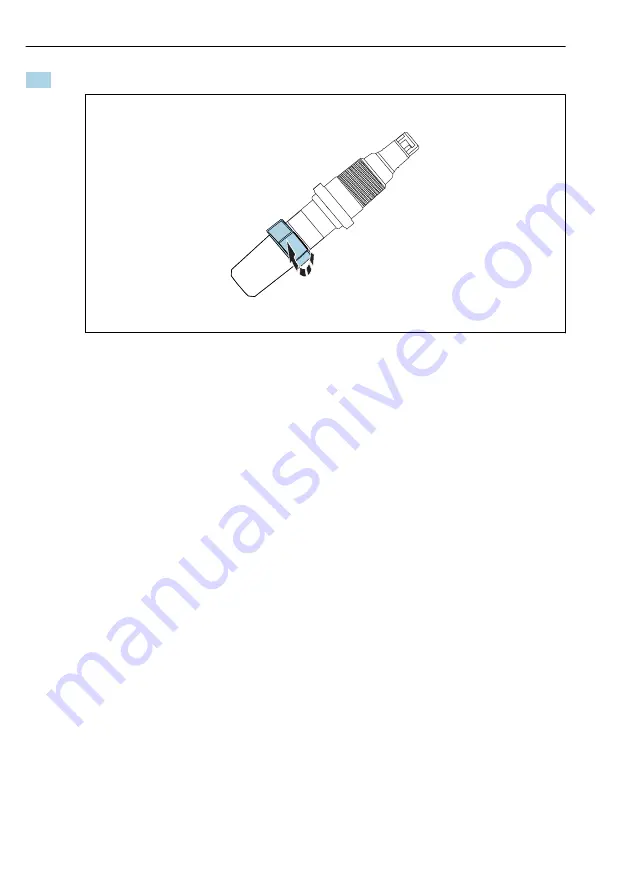
Maintenance
CCS120D
32
Hauser
3. Secure protection cap by rotating the top part of the protection cap.
A0037887
14
Securing protection cap by rotating the top part
9.2.5
Regenerating the sensor
During measurement, the electrolyte in the sensor is gradually exhausted due to chemical
reactions. The gray-brown silver halide layer that is applied to the counter electrode at the
factory continues to grow during sensor operation. However, this has no effect on the reaction
taking place at the working electrode.
A change in the color of the silver halide layer indicates an effect of the reaction that is taking
place. Carry out a visual inspection to ensure that the gray-brown color of the counter
electrode has not changed. If the color of the counter electrode has changed, e.g. if it is
spotted, white or silvery, the sensor must be regenerated.
‣
Send the sensor to the manufacturer for regeneration.
Summary of Contents for CCS120D
Page 2: ......
Page 39: ...CCS120D Installation and operation in hazardous environment Class I Div 2 Endress Hauser 39 ...
Page 42: ......
Page 43: ......