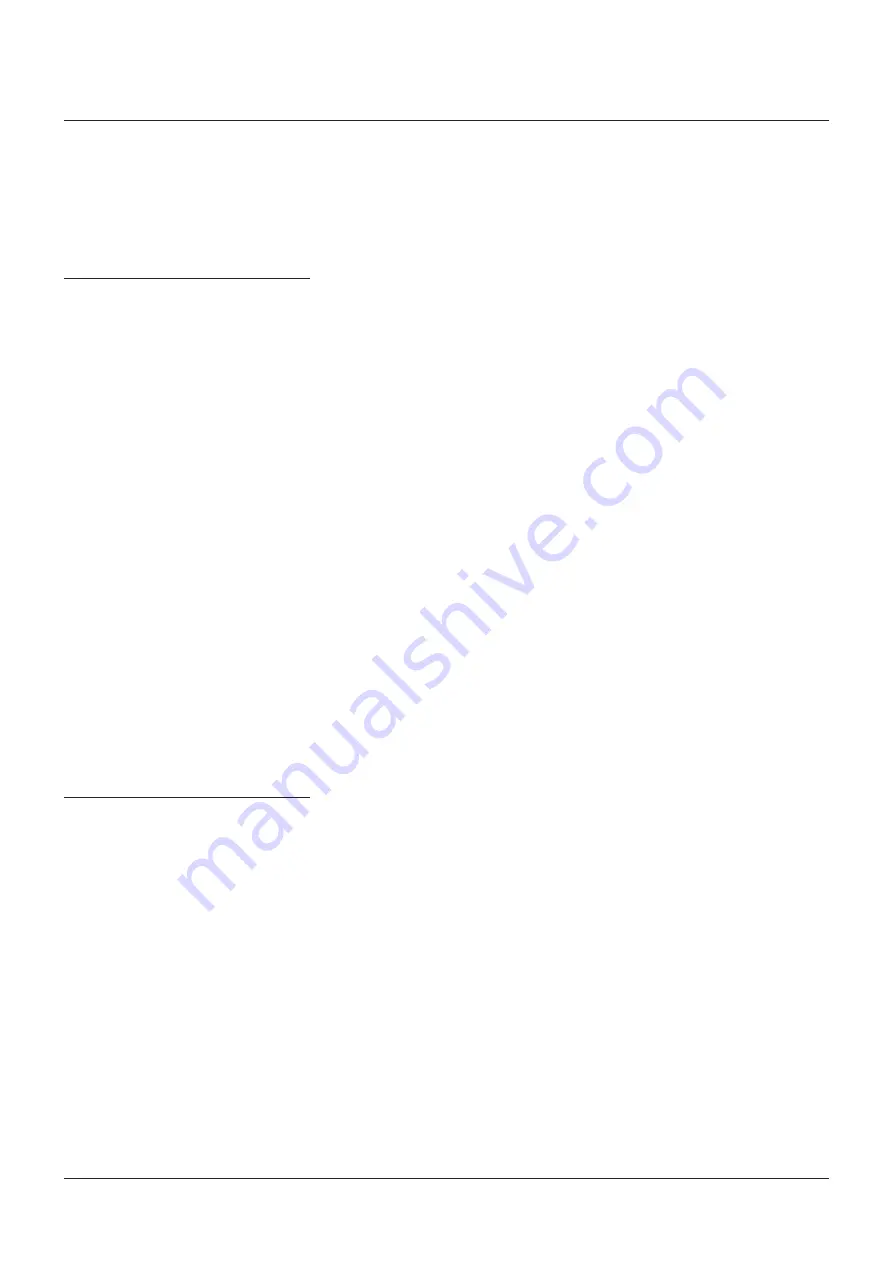
4
PENBERTHY
SERIES K3 GAGECOCKS
INSTALLATION, OPERATION AND MAINTENANCE INSTRUCTIONS
4.3 Guard rod installation
Guard rods (four required) are assembled
downward through upper gagecock with
swaged portion on rods at the top. Bottom of
rods are positioned into respective holes in the
lower gagecock rod star.
5 OPERATION
5.1 Pre-operational check
1. Assure that all installation procedures have
been completed.
2. Check to determine that all connections are
pressure tight.
5.2 Hydrostatic test
1. Take all precautions necessary to handle
the possibility of leakage during the test.
2. Hydrostatic pressure test all installations to
100 psig (690 kPaG) and correct any leakage
before proceeding.
5.3 Operating
Gagecock assemblies should be brought
into service slowly. The tubular glass used in
Penberthy gagecock sets is tempered and can
stand minimal thermal shock and mechanical
stress.
To avoid excessive thermal shock or
mechanical stress on the tubular glass, the
connecting gagecocks should be opened
slightly, and the tubular glass temperature and
pressure allowed to equalize slowly with the
vessel.
If the gagecocks are furnished with ball checks,
the gagecocks must be opened all the way after
the pressure and temperature have equalized
to permit operation of the automatic ball check
in the event of tubular glass breakage.
6 MAINTENANCE
Maintenance should only be undertaken by
qualified, experienced personnel who are
familiar with this equipment and have read and
understood all the instructions in this manual.
During system shut down, the gagecocks
should be left open to permit the gage to lose
pressure and cool with the rest of the system.
Failure to leave the gagecocks open during
system shut down will trap high-pressure fluid
in the gage.
CAUTION
Do not proceed with any maintenance unless the
gage has been relieved of all pressure or vacuum,
has been allowed to reach ambient temperature
and has been drained or purged of all fluids.
Failure to follow these instructions may result in
physical injury or property damage.
6.1 Preventative maintenance
The user must create maintenance schedules,
safety manuals and inspection details for each
specific installation of a gagecock set.
For purposes of maintenance on all
installations, the gagecocks should be
evaluated regularly by the user for signs of:
1. leakage around stem area.
2. internal stem leaks.
3. leakage around stuffing box connection.
4. internal or external corrosion.
The user must determine an appropriate
maintenance schedule necessary for his or her
specific application upon evaluation of their own
operating experience. Realistic maintenance
schedules can only be determined with full
knowledge of the services and application
situations involved.
6.2 Maintenance procedures
1. Stem packing leakage can often be stopped
by tightening the stem packing nut. If
leakage persists, the stem packing should
be replaced by following steps 'a' through 'c'
of Disassembly and step 'd' of Reassembly.
2. Signs of an internal stem leak are an
indication of a worn or damaged stem or seat.
a. To replace the stem, follow Disassembly
steps 'a' through 'd' and Reassembly
steps 'a' through 'd'.
b. To renew the seat surface, follow
Disassembly steps 'a' through 'd'. Renew
seat by using a fine lapping compound
and a mandrel the same size, shape and
seat angle as the stem. Flush gagecock
body clean and reassemble by following
steps 'a' and 'd' of Reassembly.
Note:
series K3 gagecocks have an integral
seat. Gagecock body must be replaced when
seat becomes worn or damaged beyond repair.
3. Signs of leakage around the stuffing box
indicate worn out glass packing or improper
compression of glass packing. To replace
glass packing, follow Disassembly steps 'a',
'b' and steps 'e' through 'j' and Reassembly
steps 'a', 'b', and 'e' through 'k'. In the event
of improper compression, leakage can be
stopped by tightening gage coupling nut.
4. Signs of internal or external corrosion
could be an indication of a misapplication.
An investigation should be carried out
immediately to determine the cause of
the problem. It is the user's responsibility
to choose a material of construction
compatible with both the contained fluid and
the surrounding atmosphere in the specific
application.
5. For broken sight glass replacement, follow
Disassembly steps 'a', 'b', and 'e' through
'j' and Reassembly steps 'a', 'b' and 'e'
through 'k'.
Safety instructions
New glass packing must be used when
replacing glass.