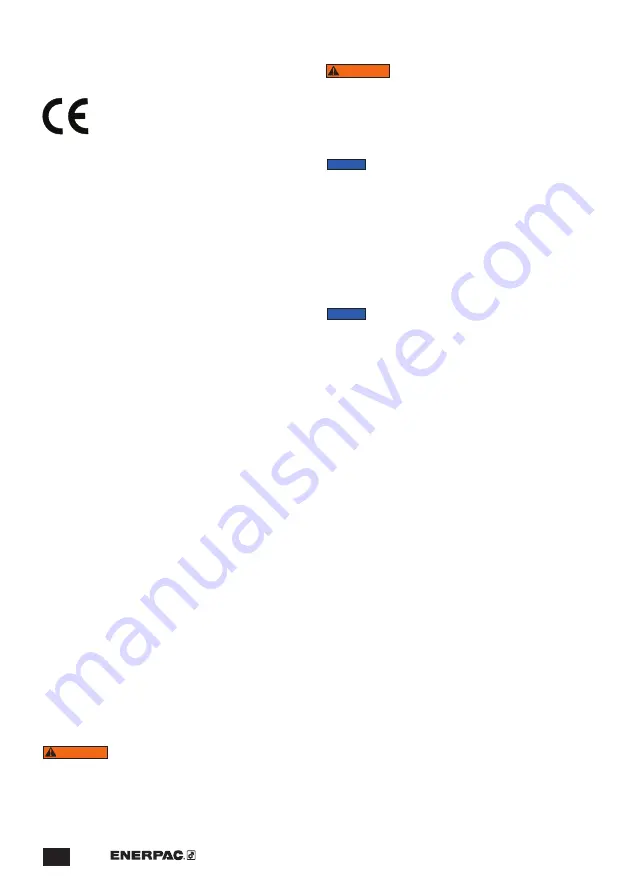
8
3.0 CONFORMANCE TO NATIONAL AND
INTERNATIONAL STANDARDS
Enerpac declares that this product has been
tested and conforms to applicable standards
and is compatible with all CE requirements.
A copy of an EU Declaration of Conformity is
enclosed with each shipment of this product.
4.0 DESCRIPTION
Enerpac models EWCH90 and EWCH140 are fixed-
head hydraulic cutters designed to cut round electrical
and communications cables.
The cutter contains two blades, one fixed and one
moving. The moving blade is actuated by an integral
double-acting hydraulic cylinder. The double-acting
design ensures positive blade return and also helps
prevent jamming or sticking.
Hydraulic power is supplied by an Enerpac hydraulic
pump, which is sold separately from the cutter. Refer to
Section 6.1 for additional pump information.
See Figure 1 for a description of cutter major features and
typical items included in the shipment. Refer to Section
2.0 for maximum cutting capacities, specifications and
dimensions.
5.0 RECEIVING INSTRUCTIONS
Visually inspect all components for shipping damage.
Shipping damage is not covered by warranty. If shipping
damage is found, notify carrier at once. The carrier is
responsible for all repair and replacement costs resulting
from damage in shipment.
6.0 SET-UP
6.1 Hydraulic Pump Requirements
The cutter must be used in conjunction with a specially
designed hydraulic pump (sold separately). This pump
contains unique valving and controls that are specific
to the cutter.
Refer to the pump instruction sheet for detailed
pump setup and operation instructions. Also refer to
Section 6.4 of this manual for additional details.
6.2 Hydraulic Connections
A high pressure twin hydraulic hose assembly connects
the pump control valve to the cutter. The hoses are
included as part of a hose subassembly that also
contains an electrical cable for the cutter controls. This
subassembly is not included with the cutter and must be
purchased separately.
To facilitate connections, quick-disconnect hydraulic
couplers are present on the hoses, the cutter, and on
the pump control valve.
NOTICE:
WARNING
Hydraulic oil can reach very high
temperatures even when the cutter is idle and
cutting force is not being applied. To prevent burns,
always use suitable personal protective equipment
when connecting or disconnecting couplers on a
cutter that has been in operation.
NOTICE:
WARNING
Never use any hydraulic component that
contains damaged hydraulic couplers. Never connect
or disconnect a hydraulic coupler if the hydraulic circuit
is pressurized. Failure to observe these instructions
may result in the uncontrolled release of pressurized
hydraulic oil. Skin penetration may occur. Death or
serious personal injury could result.
NOTICE
All hydraulic hoses and fittings used with the
cutter must be rated at 10,150 psi [700 bar] or above.
6.2.1 Connecting the Hydraulic Couplers
1. Be sure that pump motor is stopped.
2. Be certain there is no residual pressure in the
hydraulic circuit. If pressure is present, discharge the
pressure in accordance with the instructions in the
pump instruction sheet.
Repeat steps 3 through 6 for each hydraulic connection.
See Figures 2 and 3 for hookup details.
NOTICE
Before connecting hydraulic hoses, be certain
that the electrical cable (included in hose and cable
subassembly) is properly oriented. Note that electrical
connectors are different on cutter and pump ends.
3. Remove the coupler dust caps.
4. Inspect the couplers after removing the dust caps.
Remove any oil, dust or dirt.
5. Push the male and female couplers firmly together
until engagement occurs.
6. Screw the threaded collar of the female coupler fully
onto the threaded flange of the male coupler. Be sure
that no threads are visible.
6.2.2 Disconnecting the Hydraulic Couplers
1. Be sure that pump motor is stopped.
2. Be certain there is no residual pressure in the
hydraulic circuit. If pressure is present, discharge the
pressure in accordance with the instructions in the
pump instruction sheet.
Repeat steps 3 through 5 for each hydraulic connection.
See Figures 2 and 3.
3. Unscrew the threaded collar of the female coupler
from the threaded flange of the male coupler.
4. Disconnect the couplers. Remove any oil, dust or dirt.
5. Reinstall the coupler dust caps.
6.3 Electrical Connections
An electrical cable connects the pump electrical circuits
to the push button controls mounted on the cutter. This
cable is included as part of the hydraulic hose and
electrical cable subassembly.
Connect the electrical cable as described in the following
steps. See Figures 2 and 3.
1. Be sure that pump is disconnected from AC power
supply.
2. Connect one end of the electrical cable to the electrical
connector at the pump electrical control box.
3. Connect the other end of the electrical cable to the
electrical connector at the cutter.
Summary of Contents for EWCH140
Page 19: ...Notes ...
Page 20: ...WWW ENERPAC COM ...