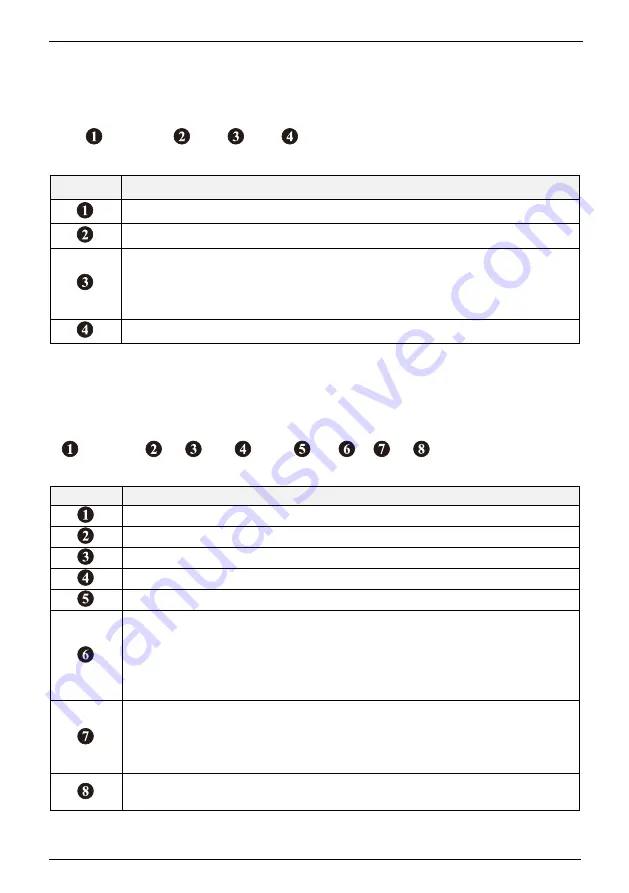
EMSD5 AC Servo Manual
Chapter 2 Servo Specifications
7
2.2 Servo Drive Naming Rule
EMSD5 - A S 040
Serial No.
Definition
EMSD5 series ac servo drive.
A and B frame
S: Simple load pulse
H: Heavy load pulse
E: Ether CAT
The branch power range: 040: 400W; 075: 750W.
2.3 Servo Motor Naming Rule
EM - 60 S 024N 30 S 2 2
Serial No.
Definition
EMHEATER Servo Motor
Flange: 60(mm),80(mm), 110(mm),130(mm)
Rated voltage: 220V(S)
Rated torque(
×
0.1N.m): 048=4.8N.m.
Rated speed(
×
100rpm): 30=3000rpm.
Encoder resolution:
S: 17 bit absolute encoder
I: 2500ppr incremental encoder
W: with battery
R: resolver
1: No
2: with oil seal
3: with brake
4: with oil seal and brake
1: Flat without keys.
2: Flat with keys and screw thread