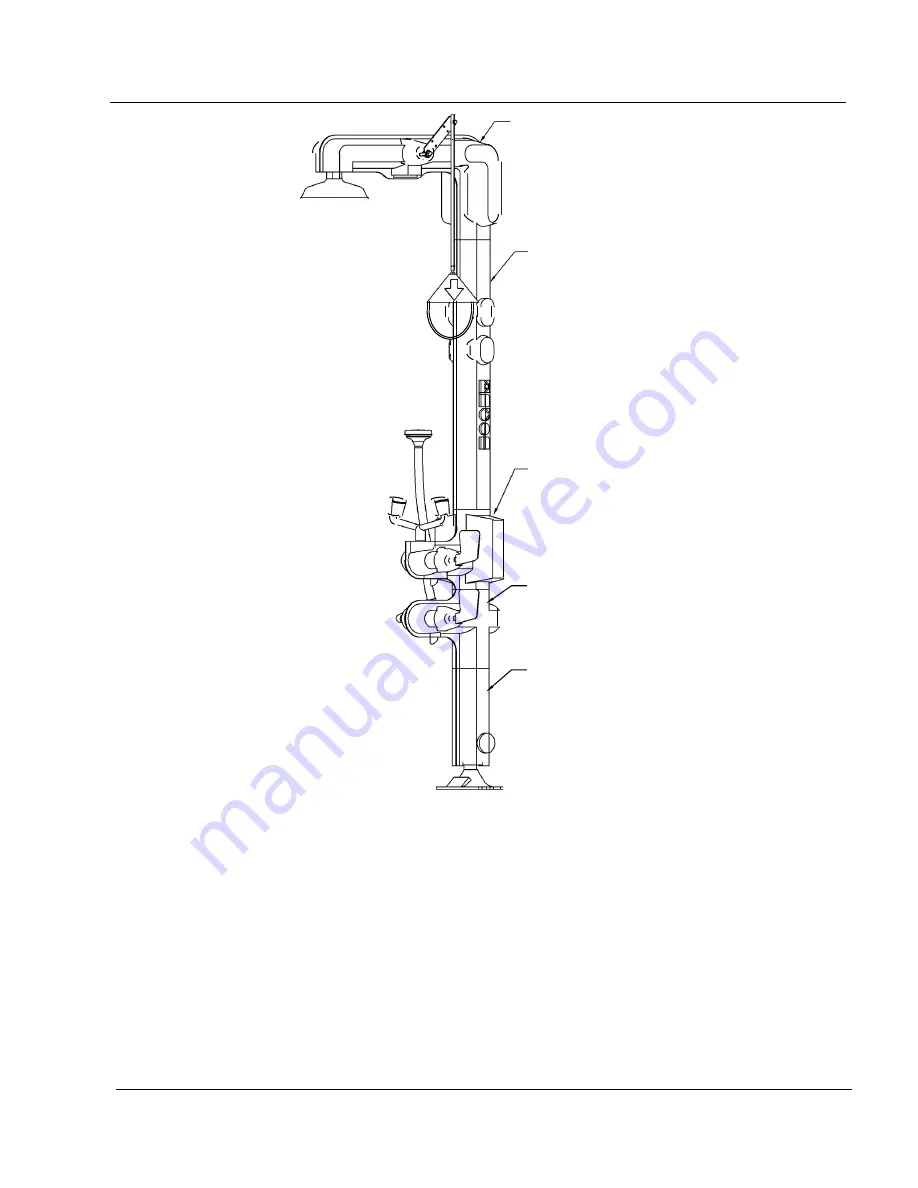
4-2
Therma-Flow
®
PLUS
IOM 09900002
Revision C 08/15/21
© 2021, Encon Safety Products, Inc.
4 MAINTENANCE AND REPAIR
OVERHEAD 24"
UPPER VERTICAL
EYEWASH FOUNTAIN
DRENCH HOSE FOUNTAIN
LOWER VERTICAL
Figure 4-1. Therma-Flow® Plus ABS Cover Assembly
To inspect the covers:
1. Inspect the ABS covers and ensure they are not cracked and intact to maintain
thermal integrity of the unit.
2. Inspect the closure strips and seals and ensure they are tight.
3. Make sure all grommets that seal the protrusions are in place and secure. Dead
air space is essential to keep the unit freeze protected.