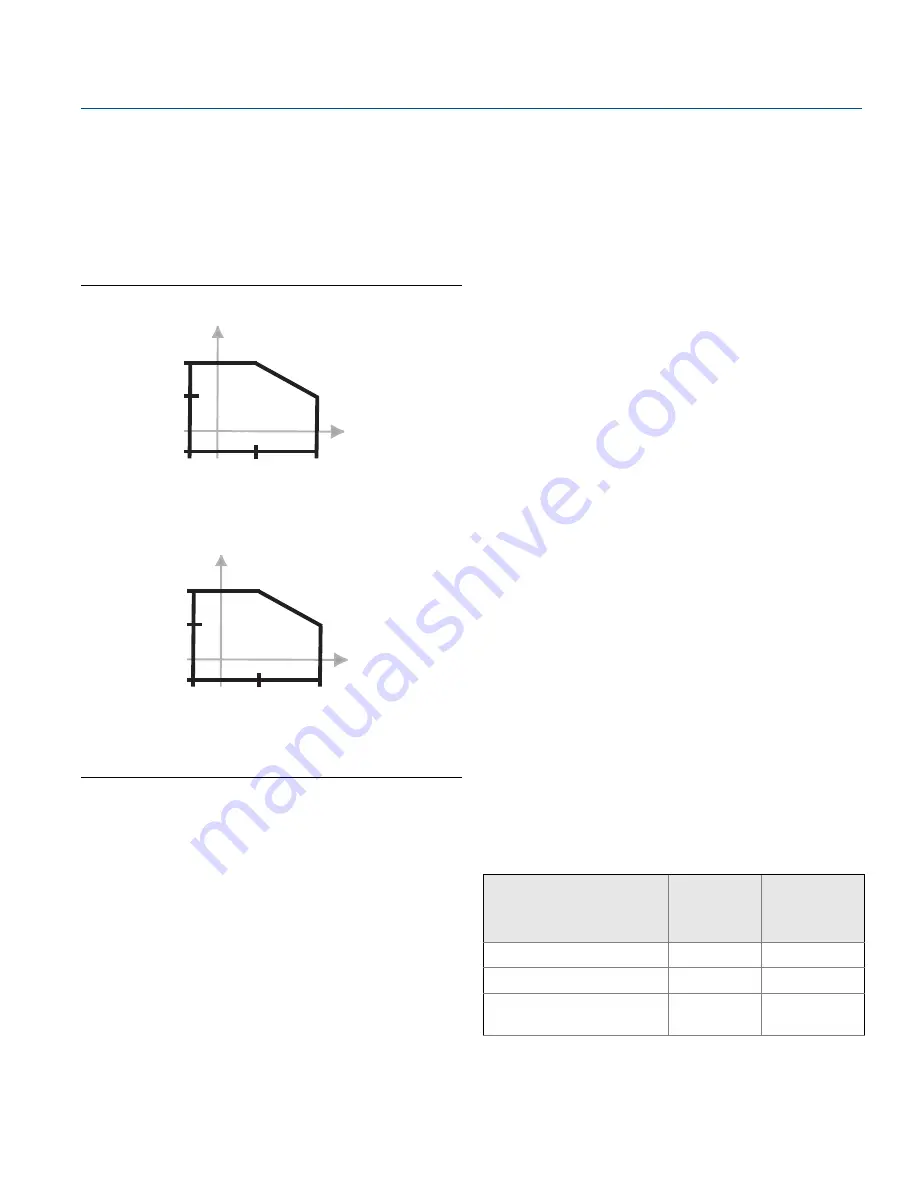
Specifications and Reference Data
January 2019
Reference Manual
00809-0100-4130, Rev DC
Specifications and Reference Data
41
Minimum and maximum operating
temperatures
for operating temperatures.
The ambient temperature for a 8/16 mA cassette is
limited to 158 °F (70 °C) in potentially explosive dust
atmospheres.
Figure A-2. Operating Temperatures
A.1.4 Performance
Hysteresis (water)
0.1 in. (± 2.5 mm)
Switching point (water)
0.5 in. (13 mm) from tip of fork (if vertical installation) or
from edge of fork (if horizontal installation) – this will vary
with different liquid densities
Liquid density requirement
Minimum standard density is 37.5 lb/ft
3
(600 kg/m
3
).
Minimum density is 31.2 lb/ft
3
(500 kg/m
3
) when ordered
with the low-density range option.
Liquid viscosity range
Up to 10000 cP (centiPoise) when operating in the normal
mode.
Up to 1000 cP (centiPoise) when operating in self-check
mode.
Solids content and coating
The maximum recommended diameter of solid particles in
the liquid is 0.2 in. (5 mm) when used in normal mode only.
For coating products, avoid bridging of forks.
Switching delay
There is a user-selectable 0.3, 1, 3, 10, 30 seconds delay for
dry-to-wet and wet-to-dry switching.
CIP (Clean In Place) and SIP (Steam In
Place) cleaning
Withstands cleaning routines up to 275 °F (135 °C).
NACE
NACE compliance to MR0175 / ISO 15156 or MR0103,
depending on the option code selected for the model
number.
Operating modes
Table A-4. Operating Modes
176 (80)
176
(80)
-40 (-40)
-94
(-70)
500
(260)
Process Temperature °F (°C)
A
m
b
ient
T
e
m
p
er
at
u
re
°
F
(°
C
)
149 (65)
32 (0)
32
(0)
2130***E
176 (80)
176
(80)
-40 (-40)
-40
(-40)
356
(180)
Process Temperature °F (°C)
A
m
b
ien
t T
e
m
p
er
at
u
re
°
F
(°
C
)
122 (50)
32 (0)
32
(0)
2130***M
Fault conditions detected
Normal
mode (red
LED)
Self-check
mode (yellow
LED)
PCB control circuit corruption
Yes
Yes
External damage to fork
No
Yes
Internal wire
disconnection/break
No
Yes