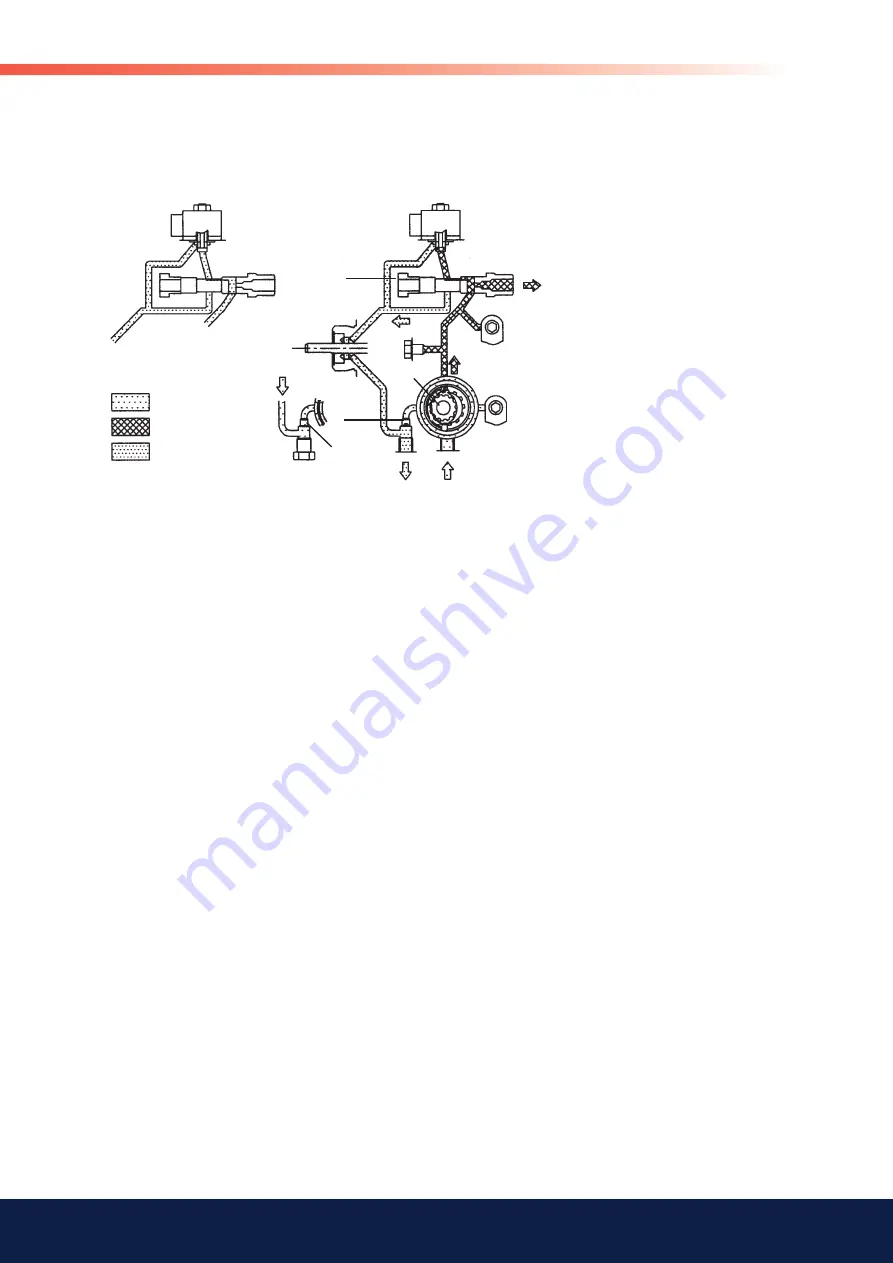
19
Bentone B 2
General
Oil under suction
Oil under pressure
By-passed oil
returned to tank,
or to suction
Inlet
Shaft seal
Back to suction
Two pipe installation
One pipe installation
Return
Solenoid valve open
Solenoid valve closed
To
nozzle
Vacuum
gauge port
Return plugged
By-pass
plug
inserted
By-pass plug
removed
Gear-set
Pressure
adjustment
Side
pressure
port
Pressure
gauge
ports
5.1.5 Function AS47CK
Pump working method
The oil pump has a solenoid valve which regulates the closing of the oil low
and provides a crisp function independent of pump rpm.
The pump’s gear wheels draw oil from the tank through the integral ilter
and conveys the oil to the regulator valve which pressurizes the nozzle
connection.
The quantity of oil that does not go to the nozzle connection is led through the
valve back to the return line, or in the case of a one-pipe installation, back to
the suction connection in the gear wheel pump.
- Two-pipe system
When the solenoid valve is not activated, the return plug channel between the
pressure side and the return side of the pressure valve is open. No pressure
will be built up to open the pressure valve, regardless of gear wheel pump
rpm. When the solenoid valve is activated, the return plug channel is shut.
The gear wheel pump’s rotation at full rpm quickly builds up the pressure
necessary for opening the valve and provides a sharp opening action.
- One-pipe system
Purging of the oil line system is not automatic in the one-pipe system; open
the manometer connection for purging.
Shut-down
When the burner stops, the solenoid valve opens the return plug channel
and drains oil to the return line. At that same moment the nozzle line is
closed. This provides a sharp cut-off. The on and off functions can be
controlled independent of motor rpm, and react very quickly. When the
solenoid valve is not activated torque is low up to full motor rpm.
Summary of Contents for Bentone B 2 KA
Page 2: ......
Page 10: ...10 Bentone B 2 General 8 9 10 11 12 16 15 14 13 1 2 3 4 5 7 6 1 5 Description...
Page 32: ...32 Bentone B 2 General...
Page 33: ...33 Bentone B 2 General...
Page 34: ...34 Bentone B 2 General...
Page 35: ......
Page 36: ...Enertech AB P O Box 309 SE 341 26 Ljungby www bentone se www bentone com...