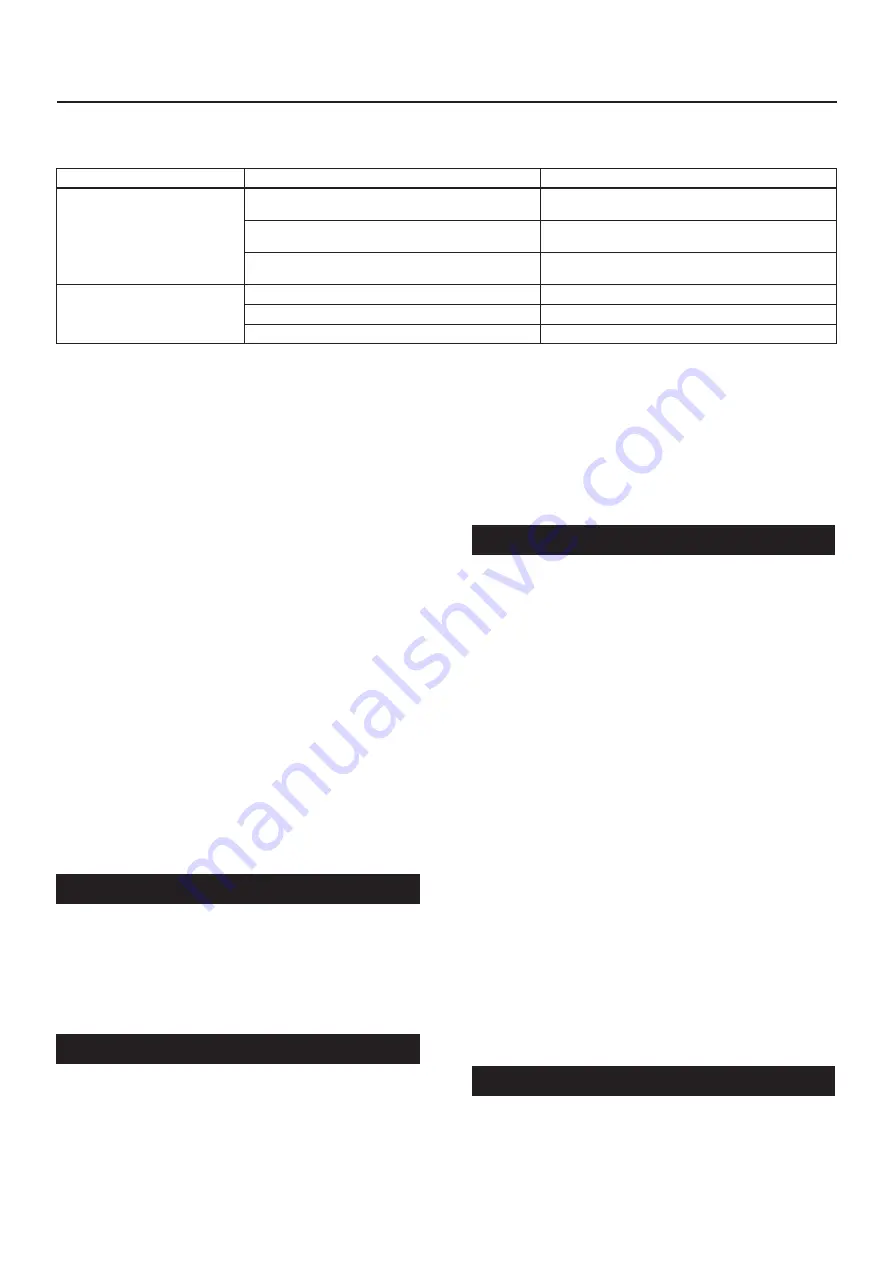
Type BM9
13
To change pilot-loaded slam-shut controller setpoints
(overpressure and/or underpressure), adjust the
pilot setpoints. Refer to pilot’s instruction manuals
for details.
Monitor outlet pressure with a test gauge during
the adjustment.
Range Setting
The reset differential indicates the minimum value to
be considered with respect to downstream pipeline
pressure set point for proper resetting of the controller.
See Figure 12.
Example: Downstream pipeline pressure set point
15 bar / 218 psig.
Choose OS9/84X-R with blue spring for overpressure
and red spring for underpressure, see Tables 7 and 8.
The reset differential ∆Pwo is 3.0 bar / 43.5 psig and
∆P
wu
is 6.0 bar / 87.0 psig.
So, the overpressure set value should be
18 bar / 261 psig (15 bar + 3 bar = 18 bar or
218 psig + 43.5 psig = 261 psig) or higher, and
underpressure set value should be 9 bar / 131 psig
(15 bar - 6 bar = 9 bar or 218 psig - 87 psig = 131 psig)
or lower.
Shutdown
▲
WARNING
To avoid personal injury resulting from
sudden release of pressure, isolate the
slam-shut valve from all pressure before
attempting disassembly and release
trapped pressure from the equipment
and pressure line.
△
CAUTION
In any installation, it is important to
slowly open and close the valves and to
vent the outlet pressure before venting
the inlet pressure to prevent damage
caused by reverse pressurization of the
pilot or main valve.
1. Slowly close the valves in the following order:
a. Inlet block valve
b. Outlet block valve
c. Control line valve(s), if used.
2. Open the vent valves to depressurize the system.
Maintenance
▲
WARNING
To avoid personal injury resulting
from sudden release of pressure,
isolate the slam-shut valve from the
system pressure and release trapped
pressure from the equipment and
pressure line before attempting
maintenance operation.
Use proper lifting techniques, when
lifting the body and spacer (keys 1
and 17).
The optional drainage plug at the bottom
of the valve, shown in Figure 13, must
not be removed unless the pressure
in the valve is completely released.
If violated, serious injury may occur
due to sudden release of extremely
high pressure.
The slam-shut valve parts are subject to normal wear
and must be inspected periodically and replaced
as necessary. The frequency of inspection and
replacement depends on the severity of service
conditions and on applicable federal, state and local
codes and regulations.
Use Torque Specifications
(Table 5) for proper torque values.
Main Valve (See Figures 14, 15 and 16)
▲
WARNING
Installation, operation and maintenance
procedures performed by unqualified
personnel may result in improper
Table 6.
Troubleshooting Type BM9 Slam-Shut Valve
SYMPTOMS
CAUSE
ACTIONS
Slam-shut device does not remain set
The sensing line to port (A) of slam-shut controller
is not connected properly
Check the sensing line connections (A)
Downstream pressure coincides with
the maximum or minimum slam-shut settings
Check slam-shut controller settings
Damaged Diaphragm (key 62) on Type OS9/80X-R
Lip seal (key 66) on Types OS9/84X-R and OS9/88X-R
Replace the diaphragm on Type OS9/80X-R
Replace the lip seal on Types OS9/84X-R and OS9/88X-R
Sleeve does not seal properly
Worn seal gaskets
Check gaskets and replace if necessary
Dirt deposit on sleeve
Check sleeve and clean / replace if necessary
Shaft and Roller (keys 7 and 50) are damaged
Check shaft and roller and replace if necessary