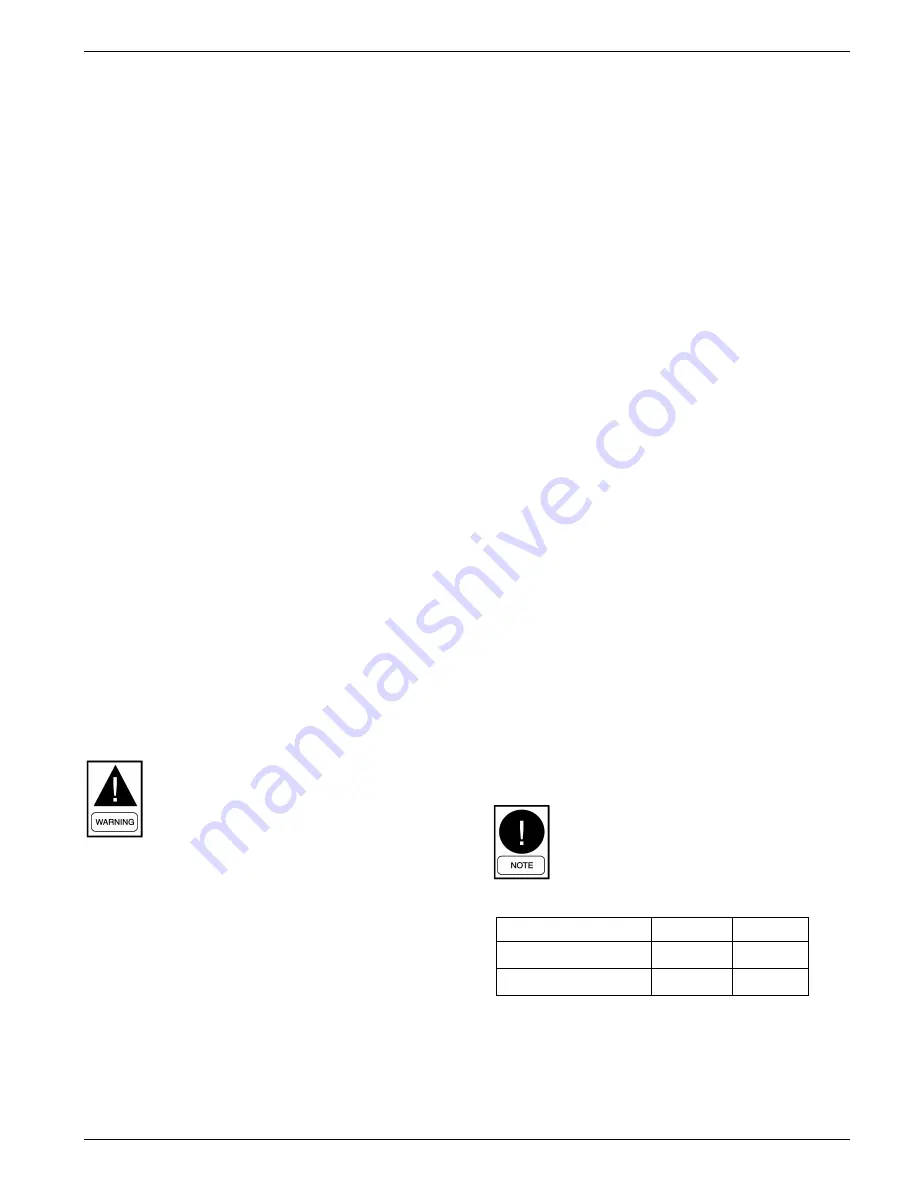
FORM ET145.18-IOM1 (115)
ENVIRO-TEC
27
10. UNIT START-UP
A.
Pre-Start-up Checklist
When the installation is complete and the system is cleaned
and flushed, open the supply and return shut-off valves at
each unit, refill the system and bleed off all air.
Before energizing the unit, the following system devices must
be checked:
□
Is the high voltage power supply correct and in
accordance with the nameplate ratings?
□
Is the field wiring and circuit protection the correct size?
□
Is the unit electrically grounded?
□
Is the low voltage control wiring correct per the unit
wiring diagram?
□
Is vibration isolation provided? (unit isolation pad,
flexible hoses, etc.)
□
Are the low / high-side pressure temperature caps
secure and in place?
□
Are all the unit access panels secure and in place?
□
Is the thermostat in the OFF position?
□
Is the water flow established and circulating through all
the units?
□
Is the ductwork (if required) correctly sized, run, taped,
and insulated?
□
Does the indoor blower turn freely without rubbing?
□
If applicable has glycol fluid been added in the proper
mix to prevent freezing in closed system application?
□
Are clean, properly sized air filters in place?
□
Is the condensate drain pipe firmly secured to both drain
riser and drain pan stub?
B.
Initial Unit Start-up
1.
Close disconnect switches on all units to provide line
power.
During installation, testing, servicing, and
troubleshooting of this product, it may be
necessary to work with live electrical components.
Failure to follow all electrical safety precautions
when exposed to live electrical components could
result in serious injury or death.
2.
Set the thermostat to the highest temperature setting.
3.
Set the thermostat system switch to COOL; the fan
control switch to AUTO. The compressor should NOT
run.
4.
Reduce the temperature control setting until the
compressor and supply fan are energized. Water
temperature leaving the heat exchanger should be
warmer than the entering water temperature (approx. 9-
12
o
F). Blower operation should be smooth. Compressor
and blower amps should be within the nameplate data
values. The suction line should be cool, with no frost
observed in the refrigerant circuit.
5.
Turn the thermostat switch to the OFF position. The
compressor and fan should stop running, and the
reversing valve should de-energize.
6.
Leave the unit off for approximately 5 minutes to allow
for pressure equalization.
7.
Turn the thermostat to the lowest setting.
8.
Set the thermostat system switch to the HEAT position.
The compressor should NOT run.
9.
Adjust the temperature setting upward until the
compressor and supply fan are energized. After several
minutes, warm air should be detected at the supply
register. A water temperature
decrease
of approximately
5-9
o
F across the heat exchanger should be noted. The
blower and compressor operation should be smooth,
with no frost observed in the refrigerant circuit.
10. Set the thermostat to maintain the desired space
temperature.
11. Check all water connections for any leaks, including
condensate drain hose connections.
C.
System Loop Temperature
Loop temperatures affect unit performance, power
consumption (efficiency), maintenance and reliability, and
noise levels. High entering water temperatures (EWT) in
cooling mode above rated conditions of 86
o
F EWT will
increase power consumption and increase compressor noise
levels. Sustained operation above 100
o
F EWT may increase
maintenance costs and increased compressor noise may
affect occupancy comfort. Unit is designed to operate up to
110
o
F EWT for intermittent periods when system loop
temperatures become elevated under high load conditions. It
is not recommended to set system loop temperatures at
110
o
F in case of high load conditions cause supply loop
temperatures to exceed 110
o
F EWT. Unit sound performance
may be negatively impacted at high EWT.
When in heating season maximum operating loop
temperature is 90
o
F EWT. It is recommended to maintain
system loop temperatures at or above rated conditions of
68
o
F EWT for optimal unit performance. If system loop
temperatures are low where freezing the coaxial is possible,
system loop must contain a glycol fluid mixture that is
adequate to prevent freezing. Minimum loop temperature
with glycol mixture is 20
o
F EWT. Lower loop temperatures
will result in lower efficiency and heating capacity.
High system loop temperatures may negatively
affect unit performance, efficiency, maintenance
and reliability, and noise levels.
Operating Limits
COOLING
HEATING
MIN. ENTERING WATER
30
o
F
20
o
F
MAX. ENTERING WATER
110
o
F
90
o
F
Summary of Contents for VB09-36
Page 6: ...FORM ET145 18 IOM1 115 ENVIRO TEC 6 FIGURE 1 Cabinet Chassis Model Nomenclature ...
Page 7: ...FORM ET145 18 IOM1 115 ENVIRO TEC 7 ...
Page 34: ...FORM ET145 18 IOM1 115 ENVIRO TEC 34 APPENDIX PSC MOTOR WIRING DIAGRAM ...
Page 35: ...FORM ET145 18 IOM1 115 ENVIRO TEC 35 ECM WIRING DIAGRAM ...
Page 36: ...FORM ET145 18 IOM1 115 ENVIRO TEC 36 CONTINUOUS FAN WITH ECM WIRING DIAGRAM ...
Page 37: ...FORM ET145 18 IOM1 115 ENVIRO TEC 37 MOTORIZED DAMPER ECM WIRING DIAGRAM ...