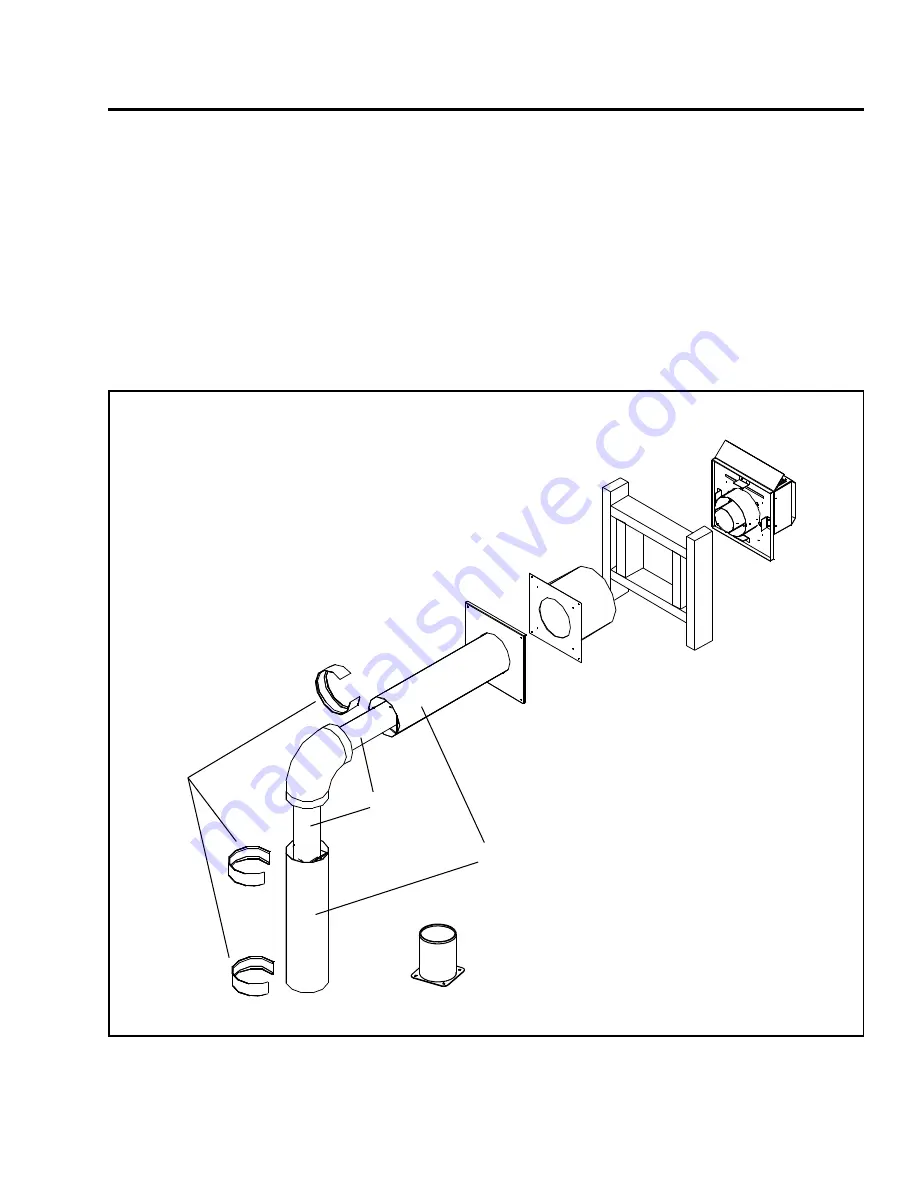
Figure 23: Assembly of Venting Kit.
Initial Installation
QUALIFIED INSTALLERS ONLY
Wall framing
Horizontal wall
termination
Wall thimble
fire stop
Inside finished collar
Decorative
brass rings
Exhaust 4"
flex pipe
Combustion air
6
5
/
8
" outer pipe
Flue pipe adaptor
19. Place a bead of high temperature silicone on the flue pipe and slide the flex liner over the collar, secure the flex
liner with three (3) sheet metal screws evenly spaced.
20. Align all straight sections of pipe, slipping all joints together and installing with three (3) sheet metal screws
evenly spaced.
21. Install the brass decorative rings around each joint making sure this decorative ring covers the sheet metal
screws that secure each section of pipe together and secure to vent pipe in the slotted tab on the backside of
the pipe so that the fastener would not be seen.
22. Secure the horizontal section of pipe to the inside finished collar by installing a screw in the tab on the inside
finished collar. This will prevent the pipe from being disconnected at the vent terminal.
23. Light the appliance and ensure proper operation.
17