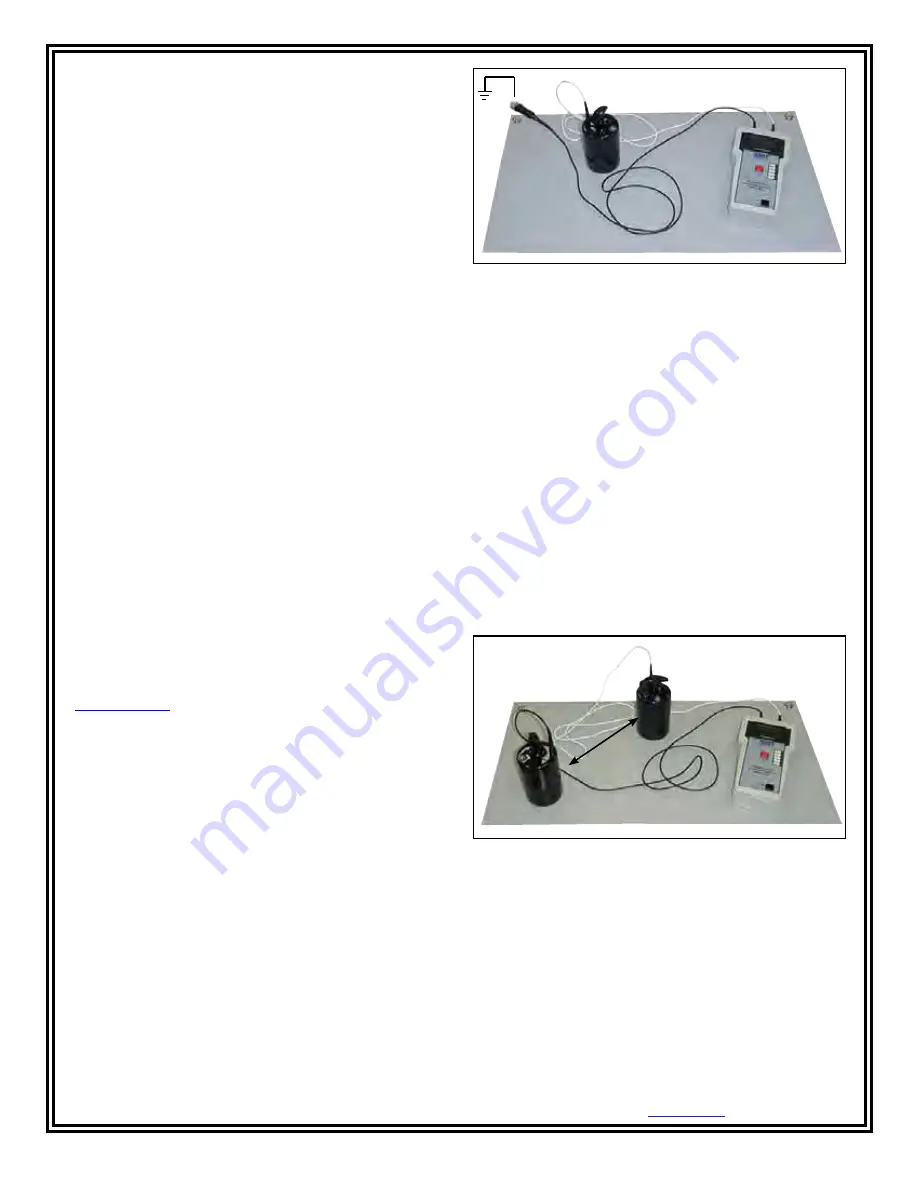
TB-6520
Page 4 of 7
Test Lab Test Procedure Guideline
For test lab use of ESD Worksurfaces, Floor Materials,
Footwear, Garments, or Seating, best advice is to follow
procedures in applicable ESD Association standards (see
above) which include details regarding:
• Cleaning (For example per S4.1 “The test specimens and
electrodes shall be cleaned twice with a minimum 70%
isopropanol-water solution using a clean, low-linting cloth
each time). Allow to dry.
• Environmental chamber (For example per S4.1 control
relative humidity to 12 ±3% RH and 50 ±5% RH and
temperature to 23 ±1 degrees C)
• Specimen support surface (For example per S4.1
greater than 1.0 x 10E12 ohms such as PMMA, PTFE or
polycarbonate)
• Specimen Pre-Conditioning (For example per S4.1 at 23
±1 degrees C; 3 specimens at 12 ±3% relative humidity
for 72 hours minimum, and 3 specimens at 50 ±5%
relative humidity for 72 hours minimum)
• Reporting Test Results, for example per S4.1 Reporting
Test Results, Report:
• Minimum, median and maximum readings for both
resistance-to-groundable point and point-to-point
resistance in ohms at low relative humidity
• Minimum, median and maximum readings for both
resistance-to-groundable point and point-to-point
resistance in ohms at moderate relative humidity
• Temperature
• Relative humidity
• Actual duration of conditioning
• Test equipment used
Periodic Checks of Installed Product Test
Procedure Guideline
The ESD Association lists test procedures and
troubleshooting tips in Compliance Verification ESD TR53.
We recommend this document be purchased from
Measure RTG Resistance to Ground
Test Procedure in reference with ANSI/ESD S4.1 section
6.4 Periodic Worksurface Testing:
• Do not clean the surface
• Remove from the surface only those items that might
interfere with the test.
• ESD sensitive devices shall also be removed
• The black sensing test lead with shielded plug should go
to equipment ground or a groundable point
• Use one Electrode on other test lead and place Electrode
the farthest convenient point on the surface
• Press button and hold Test Button until measurement is
displayed
• Perform additional measurements placing Electrode on
the most commonly used or most worn area
If measurement is outside acceptable limits, clean surface
and retest to determine if cause of failure is insulative dirt
layer or the ESD contol item. Note: Use an ESD cleaner
containing no insulative silicone.
Measure RTT Resistance Between Two Points
on the Surface
• Do not clean the surface
• Remove from the surface only those items that might
interfere with the test.
• ESD sensitive devices shall also be removed
• Use two 5 Pound Electrodes, place in the most commonly
used portion of the surface 10" apart (2" from any edge,
3" from any groundable point) for worksurface and 3' for
flooring
• Press Test button and hold Button until measurement is
displayed
• If the most used portion is not obvious, use two points
near the center of the surface
If measurement is outside acceptable limits, clean surface
and retest to determine if cause of failure is insulative dirt
layer or the ESD contol item. Note: Use an ESD cleaner
containing no insulative silicone.
© 2010 DESCO INDUSTRIES INC.
Employee Owned
Figure 3. Setting up for RTG testing.
10”
Figure 4. Setting up for RTT testing. (Electrodes are to be
about 10" apart for worksurfaces and about 3' for flooring)
Reporting and Using Test Results
Different standards have different requirements; use
requirements as specified in user’s ESD control plan.
Examples are:
Per ANSI/ESD 4.1 (worksurfaces), Report:
• RTG maximum and minimum values measured for
resistance-to-ground
• RTT maximum and minimum values measured for
point-to-point resistance in ohms
EMIT
- 3651 Walnut Avenue, Chino, CA 91710 • (909) 664-9980 • Fax (909) 627-7449 • Website: