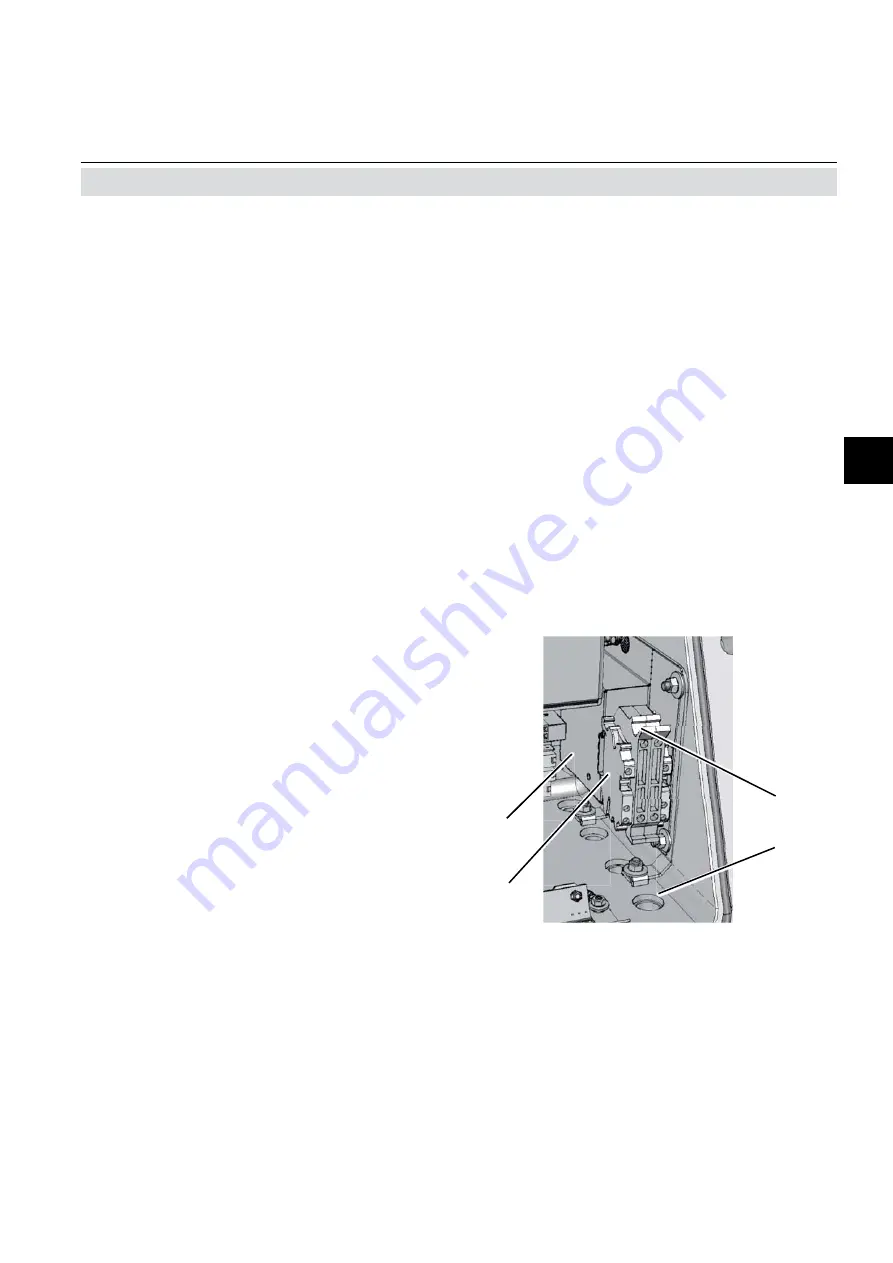
Emerson Process Management GmbH & Co. OHG
1-13
1
Techn. Description
X-STREAM X2FD
Instruction Manual
HASXMDE-IM-EX
01/2015
Fig. 1-6: Power terminals / fuse holders
1.7 Technical Data
Power Connection
Connection via internal screw terminals near
cable entries, (
fi
g. 1-6).
Cross section:
max. 4 mm
2
(10 AWG), end sleeves not
required
Cable entry via
1 cable gland, classi
fi
ed IP 68 or suitable
conduit with metric-to-NPT adaptor
Permissible outer cable diameter for power
cord:
see cable gland / conduit speci
fi
cation
Power supply fuses
The power terminals integrate fuse holders.
Fuse ratings:
AC 230 V / T 4 A / 5x20 mm
1
Power terminals with integrated
fuse
holders
2
Protective earth terminal (PE)
3
Power cable entry
4
EMI power supply
fi
lter
3
2
4
1