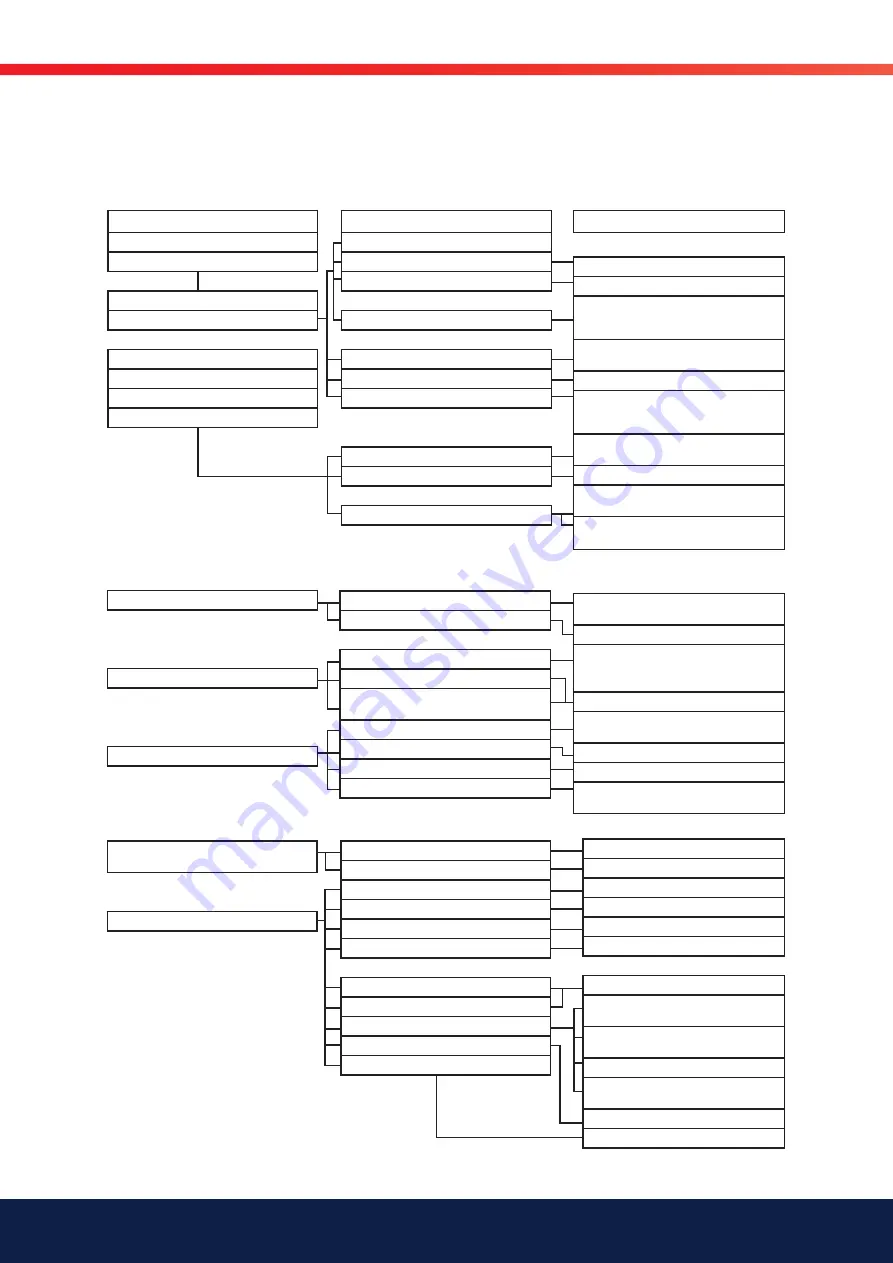
28
Bentone B55/B65 RME
General
9. FAULT LOCATION
9.1
Burner will not start
Symptom
Motor starts
Burner pre-ventilates
Flame formed
Burner trips
Motor starts
Burner pre-ventilates
No lame formed
Burner trips
Causes
Unstable lame
Excess air
Low oil pressure
Incorrect combustion apparatus settings
Flame monitor does not register light
Defective lame monitor
Defective oil burner control
No oil
False light
No spark
Remedies
Adjust the damper
Check the oil pressure
Check the nozzle in relation to the
combustion apparatus dimensions and the
ignition electrode position
Check the lame monitor is clean and can
register light
Check with using new photocell
Check using new oil burner control (Note:
replacement of photocell recommended if oil
burner control replaced)
Check the oil supply to the burner and that
there are no air bubbles in the pump
Check function of solenoid
Check lame monitor does not register
ambient light
Check high voltage wiring and ignition
electrodes
Burner does not start
Burner pre-ventilates
Burner stops
Fuse blown
Boiler thermostat has not reset
Overheating protection has deployed
Defective preheater
Defective oil burner control or
lame monitor
No oil supply
Too great a pressure drop at brake plate
Too strong draught prevents lame forming
No spark
Check and replace fuse as necessary.
Investigate cause of fault
Adjust thermostat
Reset the overheating protection.
Investigate the cause of its deploying.
Remedy fault
Check by replacing with new
Check that tank, oil lines, solenoid valves,
pump and nozzle are in good condition
Adjust the burner
Correct the boiler draught
Check the ignition transformer. Check the
ignition electrode settings and ceramics
Burner pulsates at start with
hot lue gases
Burner pulsates at start
Too strong a draught
Too great a pressure drop at brake plate
Nozzle partially blocked
Oil pressure too low
Flue blocked or damaged
Fan wheel slipping on shaft
Pump coupling loose or worn
Preheater clogged
Delayed ignition
Too strong a draught
Too great a pressure drop at brake plate
Correct the boiler draught
Adjust the burner
Replace nozzle
Check and adjust
Check and correct
Check and tighten
Replace
Check ignition electrode adjustment
(refer to technical data)
Check ignition electrodes
not damaged
Check high voltage wiring
Check position of nozzle
assembly adjustment
Correct the boiler draught
Adjust the burner
9.2
Burner will not start after normal use
9.3
Delayed ignition, burner starts; pulsation