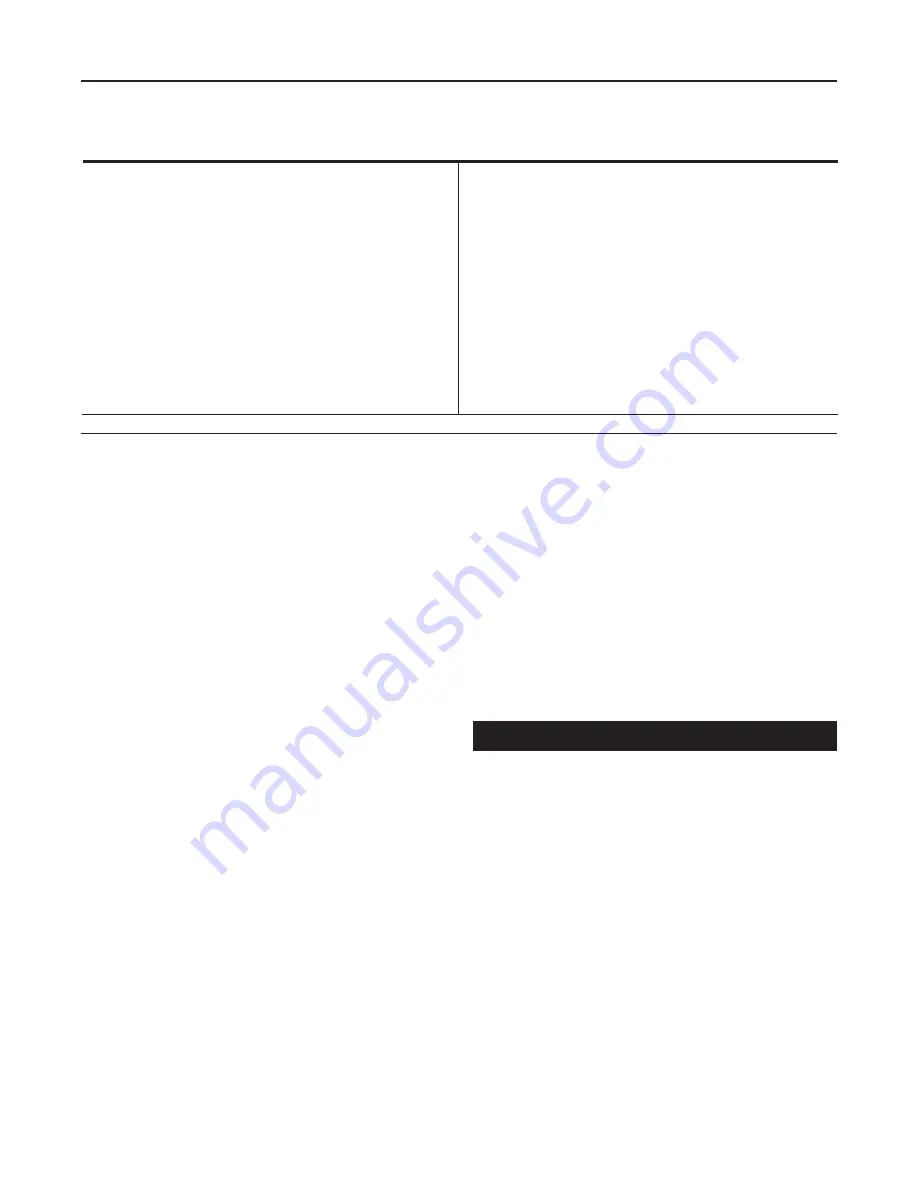
Specifications
The specifications section on this page provide the ratings and other specifications for the Max-Flo Series.
1. The pressure/temperature limits in this Instruction Manual and any applicable standard or code limitation should not be exceeded.
Available Configurations
Type HC-15:
Steam pressures to 15 psig / 1.03 barg
Type HC-30:
Steam pressures to 30 psig / 2.07 barg
Type HC-75:
Steam pressures to 75 psig / 5.17 barg
Type HC-125:
Steam pressures to 125 psig / 8.62 barg
Type HC-175:
Steam pressures to 175 psig / 12.1 barg
Maximum Operating Pressure
(1)
175 psig / 12.1 barg
Maximum Allowable Pressure
(1)
175 psig / 12.1 barg
Maximum Operating Temperature
(1)
Saturated at pressure
Maximum Allowable Temperature
(1)
377°F / 192°C
Materials of Construction
Body and Cover:
Cast iron
Valve, Pin and Seat:
Hardened Stainless steel
Float:
Stainless steel
Lever Assembly:
Stainless steel
Thermostatic Air Vent:
Stainless steel cage and
Thermal element
Cover Bolts:
Grade 5
Baffle:
Stainless steel (NPS 2-1/2 / DN 65
units only)
Maintenance
▲
WARNING
To avoid personal injury, property
damage or equipment damage caused
by sudden release of pressure or
explosion of accumulated gas, do
not attempt any maintenance or
disassembly without first isolating the
equipment from system pressure and
relieving all internal pressure from
the equipment.
When checked regularly and properly maintained,
the Max-Flo Series Float and Thermostatic Traps will
provide optimum performance.
specifications or where conditions
exceed any ratings of the adjacent
piping or piping connections.
To avoid such injury or damage,
provide pressure-relieving or
pressure-limiting device.
Max-Flo Series should be installed in an accessible
position and location for easy servicing. The trap seat
rating stamped on the nameplate, must be equal or
greater than the maximum pressure differential across
the trap. Install the trap straight and in a level position
to ensure proper installation.
1. Determine where to install trap, based on the
following requirements:
a. The trap must be located as closed as possible,
and below the equipment to be drained.
b. The trap must be in a straight run of horizontal
pipe as shown in Figure 2, and pitched to allow
condensate to flow into trap inlet, and away
from trap outlet.
c. Allow for enough space around the trap for
servicing which may include removal of the
body or cover, depending on the model you
are installing.
2. Install a Y-strainer with a Blowdown valve in a
pipe, ahead of steam trap. This prevents dirt from
entering trap.
3. Install union fittings and a shutoff valve in inlet
pipe and outlet pipe. This allows trap to be isolated
when servicing.
4. Install a test valve in outlet pipe, and cap it. This
allows trap to be tested. Cap is used as safety
precaution when unit is not being tested.
5. Blowdown piping using full steam pressure for
five minutes. This cleaning process will remove
debris from pipe and oil from system.
2
Max-Flo Series