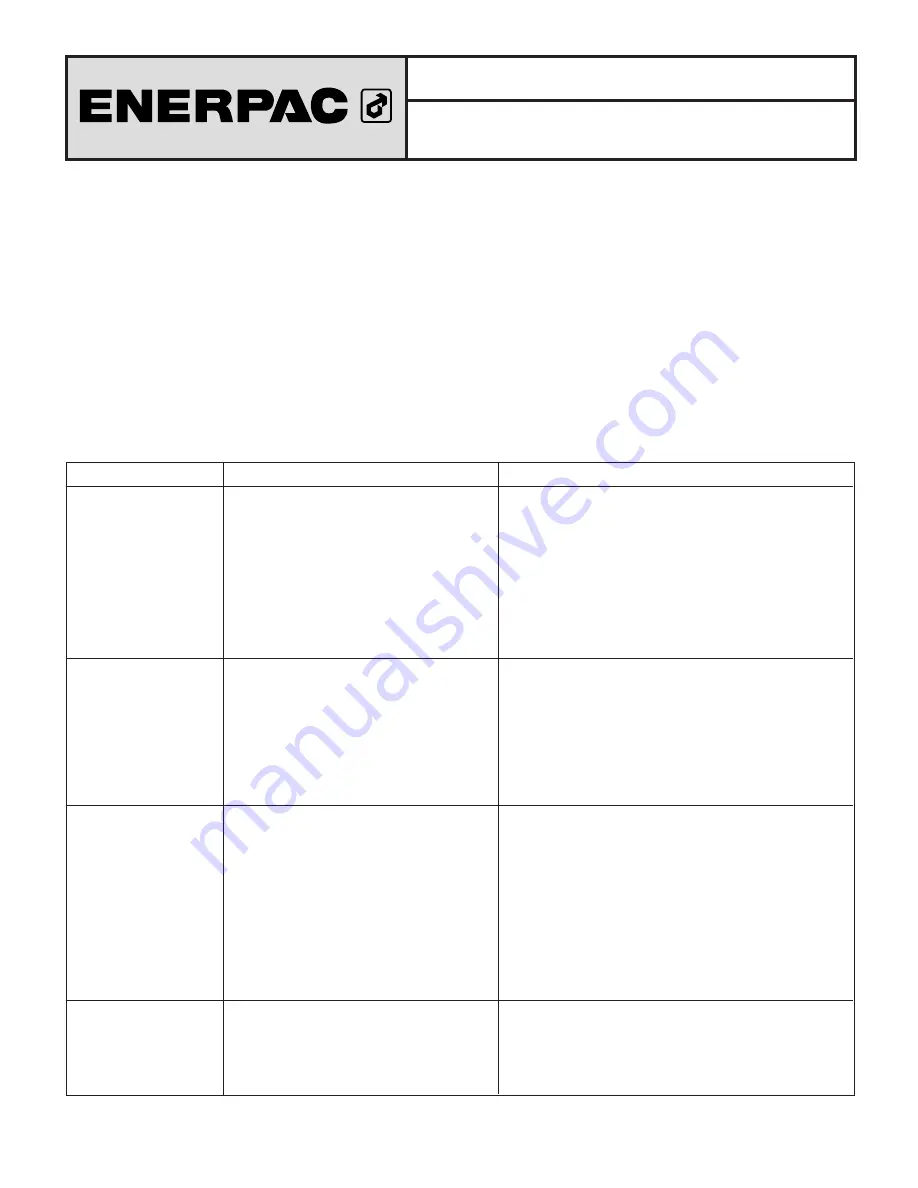
10
®
SERVICE INSTRUCTIONS:
These Service instructions are intended to be used by qualified personnel at Authorized Enerpac
Service Centers. Users of Enerpac equipment should see the pump Instruction Sheet for installation, operation, and maintenance
information.
■
REQUIRED TOOLS AND TEST EQUIPMENT:
✓
Hydraulic hand pump capable of 10,000 psi
✓
Test bench with sump, ammeter, V152 valve,
flow meter, and test cylinder
✓
High pressure gauge (0-15,000 psi)
✓
High pressure hose (10,000 psi working pressure rating)
✓
Torque wrench (torque rating)
✓
Magnet to remove check balls
✓
O-ring pick
✓
Flat bottom punch 5/32"
✓
Flat bottom punch 11/64"
✓
White Assembly grease
✓
Allen wrench 5 mm
✓
Enerpac Hydraulic Oil
✓
VM2, 3 way, 2 position, directional control valve
✓
Hydraulic press
✓
Seat assembly tool #DC9505816 (drawing available
from Enerpac)
✓
Retaining Ring Tool #AT0229 (drawing available from
Enerpac)
1.0 TROUBLESHOOTING
Problem
Possible
Cause
Action
Motor current draw is
excessive or trips
circuit breaker.
Pump runs and delivers
flow, but will not build
pressure.
Low or no flow at
0 psi.
Pump fails to maintain
pressure.
a) Low voltage at pump.
b) Defective motor.
c) Bypass valve malfunction.
d) Damaged or worn gear pump.
e) Power cord damaged or wiring incorrect.
a) Defective or misadjusted external
relief valve.
b) Oil leaks from one or more
components within the reservoir.
c) Valve malfunction or improper
adjustment.
d) Bypass valve worn.
a) Motor rotation reversed (3-phase only).
b) Bypass valve is malfunctioning.
c) Pump component parts are leaking.
d) Oil intake screen is clogged with debris.
e) Gear pump malfunction.
f) Direction valve malfunction or improper
adjustment.
a) Defective directional valve.
b) Defective final outlet check.
c) Oil leaks from one or more
components within the pump
assembly or valve assembly.
a) Check voltage at pump while pump is at operating
pressure. If below 90% of rated line voltage replace
extension cord with heavier gauge and/or move to
another electric circuit.
b) Remove the motor. Test and replace if necessary.
c) Inspect, test, and adjust the bypass valve. Replace or
rebuild if required.
d) Remove and inspect the gear pump.
Replace if necessary.
e) Replace or repair as necessary.
a) Inspect the relief valve. Reset or replace if required.
b) Perform the back-pressure test.
c) Adjust or repair.
d) Remove and inspect the bypass valve. Rebuild or
replace if necessary.
a) Reverse 2 of 3 motor wire connections.
b) Remove and inspect the bypass valve. Rebuild or
replace if necessary.
c) Perform the backpressure test to isolate leaks.
d) Remove the pump from the reservoir and inspect the
intake screen. Flush components of contamination.
Replace damaged components and hydraulic oil.
e) Disassemble the pump and inspect the gear pump.
Replace if necessary.
f) Adjust or repair.
a) Repair or replace.
b) Repair or replace.
c) Remove the pump from the reservoir and perform the
back-pressure test outlined in test procedure.
Service Instructions
Z-Class Pump 3-6
L2596
Rev. G
10/13