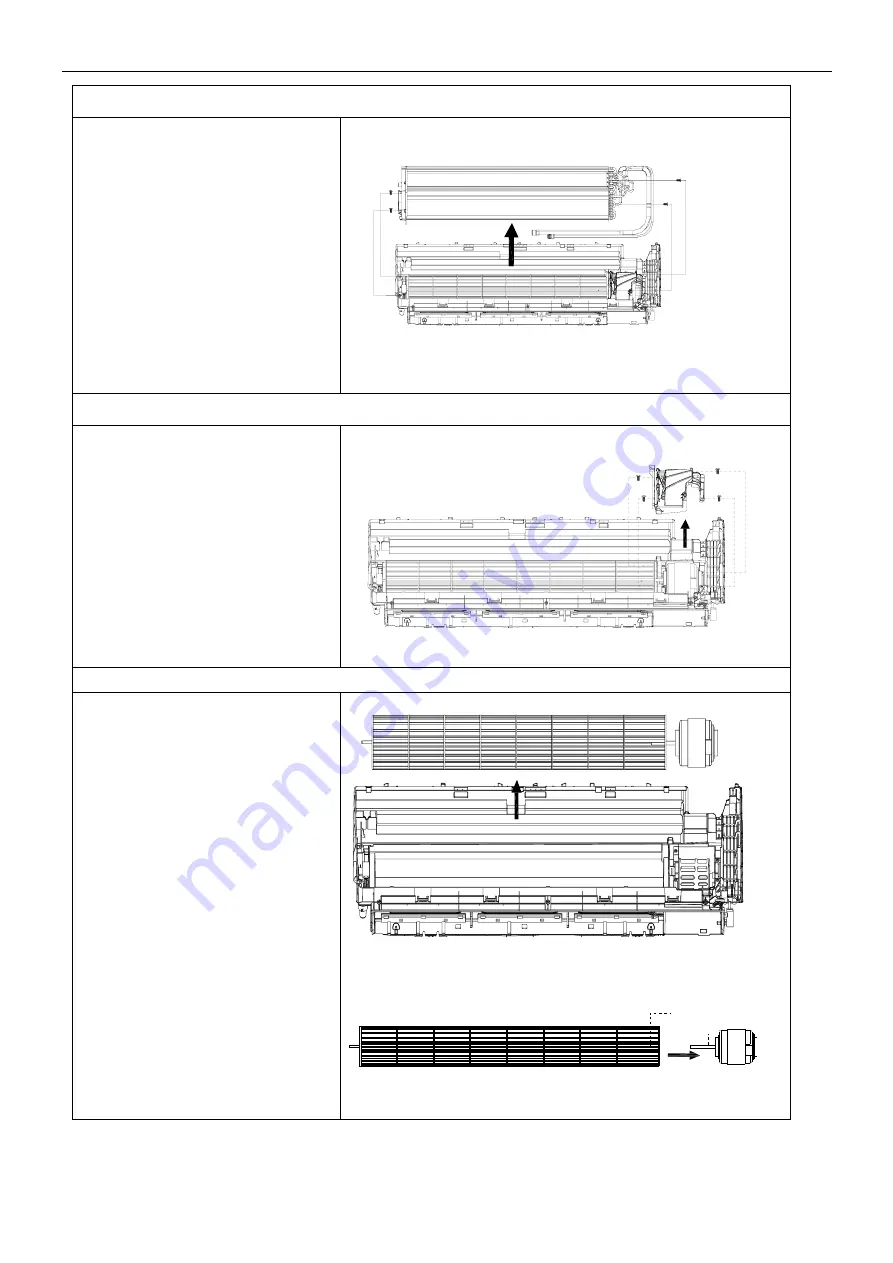
Air Conditioner Service Manual
73
9. Disassembly the evaporator
A. Unfix 2 screws of left side shown as
picture.
B. Unfix 2 screws of right side on motor
cover/right support plate.
C. Take the evaporator out from unit by
uplifting the IUPUT/OUTPUT pipes
slightly.
螺钉
螺钉/卡扣
10. Remove the MOTOR COVER
Unfix 4 screws on the motor cover with
base frame.
螺钉
11. Disassembly fan motor and fan blade.
A. Uplift the fan blade and fan motor,
take the base frame out.
B. Unfix one screw on the axis of fan
motor, and you can get fan blade and
fan motor separately.
螺
钉
screws
motor
cover
screws
screw