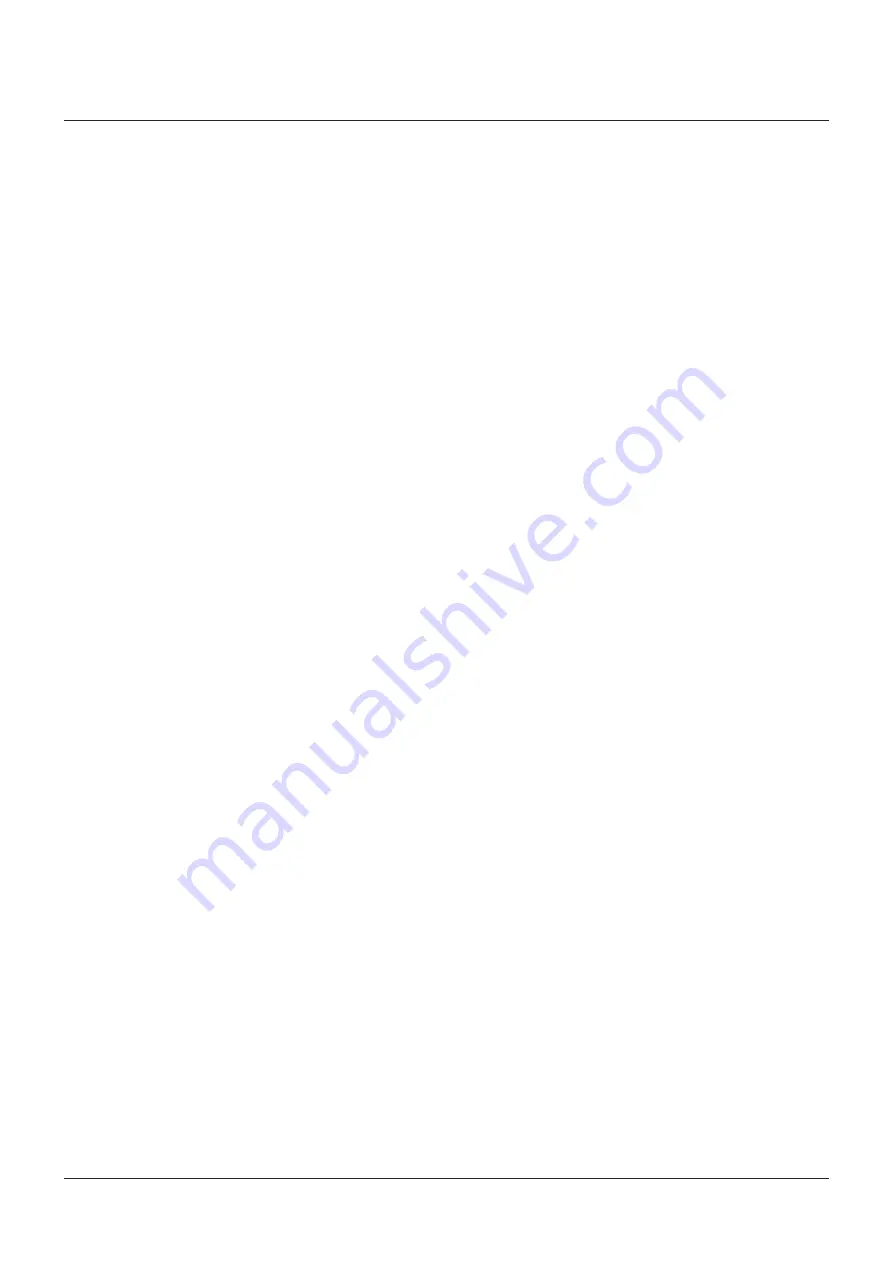
7
YARWAY
9100 SERIES ARC
®
VALVE
INSTALLATION, OPERATION AND MAINTENANCE INSTRUCTIONS
1" to 1 ½" [25 to 40 mm] valve sizes
1. All parts must be clean prior to reassembly.
2. Insert the bypass bushing without the O-ring
in the valve body to guide the disc during the
lapping. Lap the disc to the body per step 6
above.
3. Install the snubber seal assembly (42) in the
groove on the disc (33) per step 7 above.
4. Assemble the disc-bypass bushing parts
(Items 33, 34, 36, 37, 38, 39, 40, and 42)
as follows. Assemble all parts except the
spiral ring (38) and lay the assembly on a
flat surface with the bottom of the disc up.
Compress the spring by pushing down on
the spring retainer until the groove in the
bottom of the disc is exposed. Install the
spiral ring (38) by separating the coils and
inserting one end of ring into groove and
spiral each turn progressively over the shaft.
Slowly release the load on the retainer.
5. To prepare the disc-bypass bushing
assembly for installation in the valve body,
the spring (37) must be compressed and
restrained. There are two spring restraining
methods, one uses a tool and the other a
dowel pin. Using the disc-bypass bushing
assembly illustrations as a guide, visually
compare the parts to the illustrations and
determine if the provisions are for the old or
new method. The old method has a hole in
both the disc and bypass bushing to accept
a tool. The new method has only a hole in
the disc for a dowel pin. Both types of spring
restrainers will be held in place by the spring
load. Prepare the disc-bypass bushing
assembly for installation in the valve body as
described by 5a or 5b below as applicable.
a. For the old restraining method, a tool
must be fashioned by bending a metal
rod as shown. Compress and rotate the
disc and bypass bushing together to align
the assembly holes. Insert the spring
restrainer tool in the assembly holes and
release the spring load.
b. For the new restraining method, provide
the dowel pin as shown. Compress the
disc and bypass bushing together until
the pin assembly hole is exposed. Insert
the spring restrainer pin in the assembly
hole and release the spring load.
6. Visually align the centerline of the threaded
outlet hole in the bypass bushing (34) with
the body bypass outlet hole centerline.
Insert the disc-bypass bushing in the body
carefully so as not to knock the spring
restrainer loose.
7. Rotate and push or pull on the disc to
accurately align the bypass outlet holes.
Shine a light in the bottom of the disc hole
while looking through the body bypass outlet
to check alignment.
8. Install the bypass tube (35) into the body
outlet, threaded end first. Thread the tube
into the bypass bushing (34) and tighten to
approximately 20 ft/lbs [27 N•m] torque
using a spanner wrench or a 1” x 2” x ⅛”
[25 x 50 x 3 mm] thick steel plate. Stake the
body into the bypass tube slots.
9. Remove spring restrainer, tool or dowel
as applicable, by pushing on the bottom of
the disc to release the spring load. The tool
should become loose for removal. The pin
should fall out. Ensure restrainer pin either
falls out or is removed from the valve body
before placing the valve back in service.
10. Lubricate, assemble, and check valve
stroke per steps 9 and 10 under the 2” - 8”
instructions.