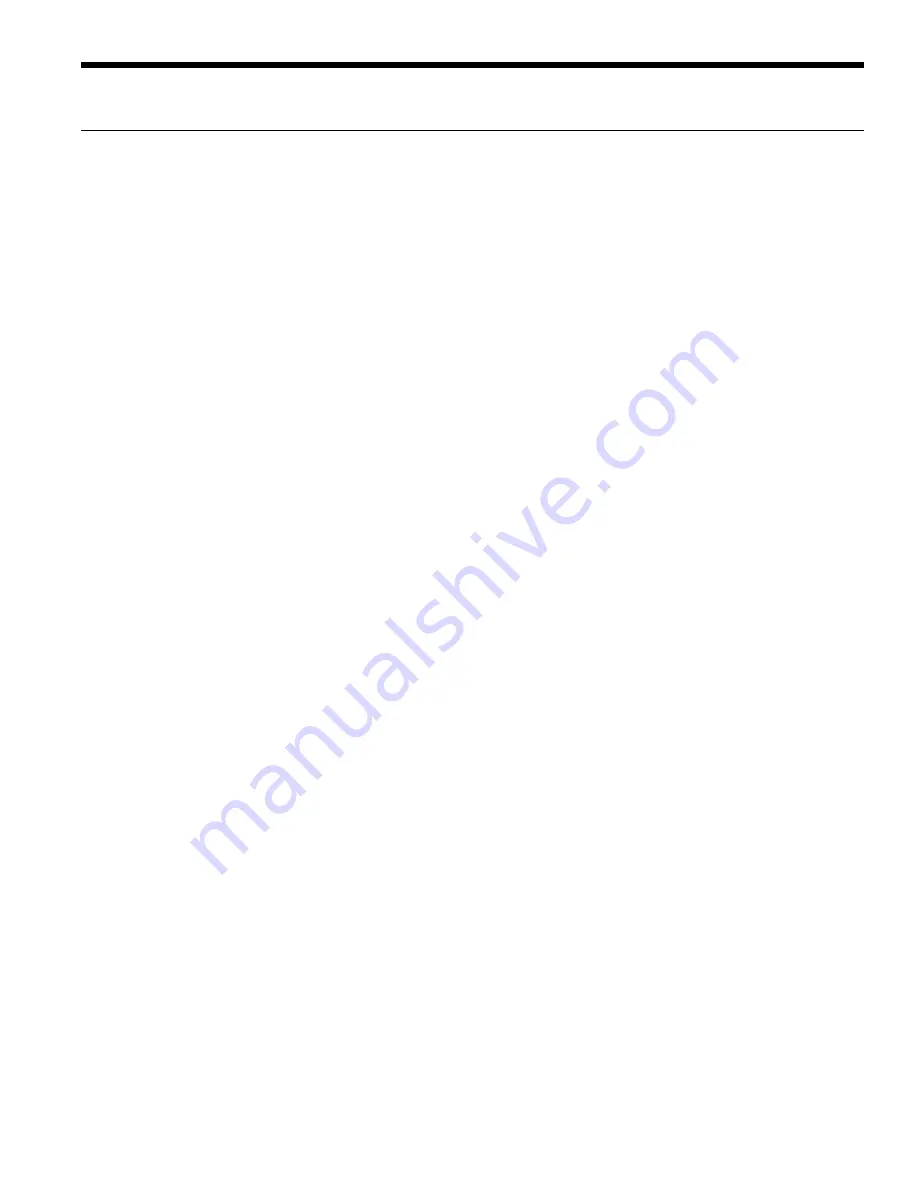
23
NDS OUTDOOR SPLIT INSTALLATION MANUAL
Leak Testing
The refrigeration line set must be pressurized and
checked for leaks before purging and charging the unit.
To pressurize the line set, attach refrigerant gauges to the
service ports and add an inert gas (nitrogen or dry carbon
dioxide) until pressure reaches 60 to 90 PSIG. Never use
oxygen or acetylene to pressure test. Use an electronic leak
detector or a good quality bubble solution to detect leaks
on all connections made in the field. Check the service
valve ports and stem for leaks and all connections made in
the field. If a leak is found, repair it and repeat the above
steps. For safety reasons do not pressurize the system
above 150 psi. Purge pressure from line set. The system is
now ready for evacuating and charging.
System Evacuation
Ensure that the line set and air coil are evacuated before
opening service valves to the split unit. The line set must be
evacuated to at least 200 microns to remove the moisture
and air that may still be in the line set and coil. Evacuate
the system through both service ports to prevent false
readings on the gauge because of pressure drop through
service ports.
Charge Amount When Using NAH Air Handler
The Envision Split is shipped with a facotry pre-charge. This
volume of refrigerant is not sufficient to run the system and
additional refrigerant must be added. If using an NAH Air
Handler please refer to the table in this section for charge
amounts to be added. The “Factory Charge” column is the
charge amount the compressor section/split is shipped
with from the factory. The “Charge Amount with NAH Air
Handler” column is the total amount of charge for the NAH
Air H Compressor section/split. This column does
not factor in additional refrigerant needed for the line set.
The installer of the system must add charge appropriately
for the specific length of the line set. A 3/8 in. liquid line is
calculated at 0.50 oz. of charge per linear foot, and a 1/2
in. liquid line is calculated at 1.0 oz. of charge per linear
foot using R-410A refrigerant. The suction line will not hold
“liquid” and should be ignored for the charge calculation.
Example:
NDS036/NAH036 with 20 ft. of 3/8 in. liquid
line. Remember that when using the NAH
Air Handler, the column “Charge Amount
with NAH Air Handler” will be used. Now
calculate for the additional 20 ft. ineset.
Additional refrigerant to be added = (20 ft. x 0.5 oz.)
= 10 oz.
Solution:
10 oz. should be added to the recommended
charge of 86 oz. found in the “Charge Amount
with NAH Air Handler” column for a total charge
of 96 oz.
Refrigeration
After initial charge, the system should be operated and
the system subcooling and superheat verified to the Unit
Operating Parameters table.
If an air handler manufactured by others is used then
refrigerant should be added to the Envision Split factory
pre-charge. Refrigerant should be added for liquid line
length. This should result in a slightly under-charged
system exhibiting low subcooling and high superheat.
As charge is added, the subcooling should rise and the
superheat should fall.
Charging the System
Charge Method – After purging and evacuating the line set,
fully open the service valves counterclockwise. Add R-410A
(liquid) into the liquid line service port until the pressure
in the system reaches approximately 200 PSIG. Never add
liquid refrigerant into the suction side of a compressor.
Start the unit and measure superheat and subcooling. Keep
adding refrigerant until the unit meets the superheat and
subcooling values in the Operating Parameters tables.
Checking Superheat and Subcooling
Determining Superheat
1.
Measure the temperature of the suction line at the
point where the expansion valve bulb is clamped.
2. Determine the suction pressure in the suction line
by attaching refrigeration gauges to the schrader
connection on the suction side of the compressor.
3. Convert the pressure obtained in Step 2 to the
saturation temperature by using the Pressure
Temperature Conversion Chart for R-410A.
4. Subtract the temperature obtained in Step 3 from
Step 1. The difference is the amount of superheat for
the unit. Refer to the Operating Parameters tables for
superheat ranges at specific entering water conditions.
Superheat Adjustment
TXVs are factory set to a specific superheat; however, the
superheat should be adjusted for the application. To adjust
the TXV to other superheat settings:
1.
Remove the seal cap from the bottom of the valve.
2. Turn the adjustment screw clockwise to increase
superheat and counterclockwise to decrease
superheat. One complete 360° turn changes the
superheat approximately 3-4°F, regardless of
refrigerant type. You may need to allow as much as 30
minutes after the adjustment is made for the system to
stabilize.
3. Once the proper superheat setting has been achieved,
replace and tighten the seal cap.
WARNING:
There are 8 total (360°) turns on the superheat
adjustment stem from wide open to fully closed. When