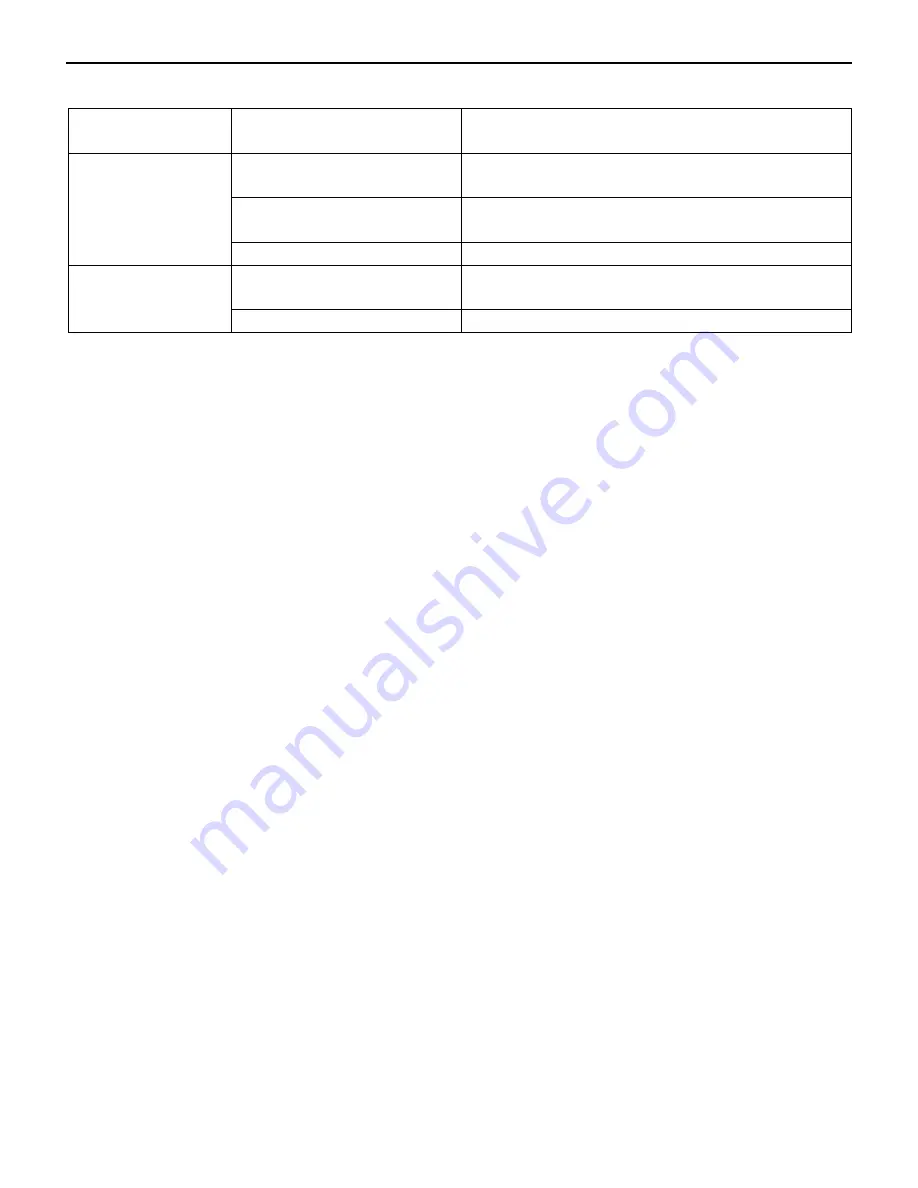
A
CU MANUAL
IOM-14
46 of 46
Feb 06 R4
TX valve not opening
Check for high superheat and correct problem as
required.
High Suction
pressure
System load higher than
design
Determine reason for high load and correct as
necessary.
Too much air flow
Check airflow, balance system air. Check blower
speed. Repair as required.
Inefficient compressor
Check and replace as required.
Noisy Compressor
Scroll compressor running
backwards
Check rotation with gauges Reverse direction of
scroll compressor as required
Compressor damaged
Check and replace as required