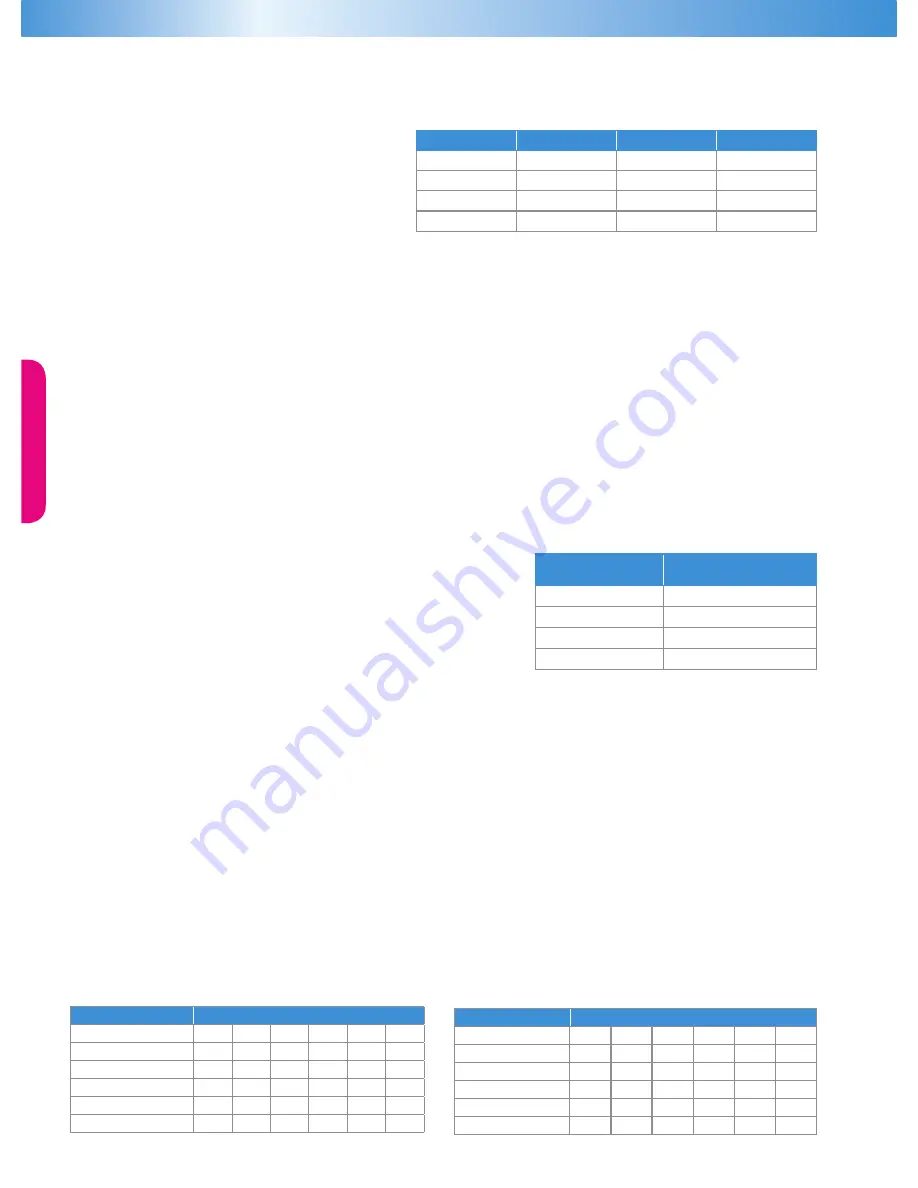
9
Electrical Connection
Power Supply
The ZX condensing unit electrical connection to the power
supply must be made by qualified technicians, who should
refer to the electrical diagrams located inside the electric
connection panel. The units are designed for below power
supply at ± 10% voltage tolerance. The circuit breaker must
be switched off before opening the front panel.
Electrical Wiring
Before commissioning, ensure that the neutral “N” wire is
connected to the terminal block (“N” furthest to the right). After proper connection of the ZX condensing unit, the control LED on
the power board and control board will light. For more details, see wiring diagram in Appendix.
Refrigeration Connections
Refrigeration Piping Installation
All interconnecting pipes should be of refrigeration grade, clean, dehydrated and must remain capped at both ends until installation.
Even during installation, if the system is left for any reasonable period of time (say two hours), pipes should be re-capped to prevent
moisture and contaminants from entering the system.
Do not assume that the service connection sizes on the unit (at the service valves) are the correct size to run your interconnecting
refrigeration pipes. The service valve sizes have been selected for convenience of installation and in some cases (larger units) these
may be considered too small. However for the very short pipe run within our units, these service connection sizes are adequate. All
interconnecting pipes should be sized to satisfy the duty required.
Usually the suction line is insulated, but the liquid line is not. However the liquid line can pick up additional heat from the ambient
and adversely affect the sub-cooling desirable for the liquid refrigerant before it enters the expansion valve.
The pipe should be sized to ensure optimum performance and good oil return. The sizing must also take into account the full capacity
range through which this particular unit will need to operate.
Pipe runs should be kept as short as possible, using the minimum number
of directional changes. Use large radius bends and avoid trapping of oil and
refrigerant. This is particularly important for the suction line. The suction
line should ideally slope gently towards the unit. Recommendation slope is
1/200~1/250. P traps, double risers and reduced pipe diameters may be required
for suction lines where long vertical risers cannot be avoided. All pipes should
be adequately supported to prevent sagging which can create oil traps. The
recommended pipe clamp support distance is shown in the table.
ZXL Liquid Line Insulation
ZXL liquid line should be insulated with a 19 mm insulation
thickness. Temperature could be as low as –15°C.
Codes
HZ
Phase
Voltages
PFJ
50
1
220/240
TFD
50
3
380/420
TF7
60
3
380
TF5
60
3
200/230
Tube Size
Max distance between
2 clamp support
12.7mm (1/2 inch)
1.20 m
16.0mm (5/8 inch)
1.50 m
22.0mm (7/8 inch)
1.85 m
28.5mm (1 1/8 inch)
2.20 m
Typical Liquid Line Temperature
o
C
R22
Ambient
°
C
Evap Temp
o
C
20
27
32
38
43
48
-40
-11
-3
7
7
11
14
-35
-8
-1
9
9
13
16
-30
-4
2
12
12
16
19
-25
0
5
14
14
19
23
-20
5
9
18
18
22
26
R404A
Ambient
°
C
Evap Temp °C
20
27
32
38
43
48
-40
-8
-1
3
8
13
19
-35
-4
2
6
11
15
21
-30
0
6
9
13
18
23
-25
5
10
13
17
21
26
-20
9
14
17
20
24
30
ZXL-LT Unit (Liquid Line Temperature)
Vapor Injection: Specific Application Tips
ZXL-LT CDU
ZXL-LT CDU applies vapor injection technology. As explained in the previous section, vapor injection improves LT operational
efficiency and provides a reliable LT envelope. Vapor injection sub cools the main liquid line using the economizer cycle. The sub
cooling of liquid line calls for some specific application tips which are applicable only for ZXL-LT CDU. They are;
1. Liquid line pipe connecting the CDU service valve to the evaporator expansion valve has to be well insulated separately. The
recommended insulation thickness is 12.5 mm (1/2 inches)
2. The lower liquid in temperature can increase the evaporator expansion valve capacities. Please follow valve manufactures
recommended liquid temperature correction factors for proper selection of evaporator expansion valve.