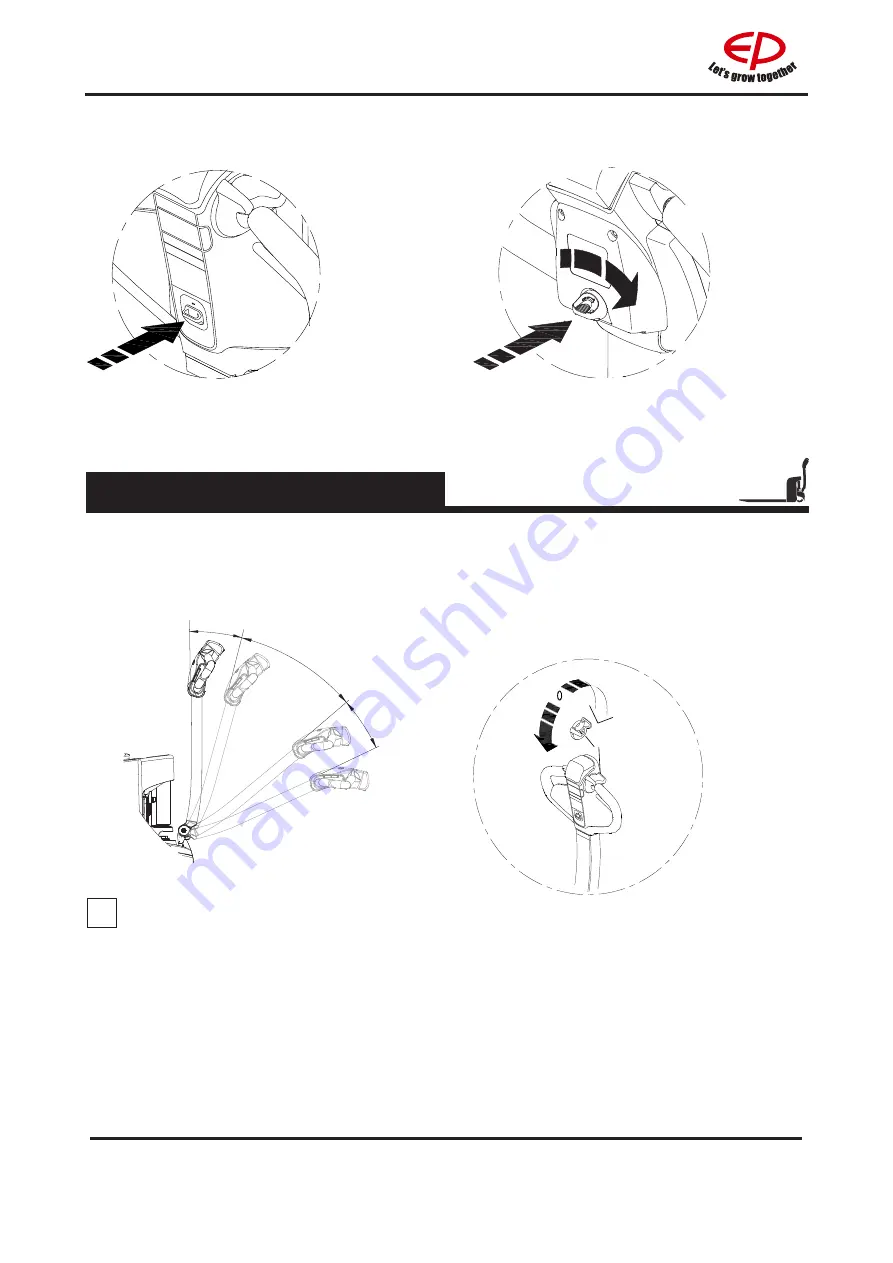
REV. 09/2020
12
B
2.Open the key switch to start the truck
WPL201
RPL201/RPL201H/RPL202
/
EPL151
1.Running
Running area
Running area
Rotary button
Control the running direction and
speed of the truck using the drive
switch (1). (the large the rotary angle,
the faster corresponding speed)
2.3.3
Running, swerving and braking
1
Forward
Backward
When using the truck on a ramp or a uneven road, please lift the leg of the forklift to prevent
its bottom from colliding with the road surface.
i
NOTE
Summary of Contents for EPL151
Page 11: ...REV 09 2020 3 A RPL201 RPL201H RPL202 EPL151 ...
Page 45: ...REV 09 2020 4 E RPL201 RPL201H ...
Page 46: ...REV 09 2020 5 E RPL202 ...
Page 50: ...REV 09 2020 9 E EPL151 ...
Page 51: ...REV 09 2020 10 E HPL152 ...
Page 52: ...REV 09 2020 11 E WPL201 ...
Page 53: ...REV 09 2020 1 F Lithium ion battery ...