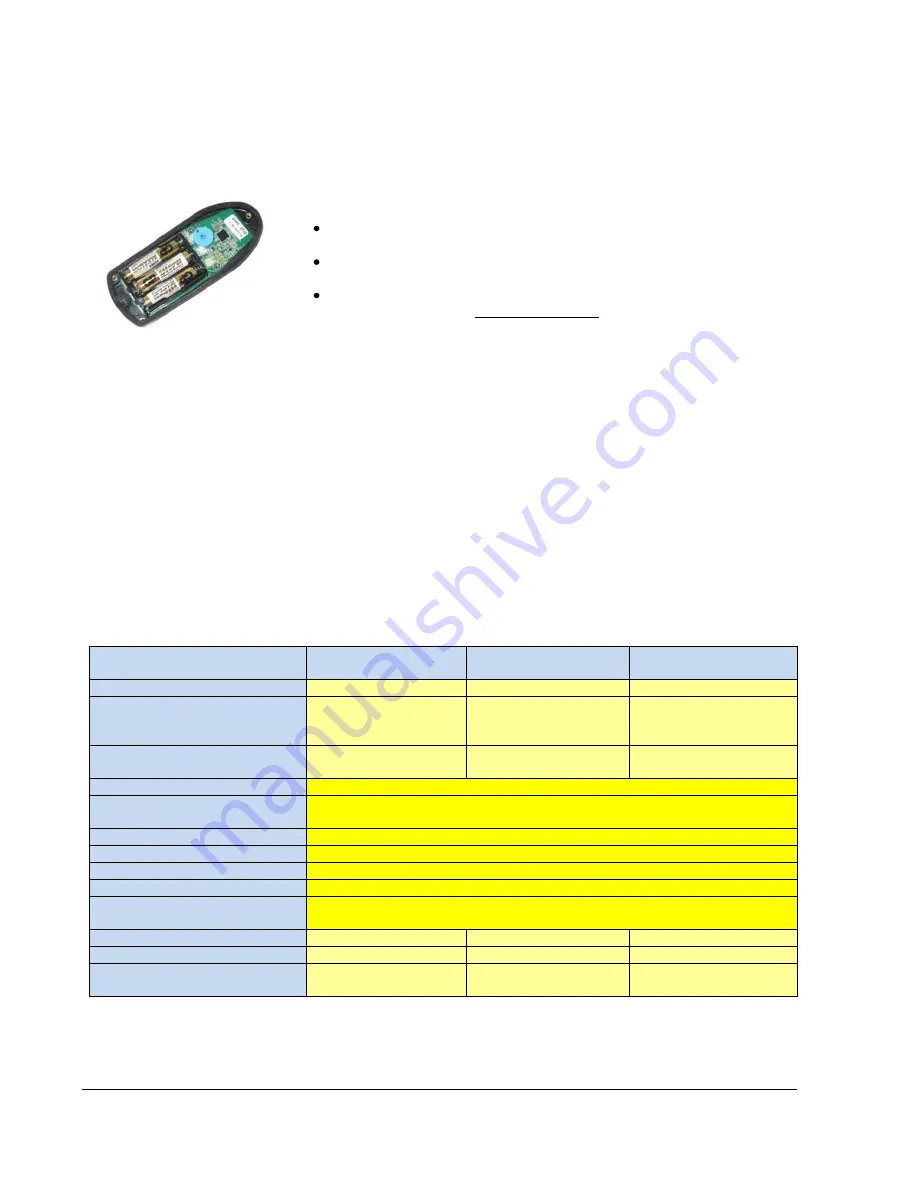
XF
Rev: 4, 2010-02-01
Page 8
2.2.6.
Battery replacement
The remote control uses three regular AAA/LR03 alkaline batteries. The battery
life is more than two seasons under normal leisure use.
When replacing batteries, open the unit by unscrewing all five screws.
NB:
The screws are of different lengths and have O-rings under the screw
heads.
Replace the batteries and make sure all 3 batteries have the
(
+
)
and the
(
–)
correct.
Reassemble the back cover and carefully screw the parts together until
the housing gasket is slightly compressed. The remote will remain
splashproof as long as the O-rings and gasket are intact with correct
compression.
NB:
To ensure a long lifetime, this remote control has acid-proof machine
screws and screw inserts in the housing.
3. Spesifications
3.1.
Technical specifications wireless remote control
Wireless remote:
Motor Control Unit:
Remote Control Unit:
Model:
RC-01
ECU-01
RCU
Power supply:
3 x 1.5 V DC
(3 x AAA/LR03
batteries)
From thruster
(integrated)
From thruster
(integrated)
Battery life:
2
–3 years
(normal leisure use)
Not applicable
Not applicable
Communication:
Two-way, narrowband, GFSK modulation
Operating frequency:
868.075
– 869.125 MHz, CE (EU/EFTA)*
902.175
– 903.025 MHz, FCC (US/Canada)*
Channels:
16 for communication
Channel separation:
50 kHz
Address range:
65.535 (16 bit), spread among the 16 channels
Temperature range:
-20 to +60 degrees Celsius/-4 to +131 degrees Fahrenheit
Relative humidity
(without condensation):
20%
– 90%
Weight:
105 g
Model dependent
120
Dimensions (HxWxD):
129x53x23 mm
Model dependent
150x200x40mm
Environment protection:
Splashproof
IP 41
IP41
* May apply to other countries. For information, please contact local authorities for the country concerned.
** Conditional upon correct installation and intact rubber gasket and O-rings