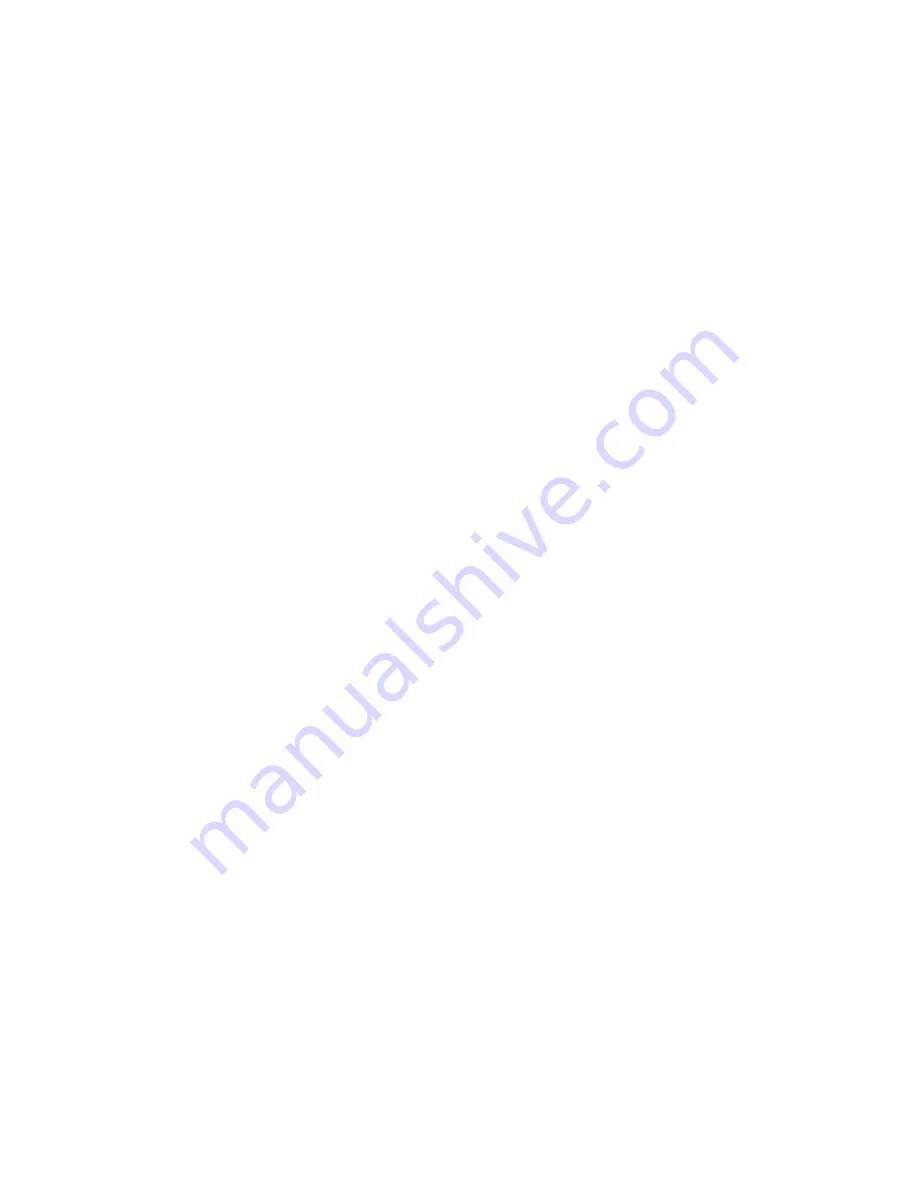
Page 15
R-3451
TROUBLE-SHOOTING
SYMPTOMS - POSSIBLE CAUSES AND CORRECTIONS
IMPORTANT: Operating heater where impurities in air exist may create odors. Cleaning supplies, paint, paint remover, cigarette smoke, cements and
glues, new carpet or textiles, etc., create fumes. These fumes may mix with combustion air and create odors.
1. When ignitor button is pressed, there is no spark at ODS/
pilot.
a. Ignitor electrode positioned wrong - Replace ignitor.
b. Ignitor electrode broken - Replace ignitor.
c. Ignitor electrode not connected to ignitor cable - Reconnect
ignitor cable.
d. Ignitor cable pinched or wet - Free ignitor cable if pinched by
any metal or tubing. Keep ignitor cable dry.
e. Broken ignitor cable - Replace ignitor cable.
f. Bad piezo ignitor - Replace piezo ignitor.
2. When ignitor button is pressed, there is spark at ODS/pilot,
but no ignition.
a. Gas supply turned off or manual shutoff valve closed - Turn
on gas supply or open manual shutoff valve.
b. Control knob not in PILOT position - Turn gas control knob
to PILOT position.
c. Control knob not pressed in while in PILOT position - Press
in control knob while in PILOT position.
d. Air in gas lines when installed - Continue holding down
control knob. Repeat igniting operation until air is removed.
e. Depleted gas supply - Contact local gas company.
f. ODS/pilot is clogged - Clean ODS/pilot or replace ODS/pilot
assembly.
g. Gas regulator setting is not correct - Replace gas regulator.
3. ODS/pilot lights but flame goes out when control knob is
released.
a. Control knob not fully pressed in - Press in control knob
fully.
b. Control knob not pressed in long enough - After ODS/pilot
lights, keep control knob pressed in 30 seconds.
c. Safety interlock system has been triggered (thermostat models
only) - Wait one minute for safety interlock system to reset.
Repeat ignition operation.
d. Manual Shutoff valve not fully open - Fully open manual
shutoff valve.
e. Thermocouple connection loose at control valve - Hand
tighten until snug, then tighten 1/4 turn more.
f. Pilot flame not touching thermocouple, which allows
thermocouple to cool, causing pilot flame to go out. This
problem could be caused by either 1) low gas pressure -
Contact local gas company or 2) dirty or partially clogged
ODS/pilot - Clean ODS/pilot or replace ODS/pilot assembly.
g. Thermocouple damaged - Replace thermocouple.
h. Control valve damaged - Replace control valve.
4. Main burner does not light after ODS/pilot is lit.
a. Main burner orifice clogged - Clean main burner or replace
main burner orifice.
b. Main burner orifice diameter is too small - Replace main
burner orifice.
c. Inlet gas pressure is too low - Contact local gas company.
5.
Pilot burning, no gas to burner, valve knob "ON", on/off
switch "ON."
a. "On/Off" switch, wall switch, remote control or wires
defective - Check "on/off" switch and wires for proper
connections. Place jumper wires across terminal at switch -
if burner comes on, replace defective switch. If OK, place
jumper wires across switch wires at gas valve-if burner
comes on, wires are faulty or connections are bad.
b. Thermopile may not be generating sufficient millivolts - If
the pilot flame is not close enough physically to the thermopile,
clean the ODS/pilot.
- Be sure the wire connections from the thermopile at the gas
valve terminals are tight and the thermopile is fully inserted
into the pilot bracket.
- Check the thermopile with a millivolt meter. Take the
reading at TH-TP & TP terminals of the gas valve. The meter
should read 350 millivolts minimum, while holding the valve
knob depressed in the PILOT position, with the pilot lit, and
the ON/OFF switch in the OFF position. Replace the faulty
thermopile if the reading is below the specified minimum.
- With the pilot in the ON position, disconnect the thermopile
leads from the valve. Take a reading at the thermopile leads.
The reading should be 350 millivolts minimum. Replace the
thermopile if the reading is below the minimum.
c. Defective valve - Turn valve knob to "ON." Place ON/OFF
switch to "ON." Check with millivolt meter at thermopile
terminals. Millivolt meter should read greater than 200
millivolts. If the reading is okay and the main burner does not
ignite, replace the gas valve
d. Plugged main burner orifice - Check main burner orifice for
blockage and remove.
6. Delayed ignition of main burner.
a. Manifold pressure is too low - Contact local gas company.
b. Main burner orifice clogged - Clean main burner and main
burner orifice.
7. Main burner backfiring during combustion.
a. Main burner orifice is clogged or damaged - Clean main
burner and main burner orifice or replace main burner orifice.
b. Damaged main burner - Replace damaged main burner.
c. Gas regulator defective - Replace gas regulator.
8. Yellow flame in front section of main burner during main
burner combustion.
a. Not enough air - Check main burner for dirt and debris. If
found, clean main burner.
b. Gas regulator defective - replace gas regulator.
9. Slight smoke or odor during initial operation.
a. Residues from manufacturing processes and logs curing -
Problem will stop after a few hours of operation.
10. Heater produces a whistling noise when main burner is lit.
a. Turning control knob to HI position when main burner is cold
- Turn control knob to LO position and let warm up for a
minute.
b. Air in gas line - Operate main burner until air is removed from
line. Have gas line checked by local gas company.
c. Air passageways on heater blocked - Observe minimum
installation clearances (see page 4).
d. Dirty or partially clogged main burner orifice - Clean main
burner and main burner orifice or replace main burner orifice.
11. Heater produces a clicking/ticking noise just after main
burner is lit or shut off.
a. Metal expanding while heating or contracting while cooling
- This is common with most heaters. If noise is excessive,
contact service person.
12. Heater produces unwanted odor.
a. Heater burning vapors from paint, hair spray, glues, cleaners,
chemicals, new carpet, etc. - Open window to ventilate room.
Stop using odor causing products while heater is operating.
b. Low fuel supply - Refill supply tank.
c. Gas leak - Locate and correct all leaks.
13. Heater shuts off in use (ODS operates).
a. Not enough fresh air is available - Open window and/or door
for ventilation.
b. Low line pressure - Contact local gas company.
c. ODS/pilot is partially clogged - Clean ODS/pilot.
14. Gas odor even when control knob is in OFF position.
a. Gas leak - Locate and correct all leaks.
b. Control valve defective - Replace control valve.
15. Gas odor during combustion.
a. Foreign matter between logs and main burner - remove
foreign matter.
b. Gas leak - Locate and correct all leaks.
Summary of Contents for CIVF-25-2
Page 5: ...Page 5 R 3451 Figure 1 Figure 2 Figure 3 ...
Page 18: ...Page 18 R 3451 ...